Mastering Weld Sizes
An Essential Introduction
Dive into the world of welding precision with our comprehensive guide on weld sizes. Understanding the significance of weld sizes is crucial for welders, engineers, and inspectors alike. From determining weld dimensions to their impact on joint strength and performance, we cover it all. Explore the implications of weld sizes across various welding processes and learn best practices for achieving optimal results.
Whether you are a novice or seasoned professional, this guide will equip you with the knowledge and skills to excel in the art of welding.
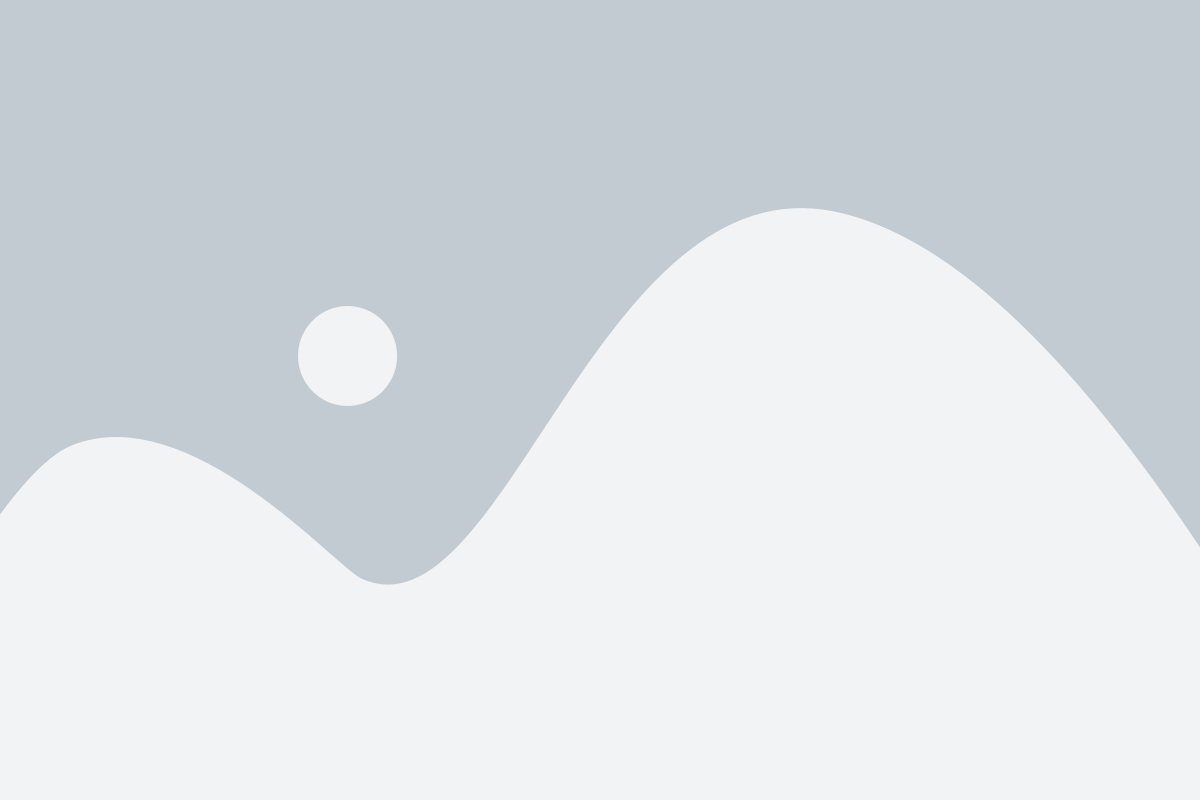
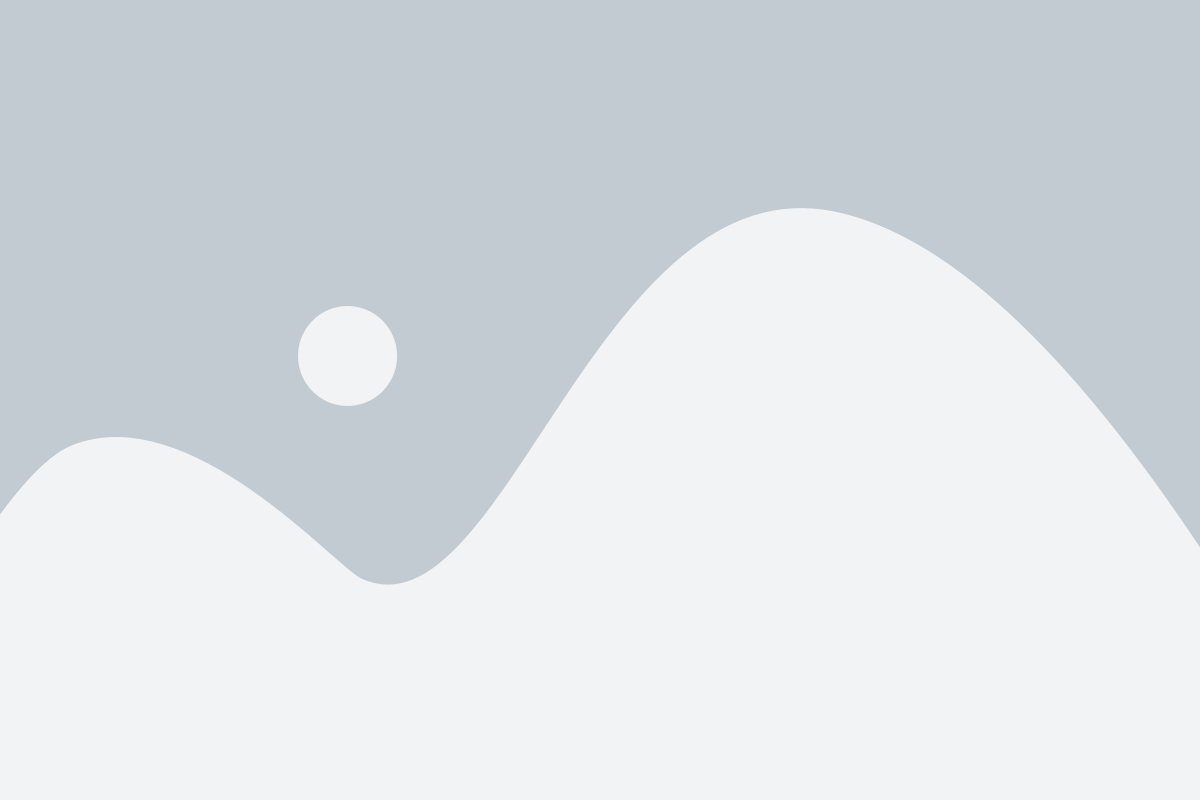
Concern
Significance of Weld Sizes
Structural Integrity: Weld sizes directly impact the structural integrity of welded joints, ensuring they can withstand mechanical stresses and loads.
Safety Assurance: Properly sized welds enhance safety by reducing the risk of premature failure or fracture, crucial in industries where human lives and assets are at stake.
Compliance with Standards: Adherence to specified weld sizes is essential for meeting industry standards and regulatory requirements, ensuring compliance with safety and quality protocols.
Uniform Stress Distribution: Well-proportioned weld sizes facilitate even stress distribution across the joint, minimizing the likelihood of stress concentration and subsequent failure.
Enhanced Performance: Optimal weld sizes contribute to improved performance characteristics, such as fatigue resistance, ductility, and overall durability of welded structures.
Cost Efficiency: By accurately sizing welds according to design specifications, wastage of materials and resources is minimized, leading to cost-effective fabrication processes.
Quality Assurance: Consistently sized welds indicate a high level of craftsmanship and attention to detail, instilling confidence in the quality of the welded components or structures.
Operational Reliability: Weld sizes play a crucial role in ensuring the reliability and longevity of welded assemblies, reducing the need for frequent maintenance or repair.
Precision Engineering: Understanding and controlling weld sizes demonstrate precision engineering practices, reflecting professionalism and expertise in the welding field.
Industry Competitiveness: Mastery of weld sizing techniques enhances competitiveness in the industry by delivering superior quality products and services that meet or exceed customer expectations.
Weld Sizes
Factors and Considerations
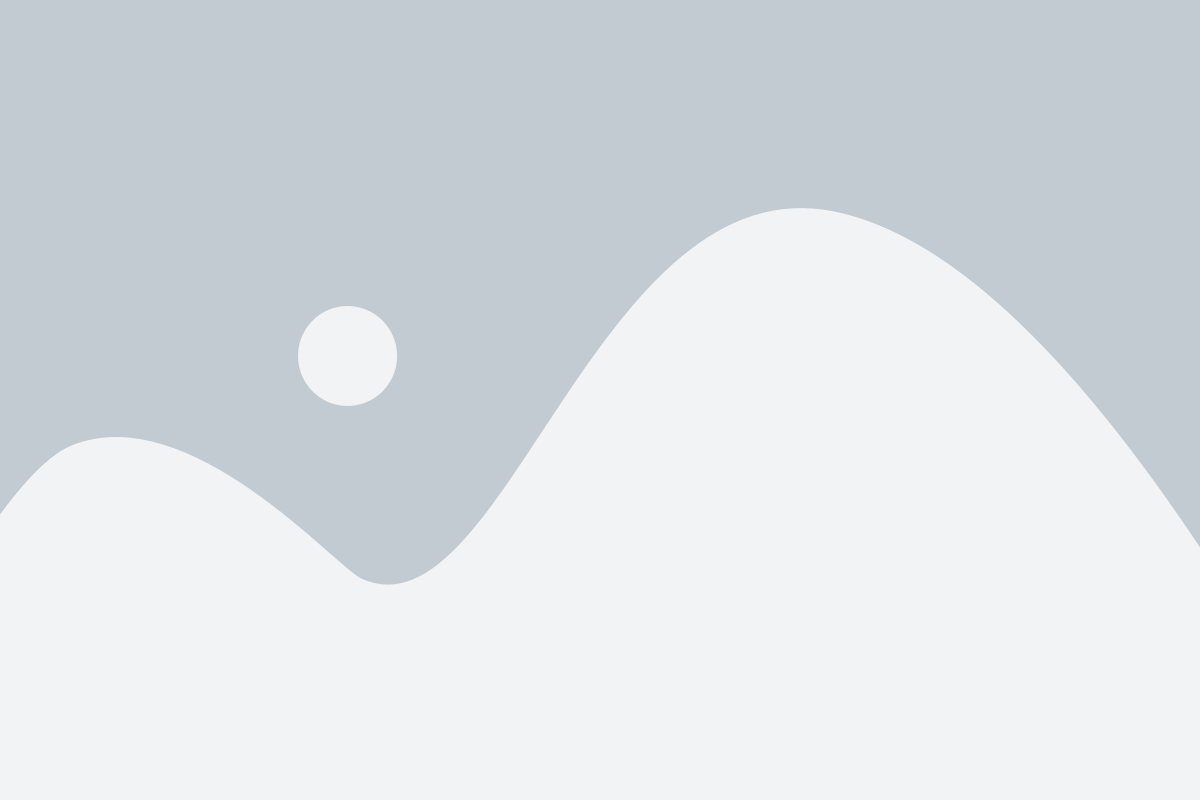
Design Throat Thickness of Full Penetration Butt Weld
The design throat thickness of a full penetration butt weld refers to the theoretical thickness of the weld at its root. It is calculated based on the thickness of the thinnest member being welded and is used for design and analysis purposes.
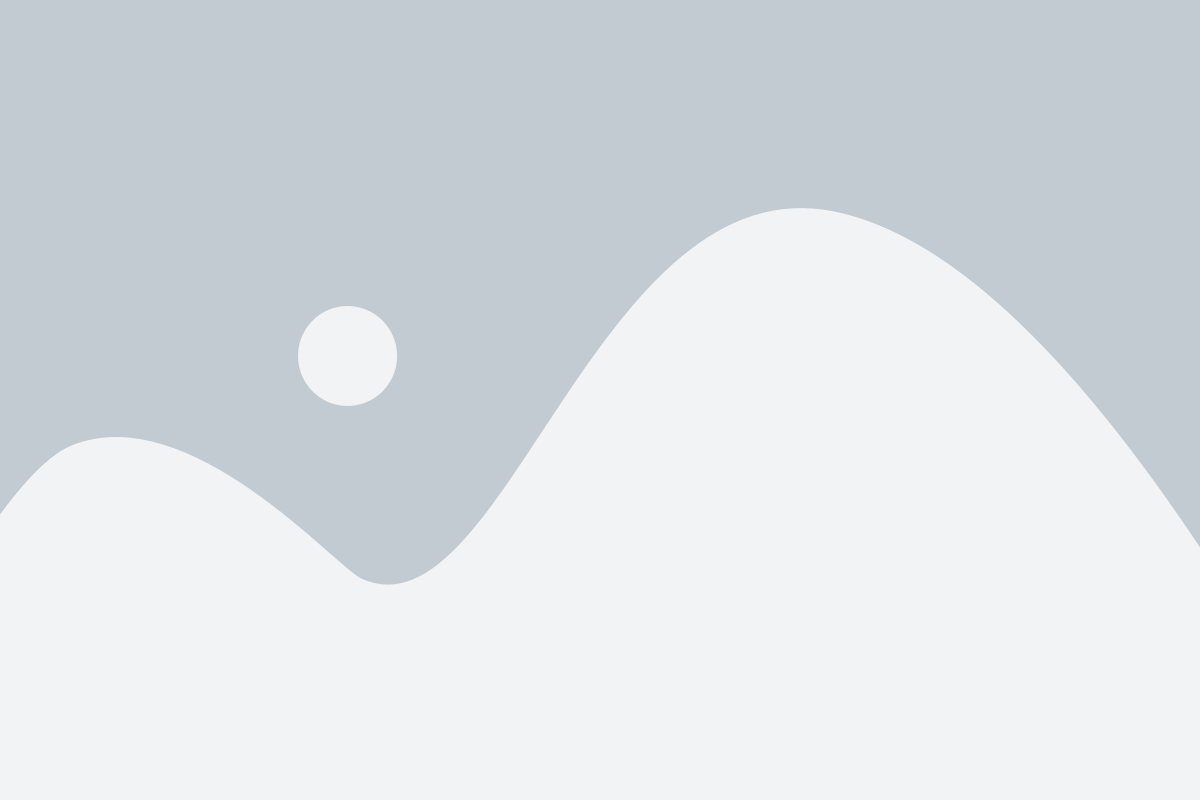
Actual Throat Thickness of Full Penetration Butt Weld
The actual throat thickness of a full penetration butt weld is the measured thickness of the weld at its root after welding has been completed. This measurement is typically performed using calibrated instruments or weld gauges and may differ from the design throat thickness due to factors such as welding process variations and material properties.
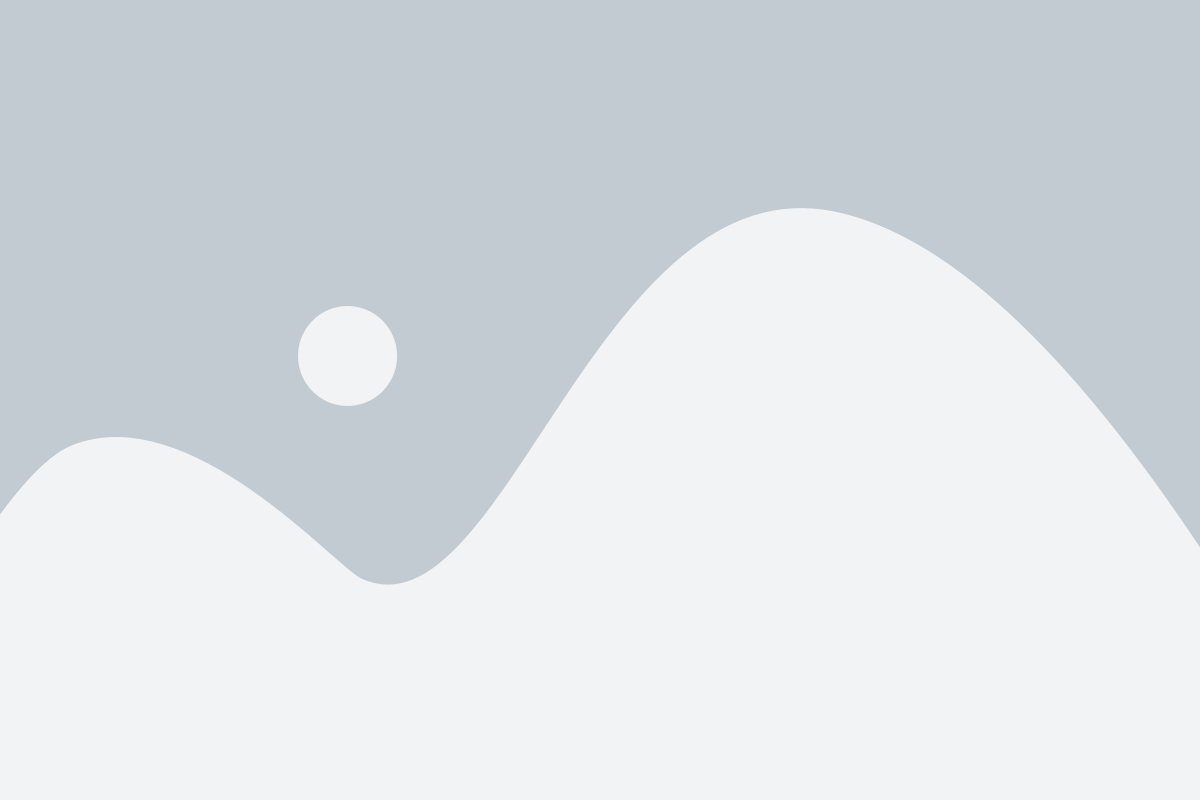
Design Throat Thickness of Partial Penetration Butt Weld
For partial penetration butt welds, the design throat thickness refers to the calculated theoretical thickness of the weld at its root, similar to full penetration welds. However, in the case of partial penetration welds, the throat thickness is less than that of full penetration welds, as the weld does not fully penetrate the thickness of the joint.
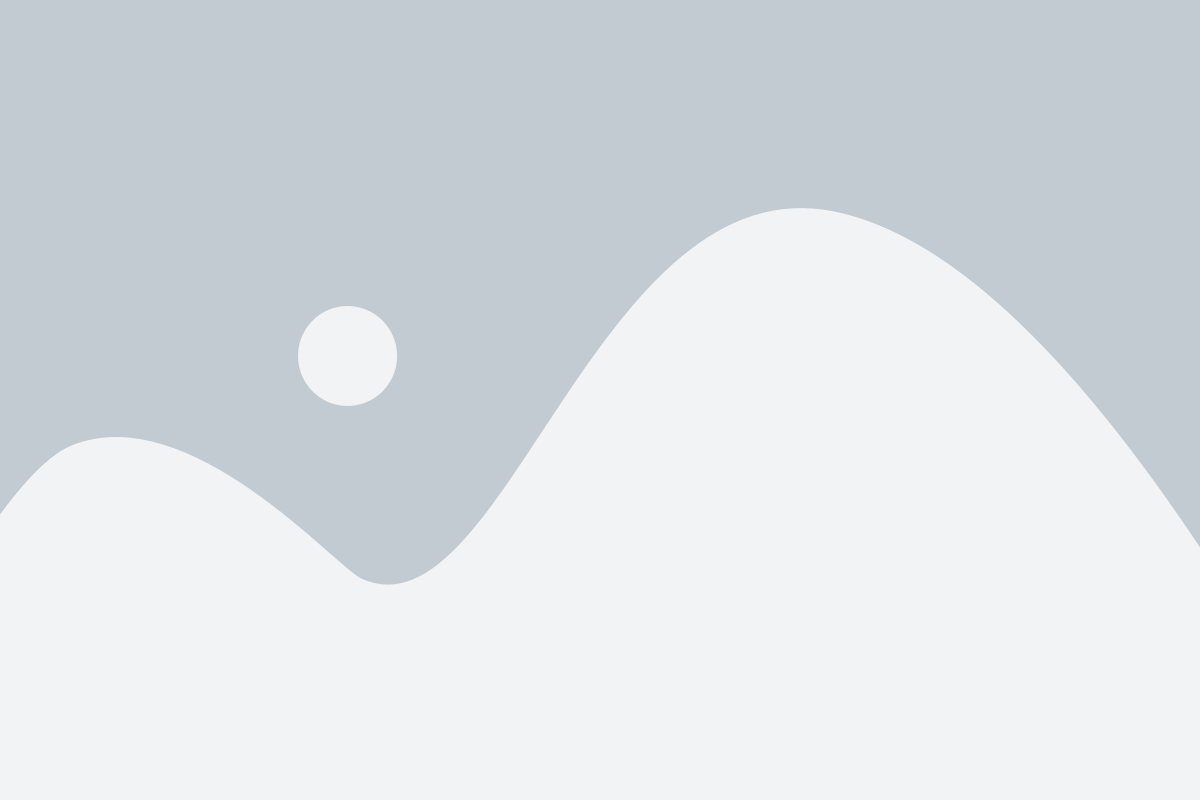
Actual Throat Thickness of Partial Penetration Butt Weld
The actual throat thickness of a partial penetration butt weld is the measured thickness of the weld at its root after welding. It is typically less than the design throat thickness due to the incomplete penetration of the weld into the joint material.
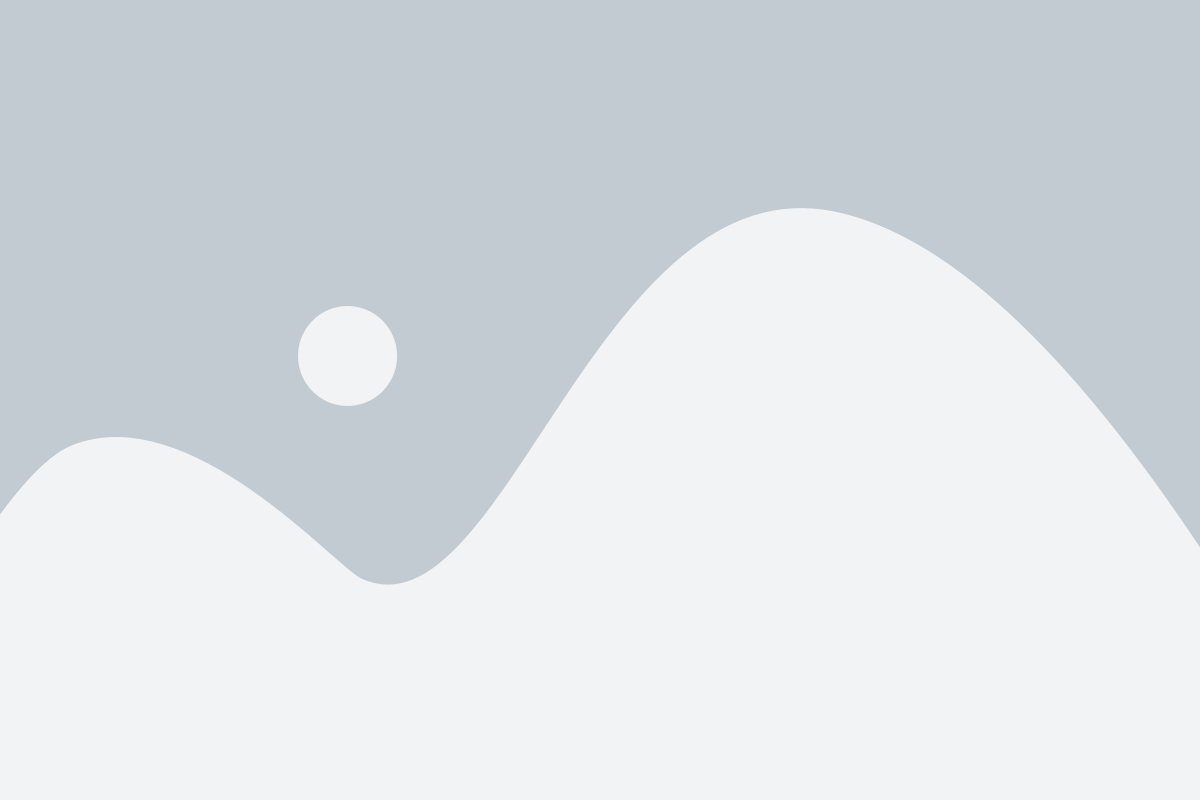
Leg Length of Fillet Weld
The leg length of a fillet weld is the distance from the root of the fillet weld to the toe of the weld, measured along the perpendicular line from the intersection of the two surfaces being joined. It is an essential dimension used to specify the size of fillet welds and is measured on both sides of the joint.
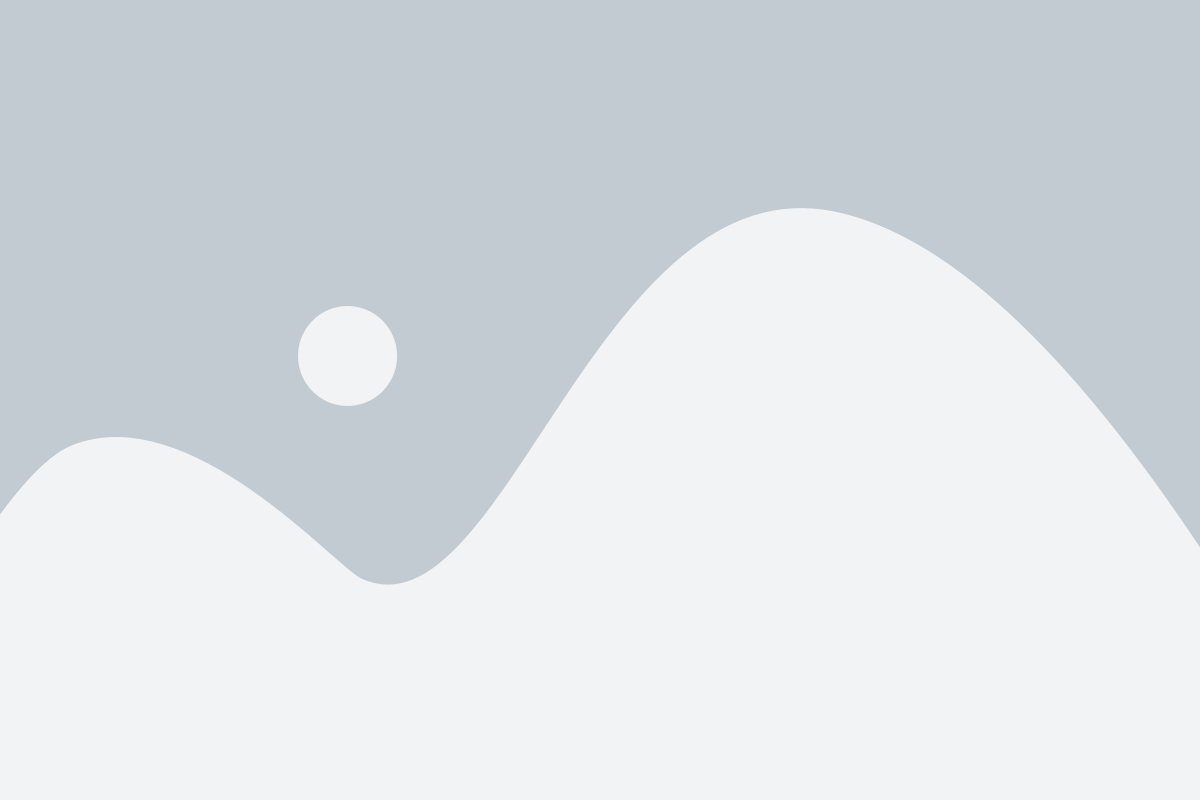
Design Throat Thickness of Fillet Weld
The design throat thickness of a fillet weld is the theoretical thickness of the weld at its root. It is calculated based on the size of the weld leg and is used for design and analysis purposes.
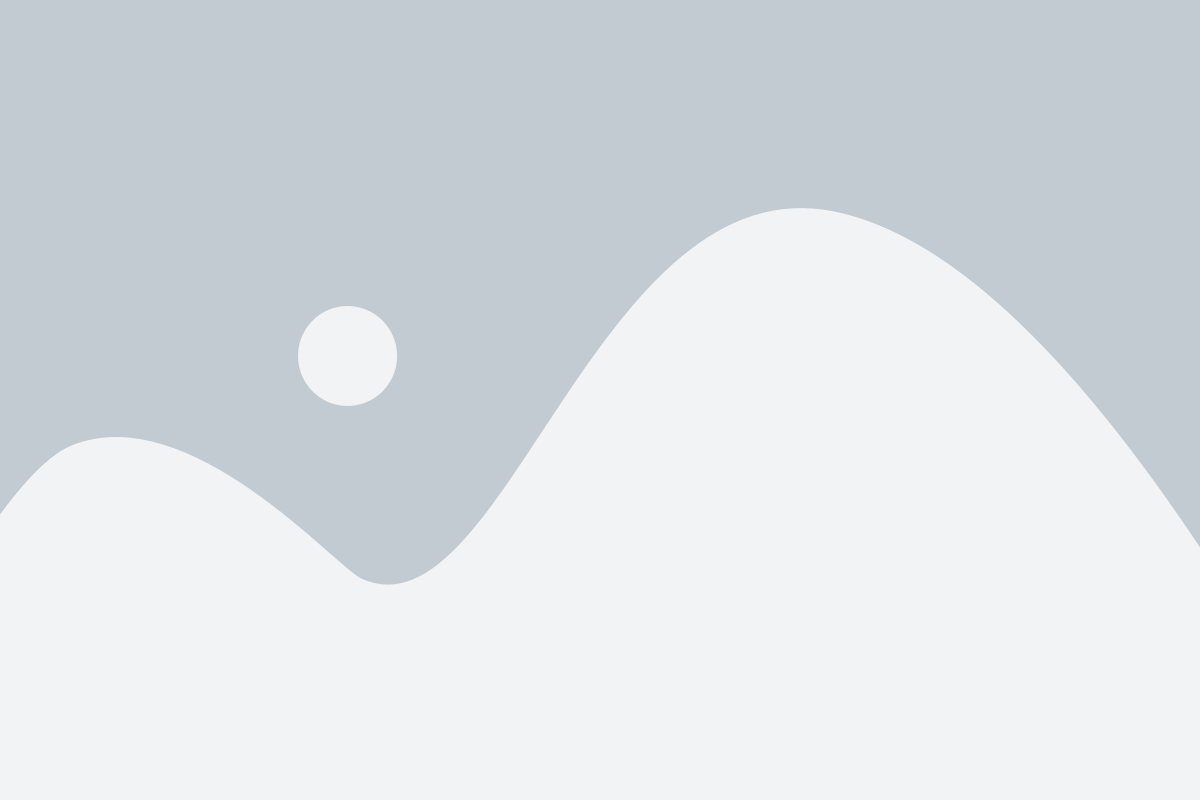
Actual Throat Thickness of Fillet Weld
The actual throat thickness of a fillet weld is the measured thickness of the weld at its root after welding has been completed. This measurement is typically performed using calibrated instruments or weld gauges and may differ from the design throat thickness due to factors such as welding process variations and material properties.
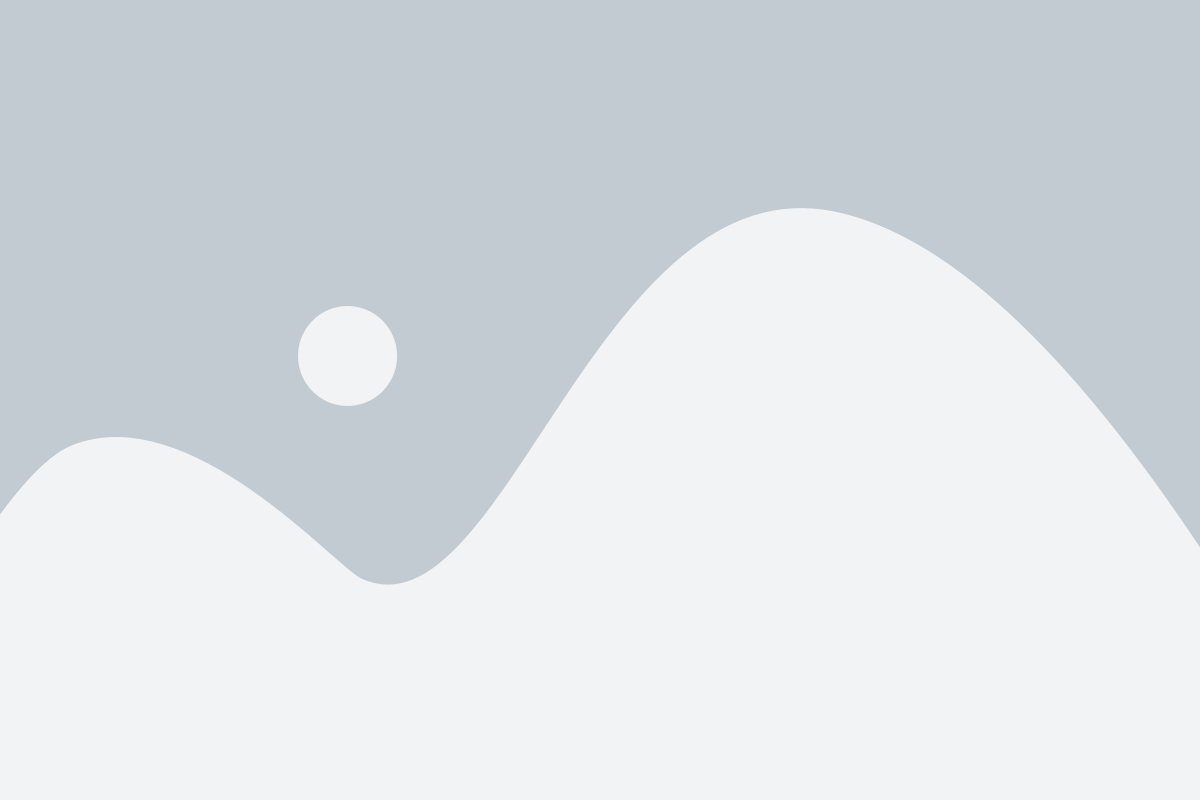
Relation between Leg Length & Design Throat Thickness
For a flat face fillet weld in which the leg lengths are equal within the agreed tolerance, the cross-section area of this type of weld can be considered to be a right angle isosceles triangle with design throat thickness and leg length. The relation between design throat thickness and leg length is Throat = 0.707 x Leg or Leg = 1.414 x Throat