Introduction to Lack of Fusion
Importance of Proper Weld Pool
Lack of fusion, also called as incomplete fusion, is a critical welding imperfection where there is insufficient bonding between weld metal and parent metal or between successive weld layers. It is a type of weld discontinuity in which fusion did not occur between the weld metal and the fusion faces or the adjoining weld beads. This flaw can weaken the weld, leading to structural integrity issues. Lack of sidewall, inter-run, and root fusion are common variations, each demanding specific preventive measures.
Understanding and addressing lack of fusion is essential for ensuring robust weld quality and structural integrity in various industries.
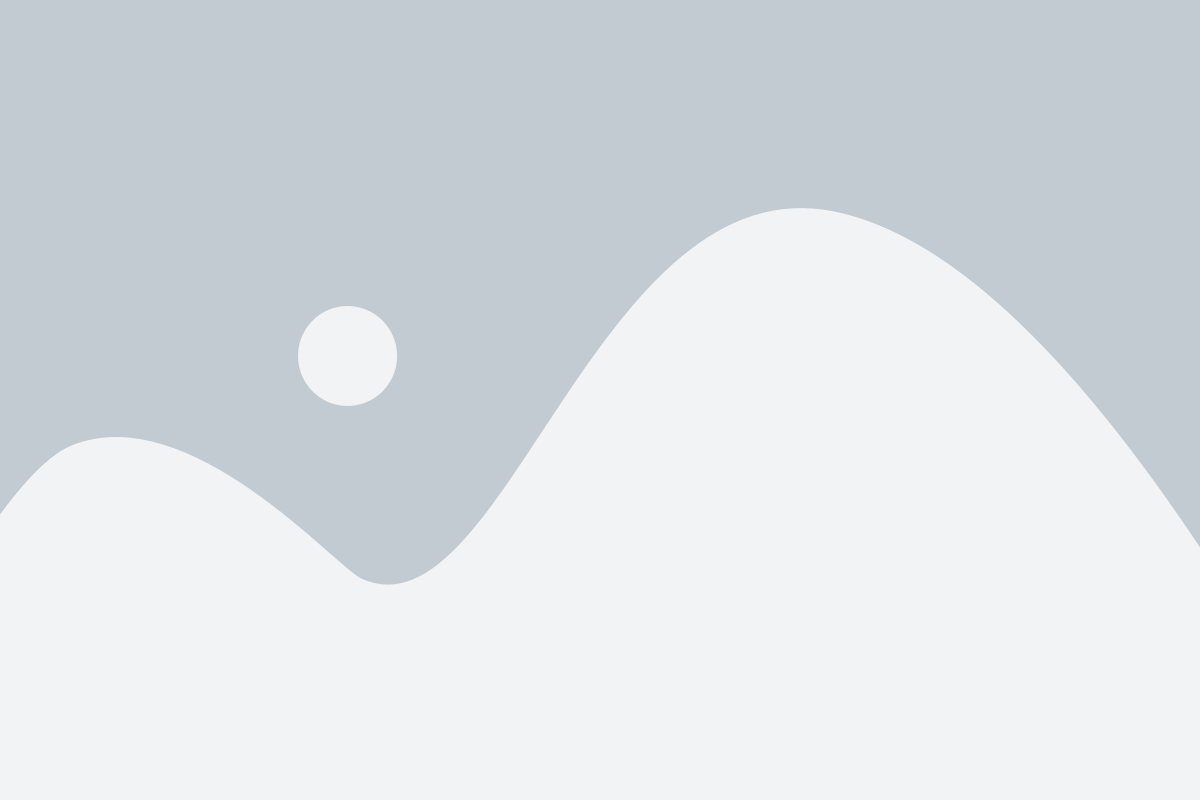
Types of Lack of Fusion
Critical Welding Imperfection
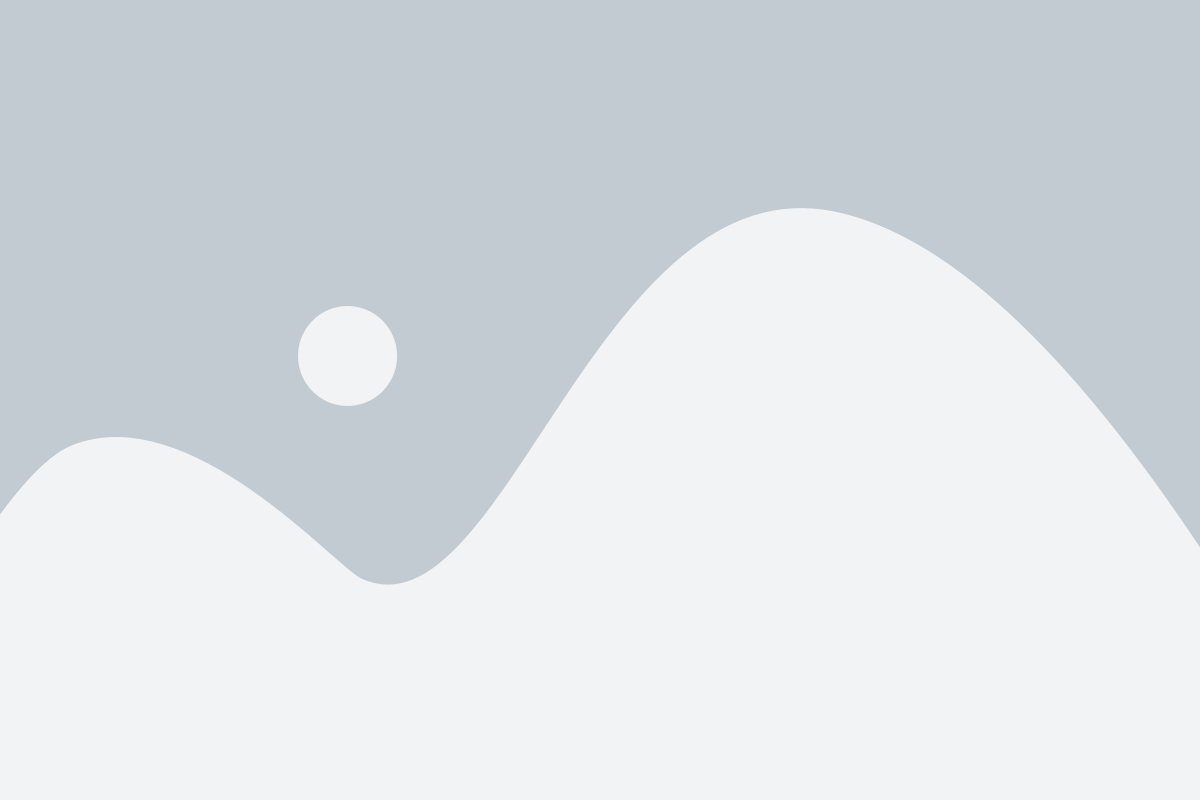
1) Lack of Root Fusion
Lack of root fusion refers to a welding imperfection when the weld metal fails to adequately bond with the parent metal at the root of a welded joint. In essence, this imperfection signifies that the weld has not effectively merged with the base material it is meant to join.
In practical terms, during the welding process, the molten weld metal should flow and fuse seamlessly with the adjacent base material, forming a solid and continuous bond. However, when lack of root fusion occurs, this fusion fails to occur adequately, resulting in a visible gap or void at the root of the weld joint.
Key Factors (Causes) affecting Lack of Root Fusion
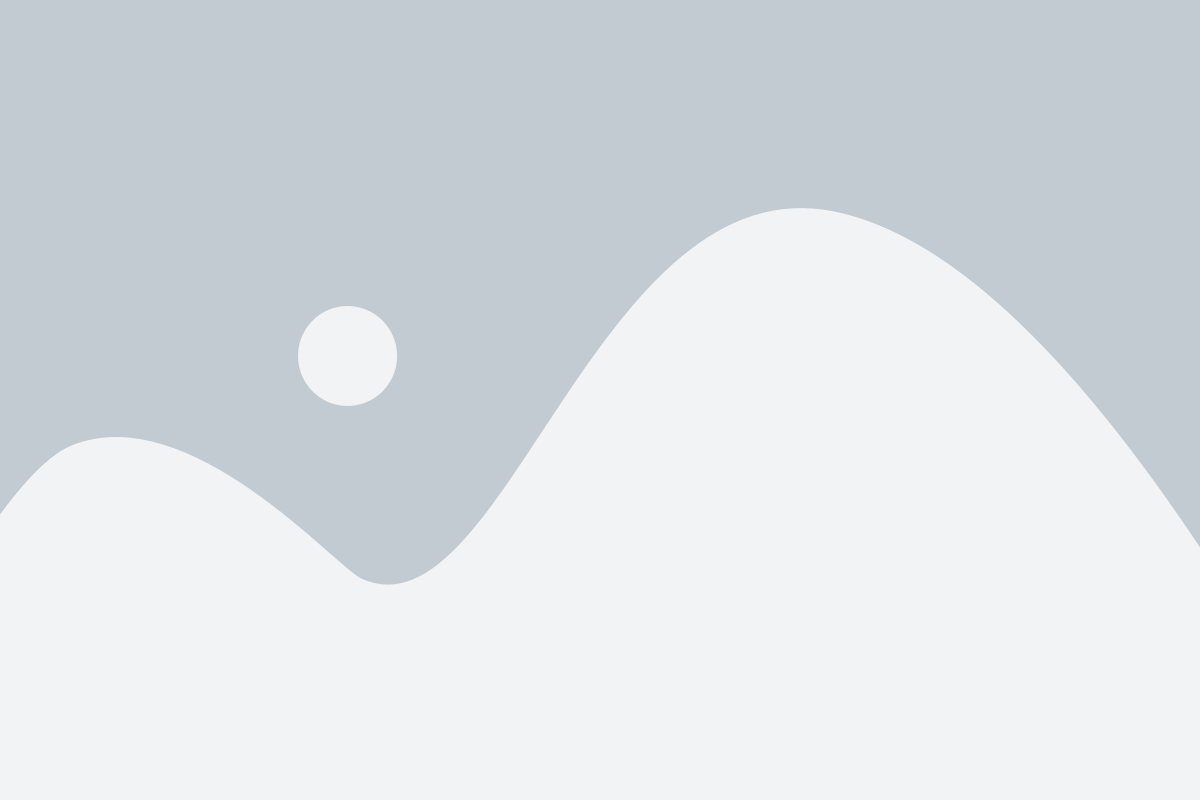
Insufficient Heat Input
Welding processes require sufficient heat to melt both the base metal and the filler material, facilitating fusion. When heat input is inadequate, the temperature at the root of the weld joint may not reach the required level for proper fusion. Factors contributing to low heat input include incorrect welding parameters such as low welding current, voltage, or travel speed.
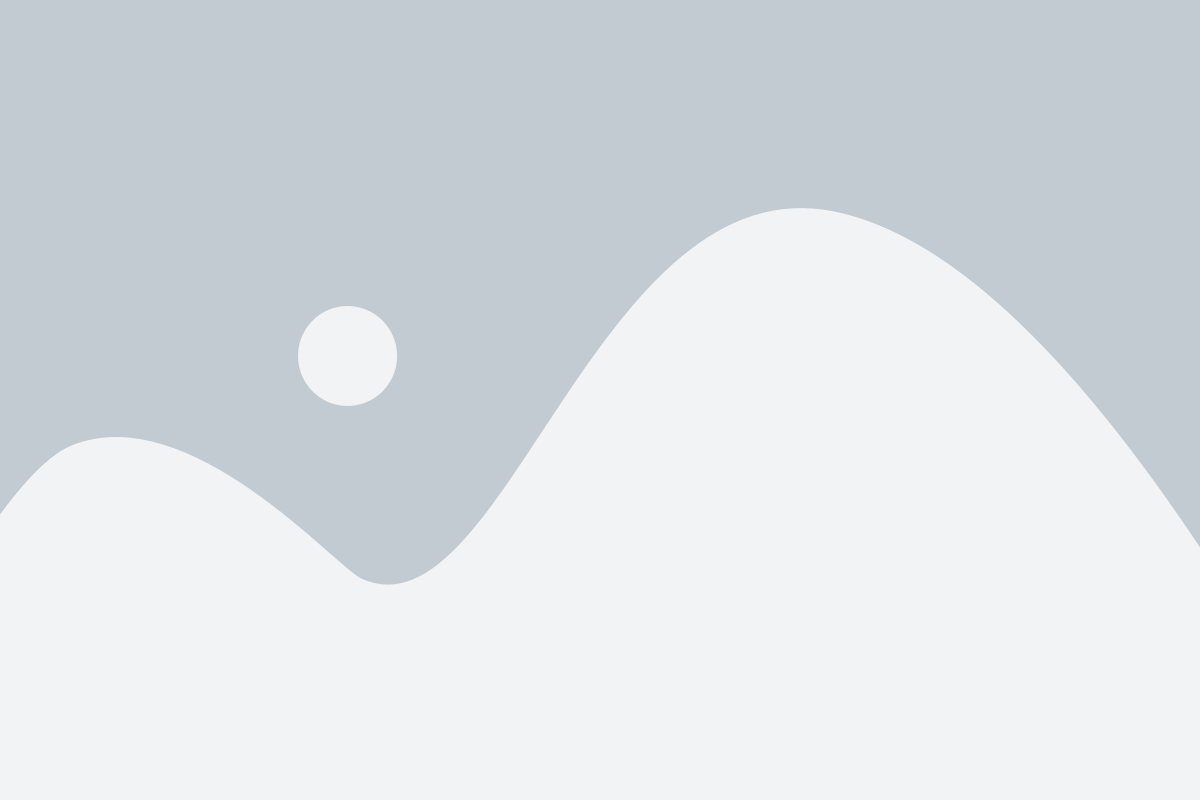
Excessive Inductance
Inductance settings influence the dynamics of the welding arc and the stability of the weld pool. In Gas Metal Arc Welding (GMAW) dip transfer, for instance, excessive inductance can disrupt the flow of molten metal into the root area, preventing complete fusion.
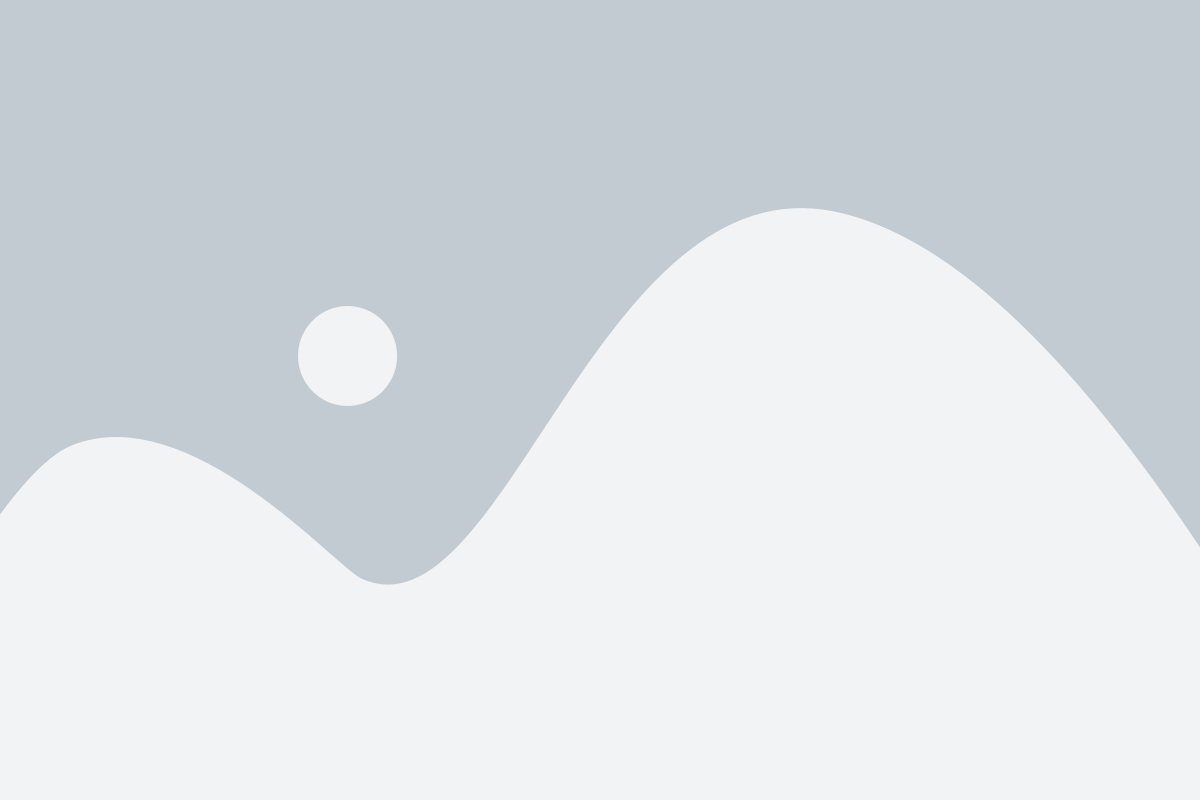
Incorrect Electrode Size & Type
The choice of electrode size and type is crucial for achieving adequate heat input and penetration at the root of the weld. If the electrode is too large, it may deliver excessive heat, leading to burn-through or distortion without promoting proper fusion. Conversely, using an electrode with insufficient current density may result in insufficient heat generation for root fusion.
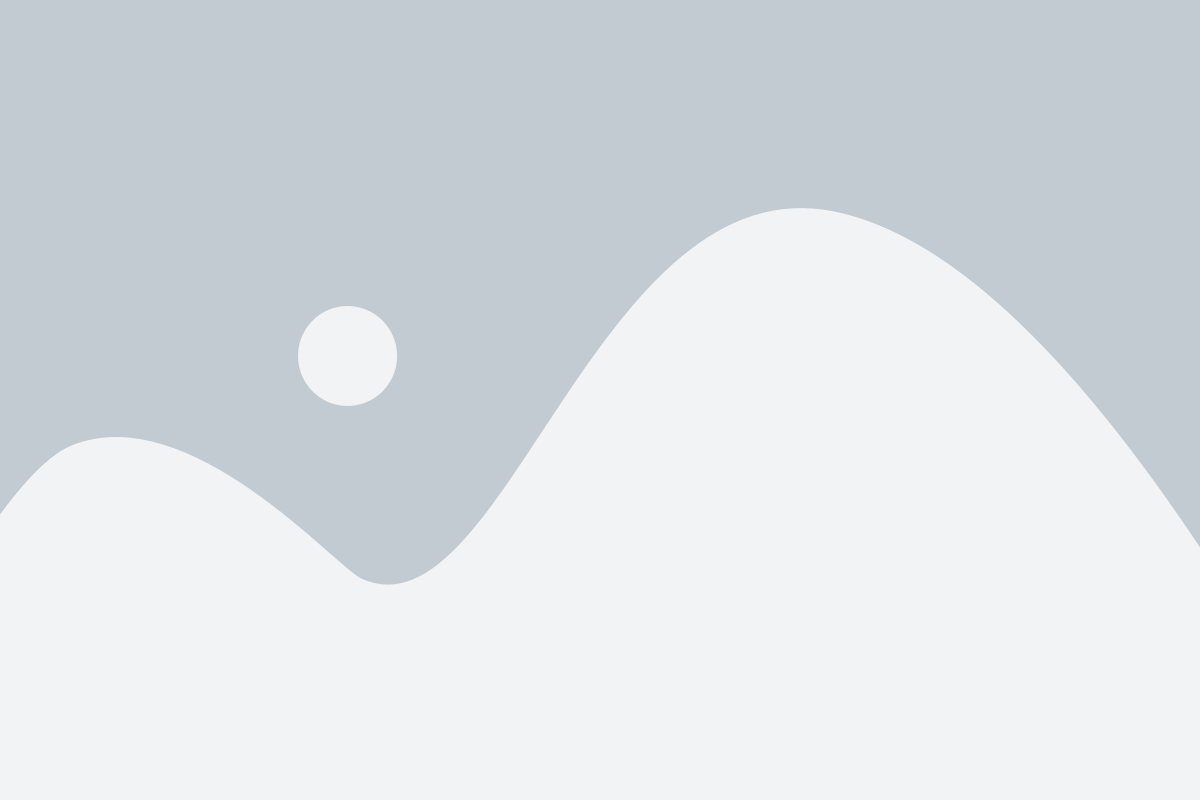
Improper Welding Technique
Welding technique plays a pivotal role in ensuring proper fusion at the root of the weld joint. Incorrect electrode manipulation, such as improper angle or weaving pattern or vertical down welding, can affect the penetration depth and distribution of heat, compromising root fusion. Additionally, inaccurate bead placement may result in inadequate coverage of the root area, impeding fusion.
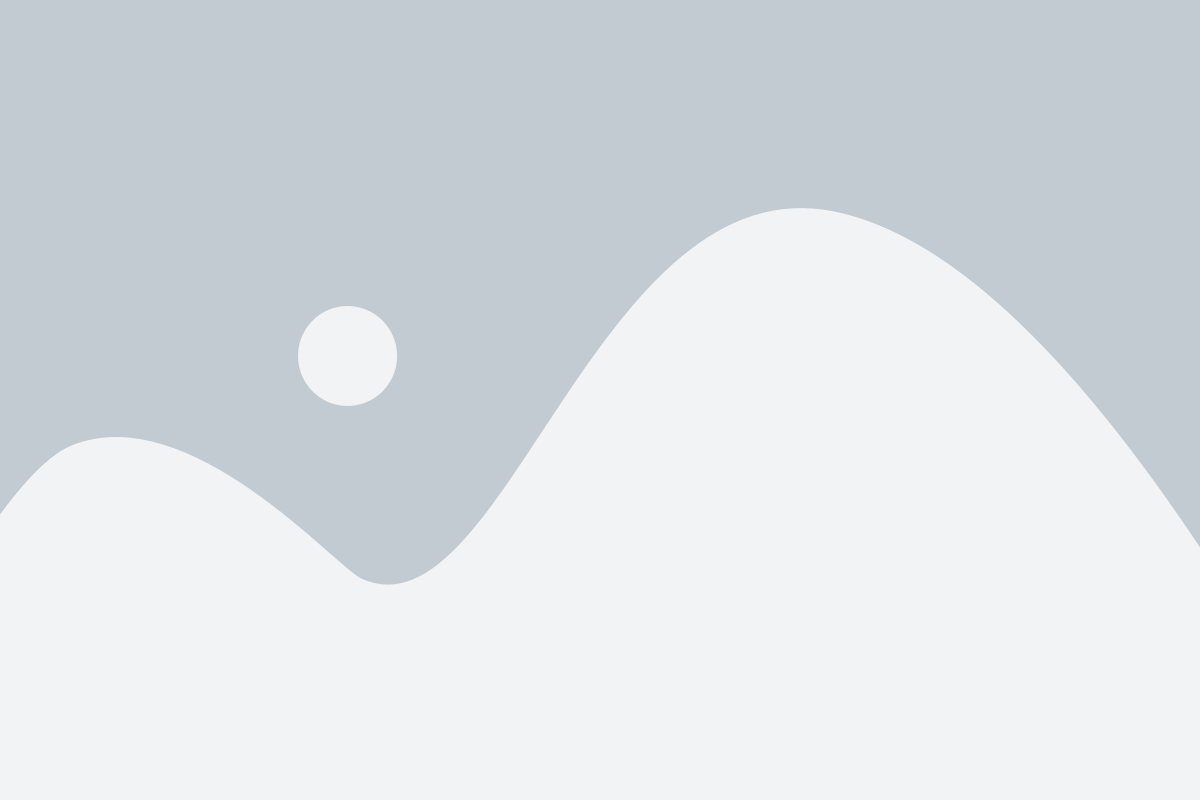
Incorrect Joint Preparation
Joint preparation is critical for facilitating root fusion by providing proper access for the welding arc and ensuring clean, properly aligned surfaces for bonding. Large root face or small root gap can hinder heat transfer to the root, preventing effective fusion.
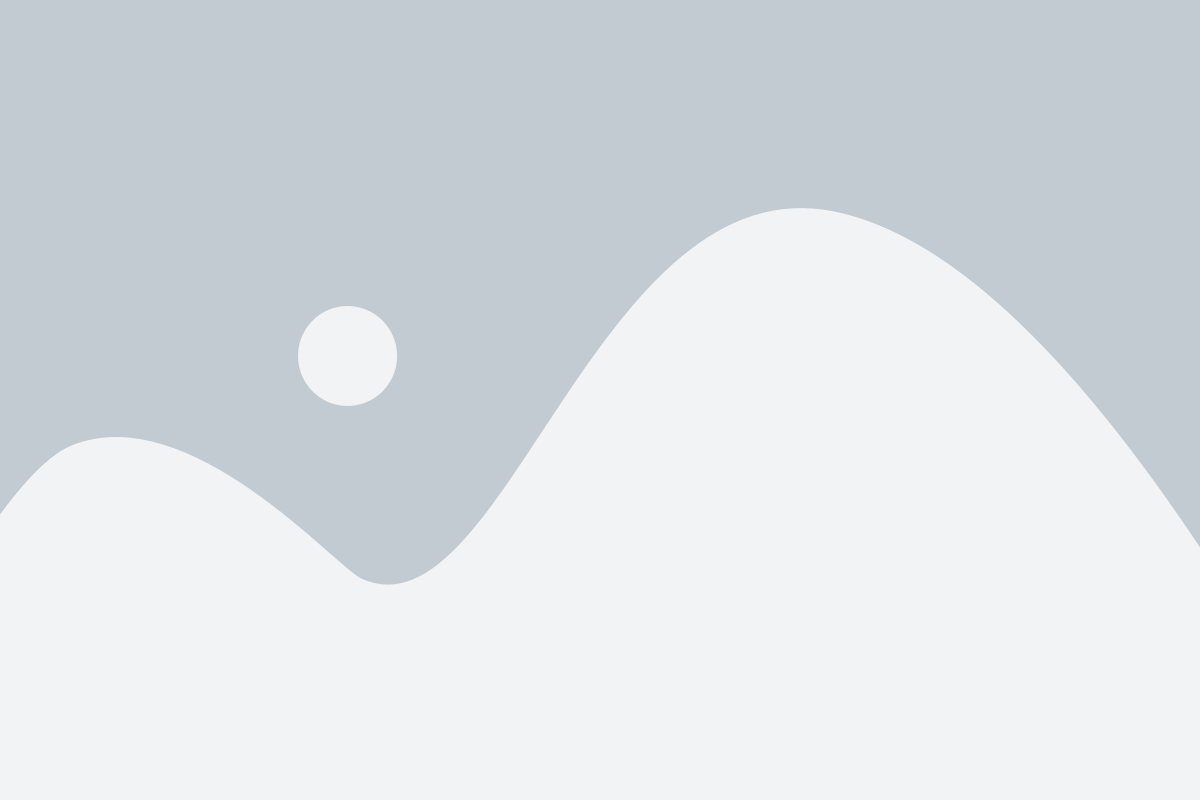
Misalignment at the Root
Misalignment between the base metal edges at the root of the weld joint can create gaps or voids that inhibit fusion. Excessive misalignment prevents intimate contact between the weld metal and base metal, impeding the flow of molten metal and compromising fusion integrity.
Prevention against Lack of Root Fusion
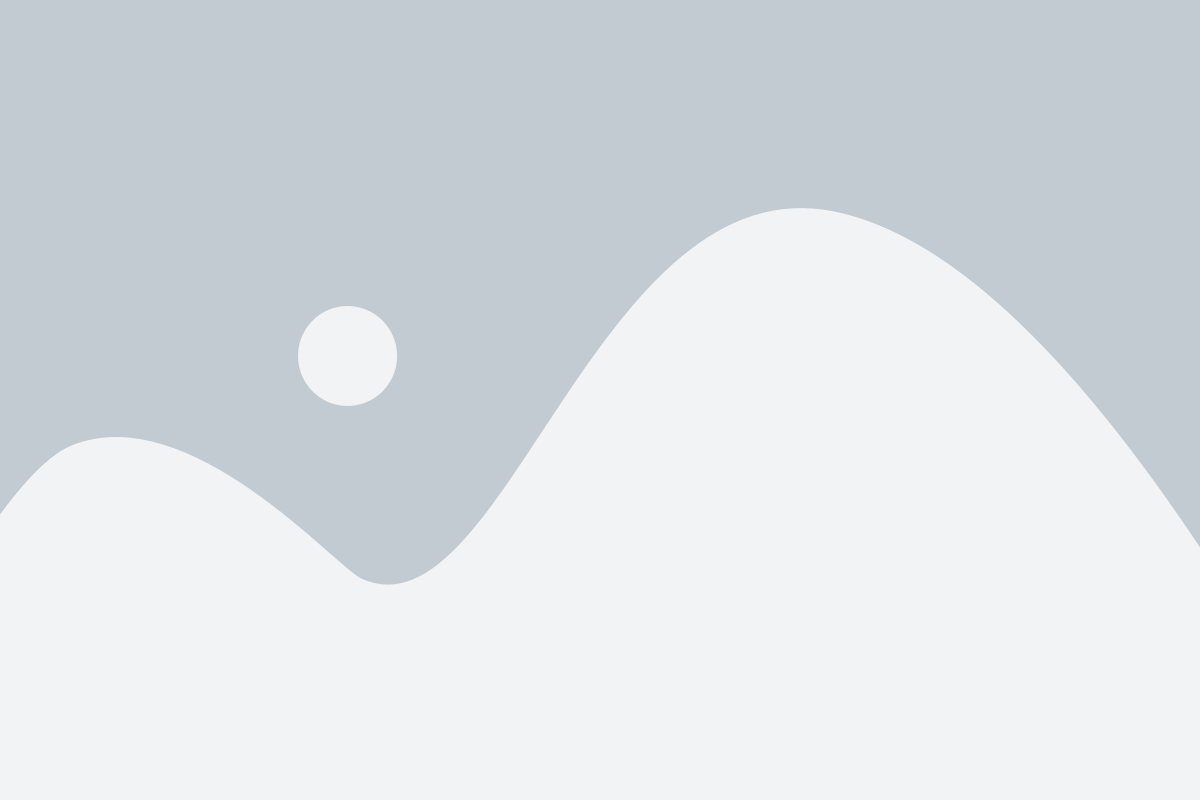
Optimizing Heat Input
Controlling heat input is crucial for achieving proper fusion at the root of the weld joint. Welding parameters such as current, voltage, and travel speed should be adjusted to ensure adequate heat generation. Too little heat can result in insufficient melting of the base metal, leading to lack of fusion, while excessive heat can cause burn-through or distortion without promoting proper bonding.
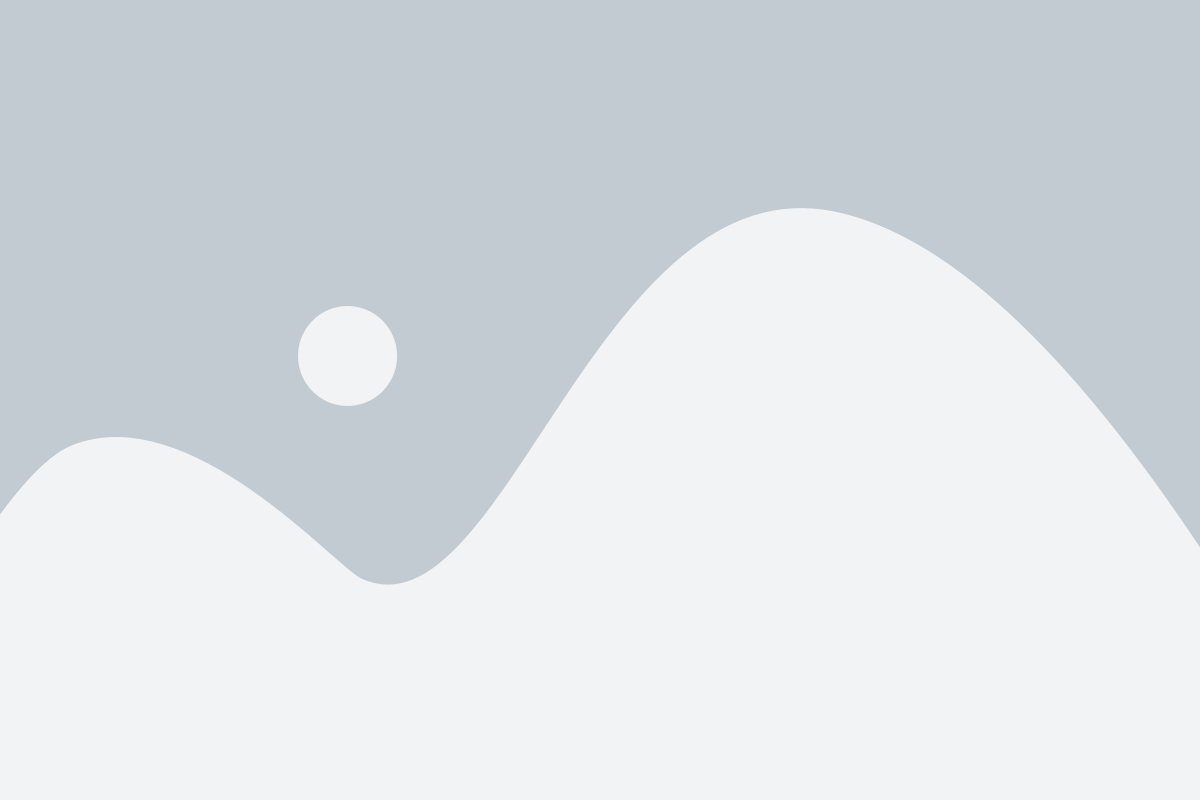
Managing Inductance
In processes like GMAW, inductance settings influence the behavior of the welding arc and the stability of the weld pool. By adjusting inductance levels, welders can control the arc characteristics to optimize molten metal flow into the root area. Proper management of inductance ensures consistent fusion along the entire length of the weld joint.
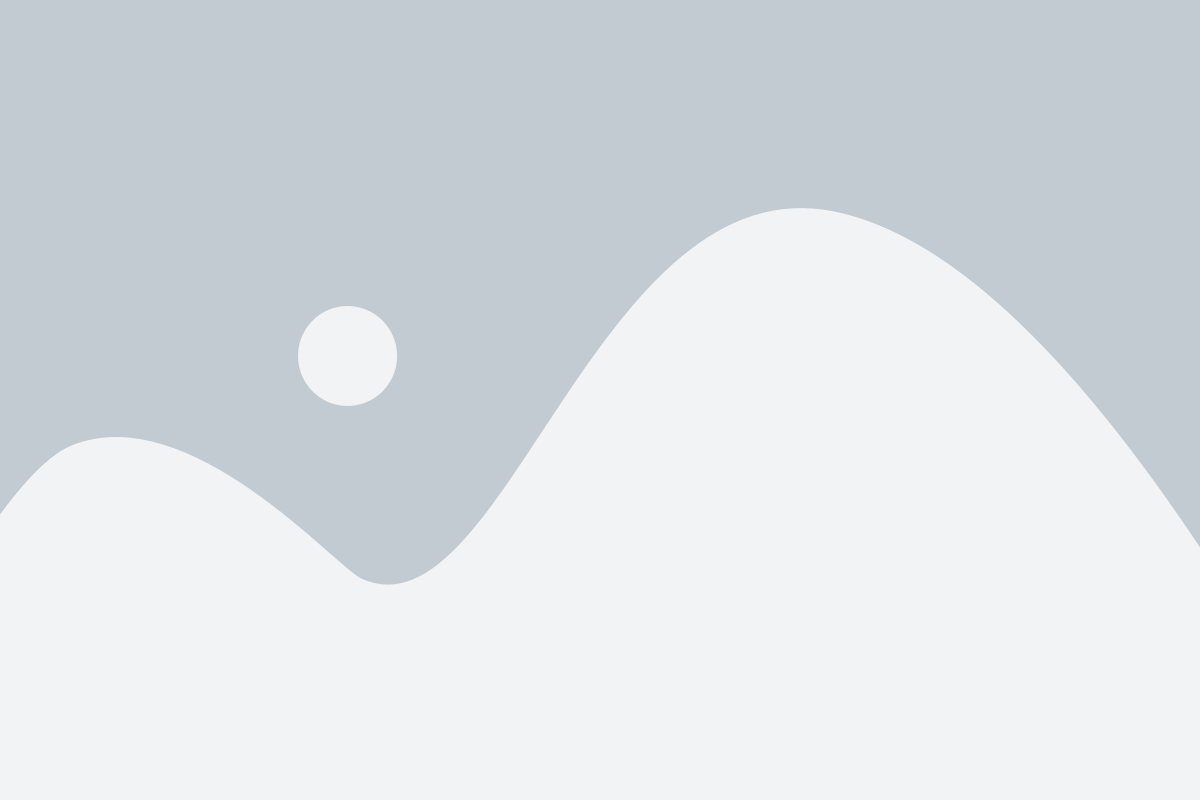
Correct Electrode Selection
Choosing the right electrode size and type is essential for achieving adequate root fusion. Electrodes should match the welding current density requirements and be properly prepared to ensure optimal performance. Correct electrode selection contribute to consistent penetration and bonding at the root of the weld.
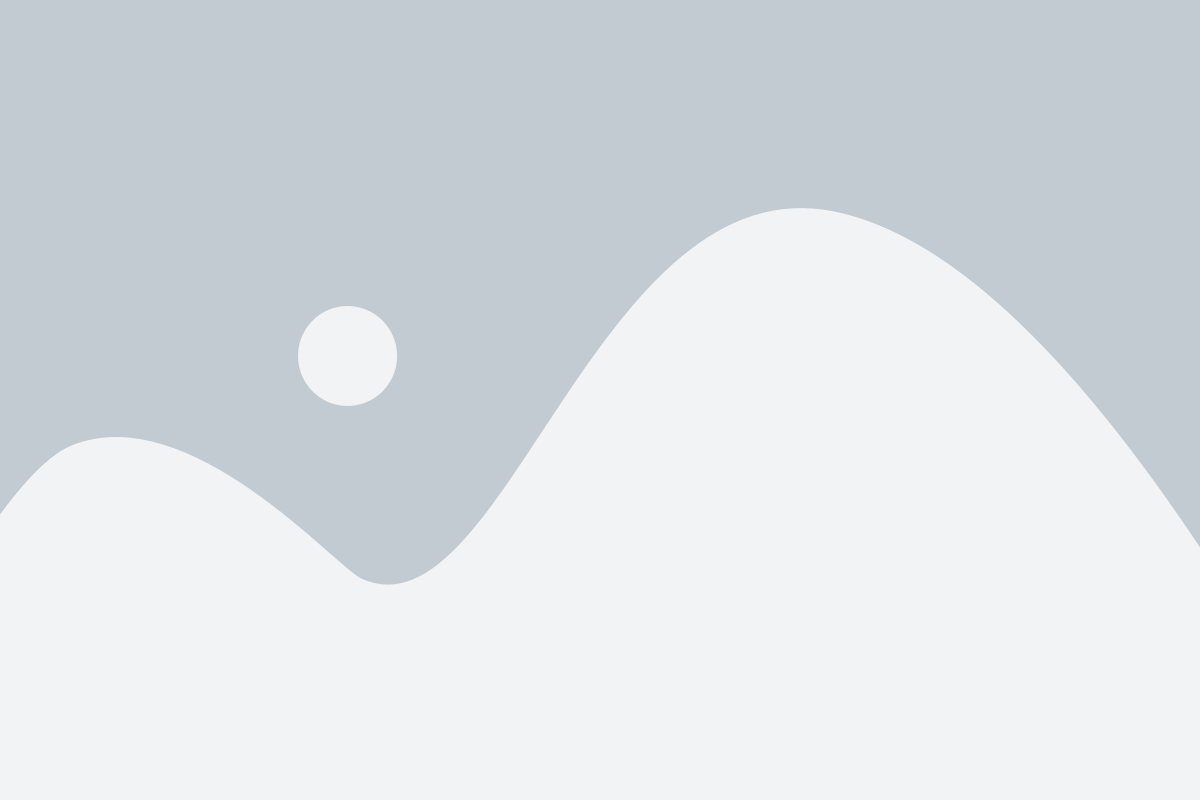
Proper Welding Technique
Proper welding technique is critical for promoting root fusion. Welders should maintain a consistent arc length, angle, and travel speed to ensure uniform heat distribution and penetration. Additionally, proper electrode manipulation, such as proper angle or weaving pattern or vertical up welding, help optimize fusion conditions and minimize the risk of defects.
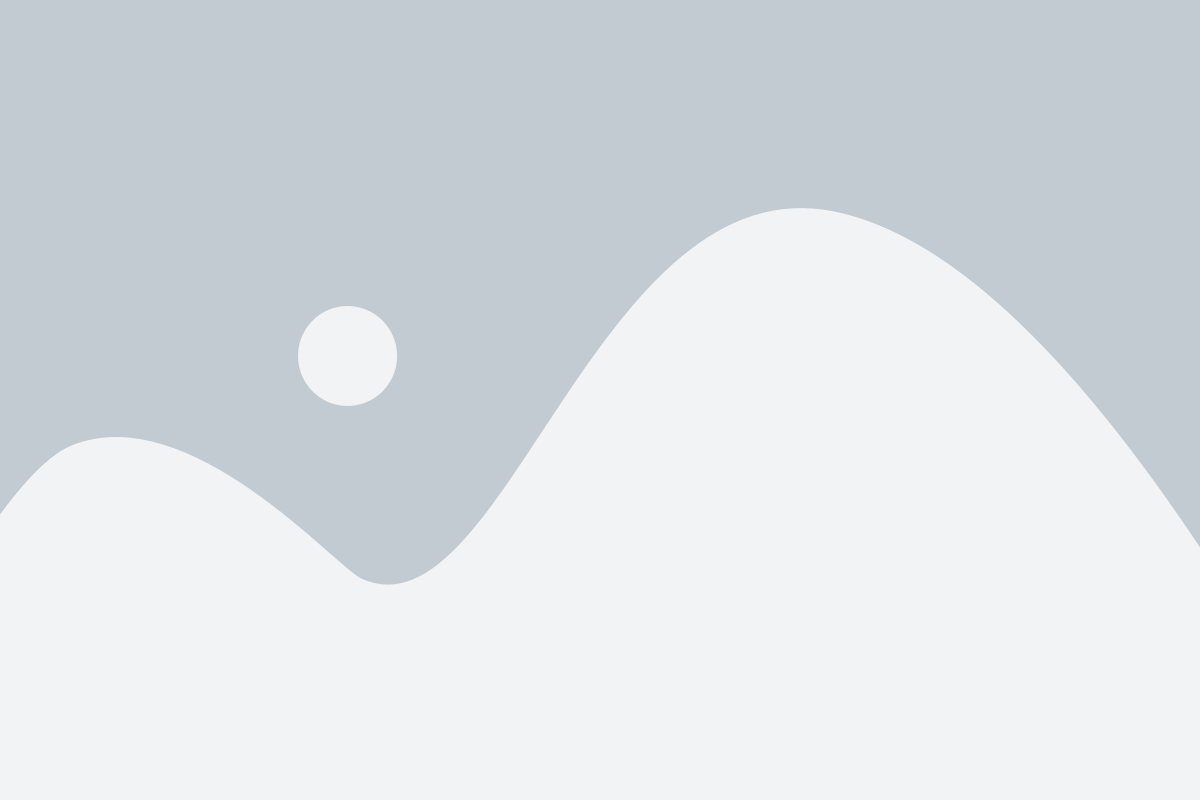
Correct Joint Preparation
Thorough joint preparation is essential for facilitating root fusion. Weld joints should be cleaned thoroughly to remove contaminants such as oil, grease, and rust. Proper alignment of the base metal edges with appropriate root face and gap dimensions ensures optimal access for the welding arc and promotes efficient fusion.
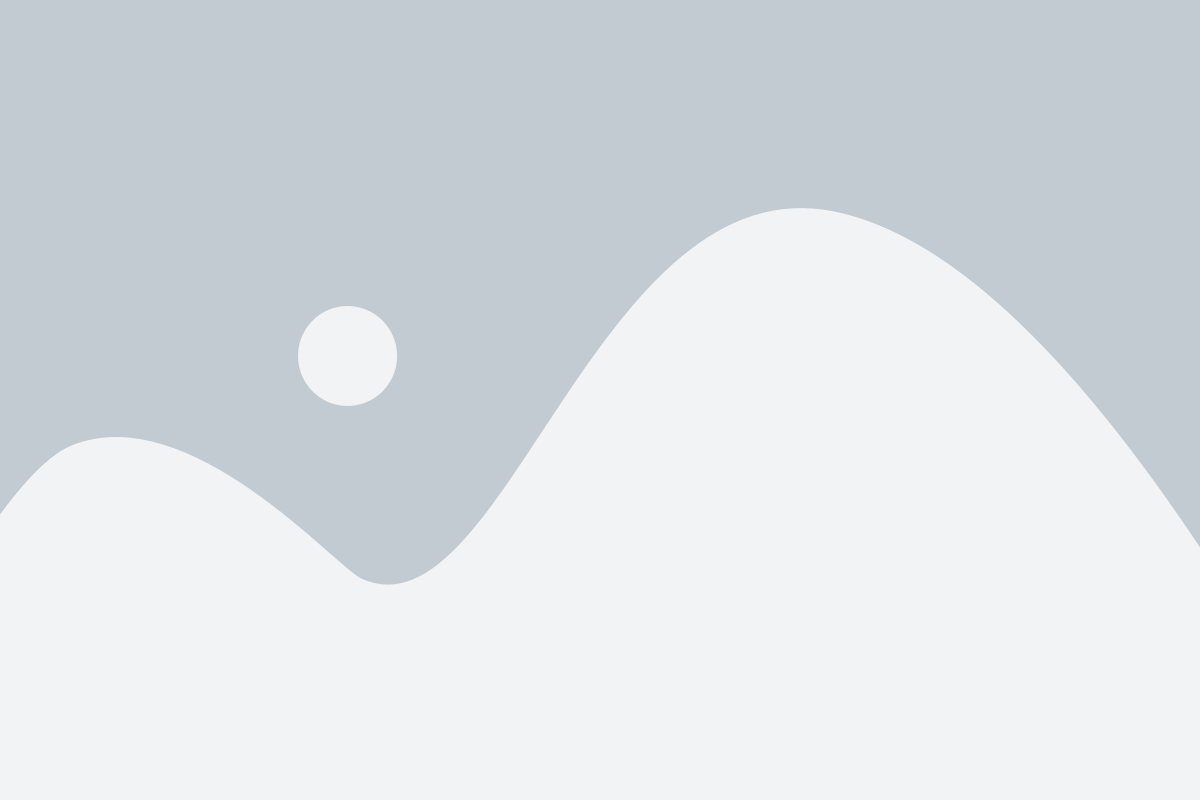
Addressing Root Misalignment
Misalignment between base metal edges can create gaps or voids that hinder root fusion. Welders should take care to minimize misalignment and ensure proper fit-up of the joint. Proper alignment promotes intimate contact between the weld metal and base metal, facilitating the flow of molten metal and promoting fusion integrity.
2) Lack of Inter-run Fusion
Lack of inter-run fusion, also known as inter-pass fusion, is a welding imperfection characterized by the absence of fusion between successive weld passes or layers. In multi-pass welding, where multiple layers of weld metal are deposited to fill a joint, proper fusion between these layers is crucial for ensuring the integrity and strength of the weld.
When lack of inter-run fusion occurs, there is insufficient bonding between the previously deposited weld bead and the subsequent pass. This deficiency can lead to discontinuities, such as cracks or lack of fusion defects, within the weld structure. Without adequate fusion between the weld passes, the overall weld integrity is compromised, making it susceptible to failure under load or stress conditions.
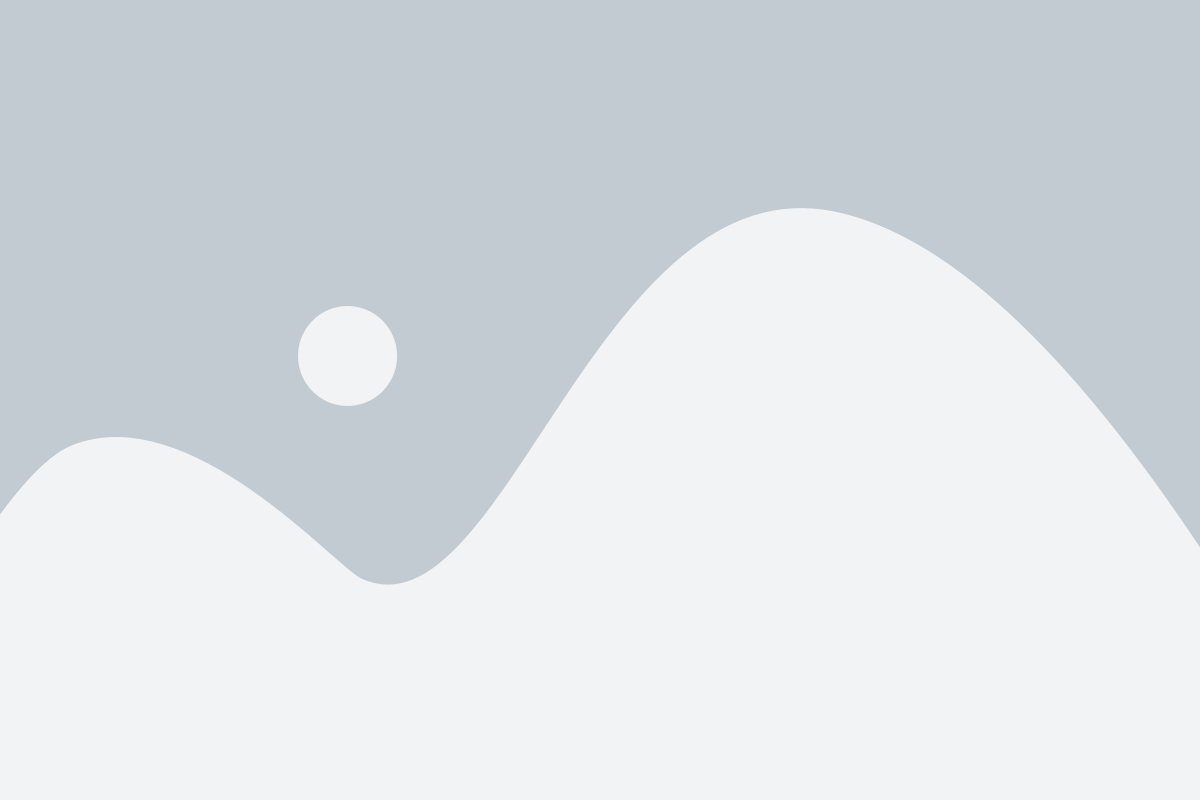
Key Factors (Causes) affecting Lack of Inter-run Fusion
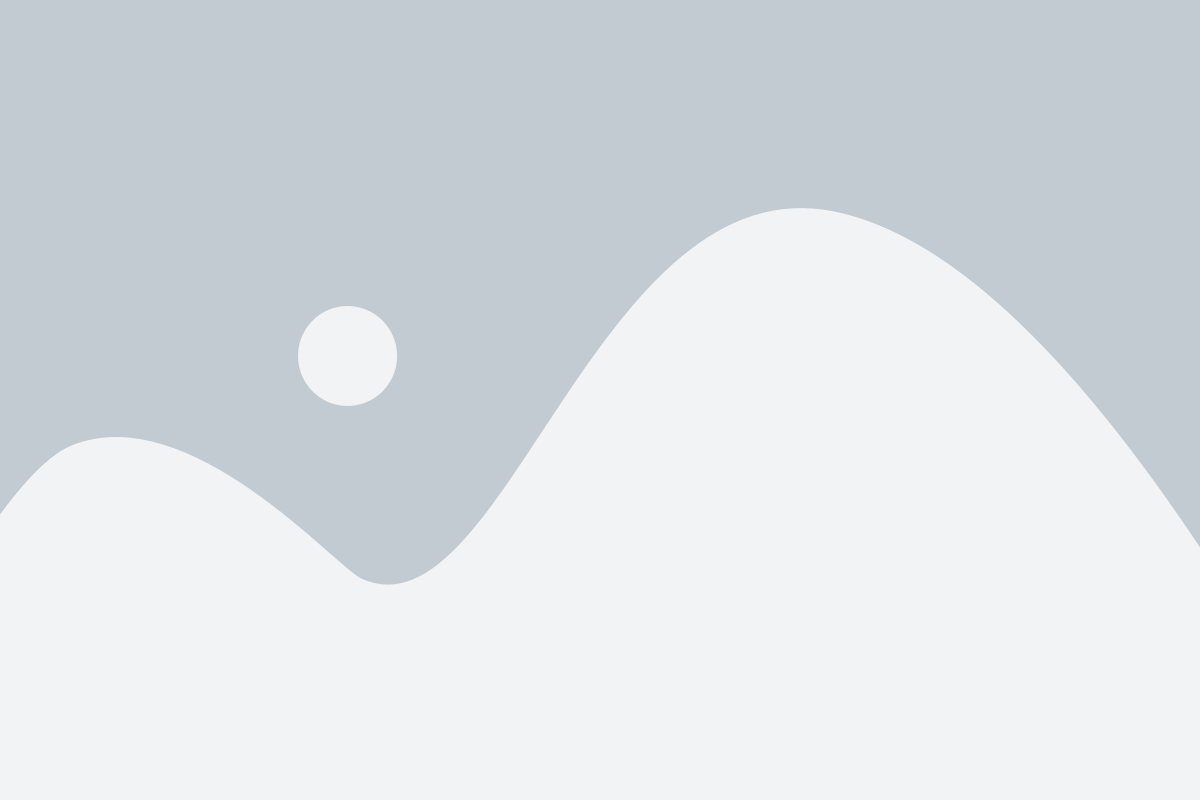
Low Arc Current
Insufficient arc current results in a low level of heat generation, leading to poor fluidity of the weld pool. As a result, the molten metal from the subsequent weld pass may struggle to fuse adequately with the previously deposited layer. This lack of heat input prevents proper bonding between the weld passes, resulting in lack of inter-run fusion.
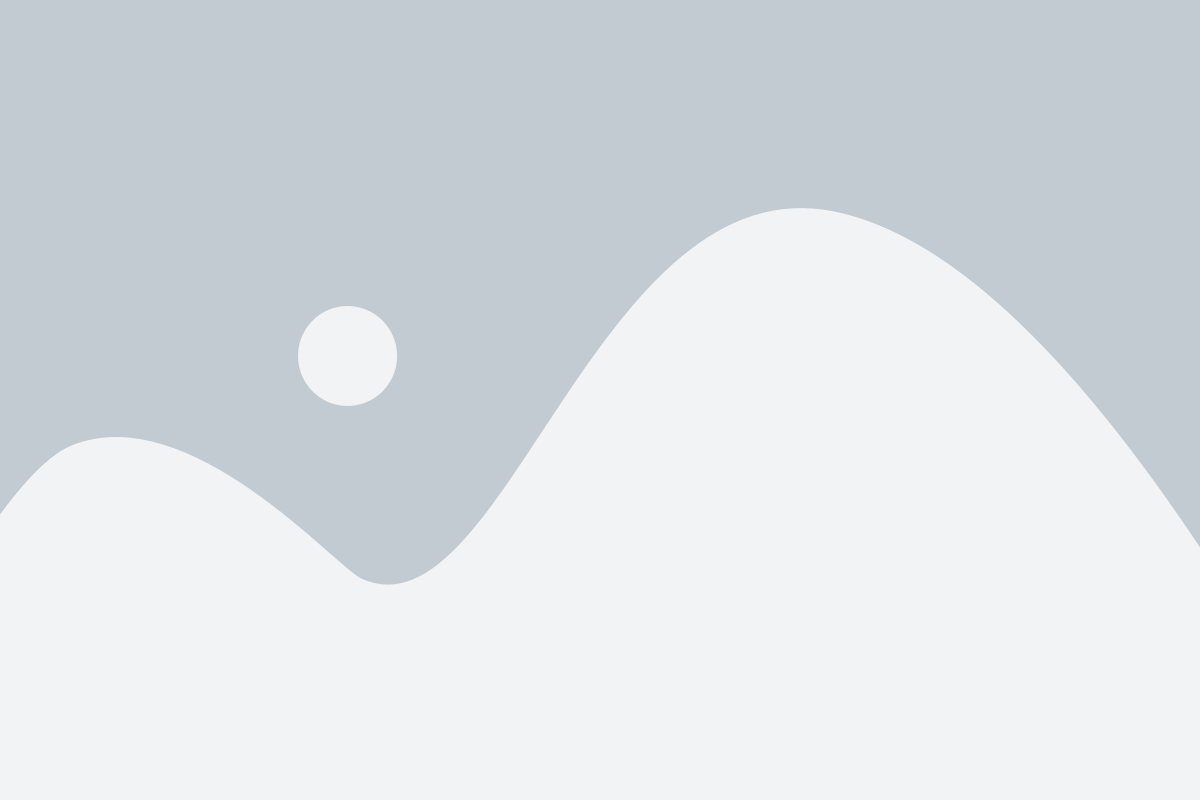
High Travel Speed
Excessive travel speed during welding reduces the amount of time the welding torch or electrode spends in contact with the workpiece. This rapid movement limits the opportunity for proper mixing and bonding of the molten weld metal with the previous layer. As a result, there is insufficient time for the weld passes to merge effectively, leading to incomplete fusion and lack of inter-run fusion defects.
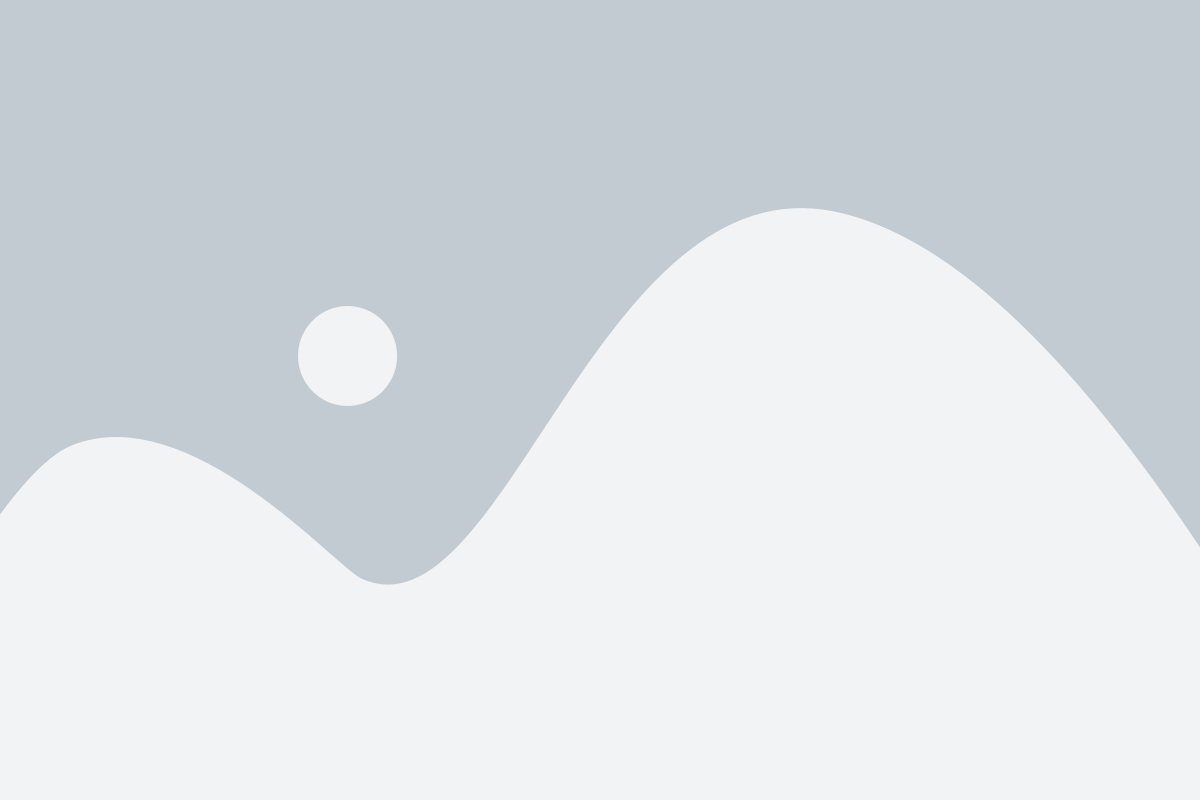
Improper Bead Placement
Incorrect bead placement can hinder inter-run fusion by preventing proper overlap and coverage between successive weld passes. Insufficient overlap or excessive gap between weld passes creates discontinuities within the weld structure, compromising fusion integrity.
Prevention against Lack of Inter-run Fusion
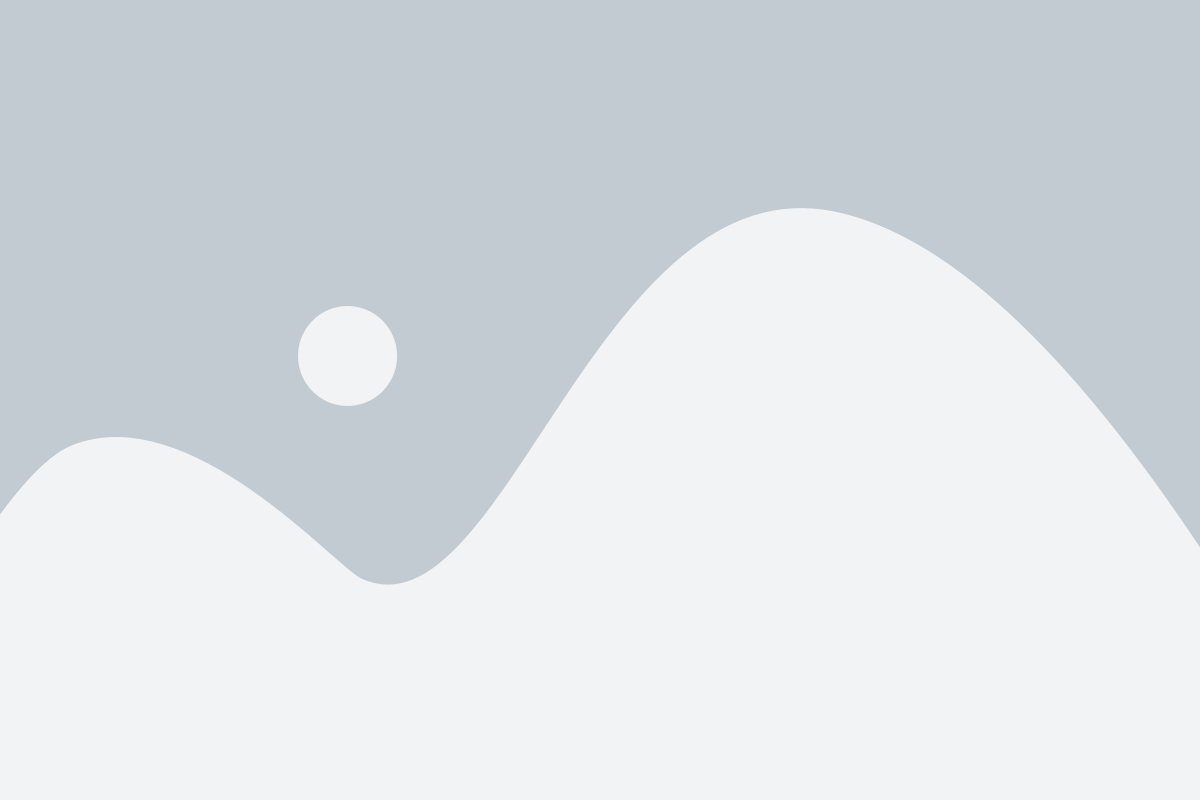
Optimizing Welding Current
Adjusting welding parameters such as increasing arc current is crucial for ensuring proper fusion between successive weld passes. By increasing the welding current, welders can increase the heat input thereby increasing fluidity of the weld pool, facilitating effective bonding between the weld passes.
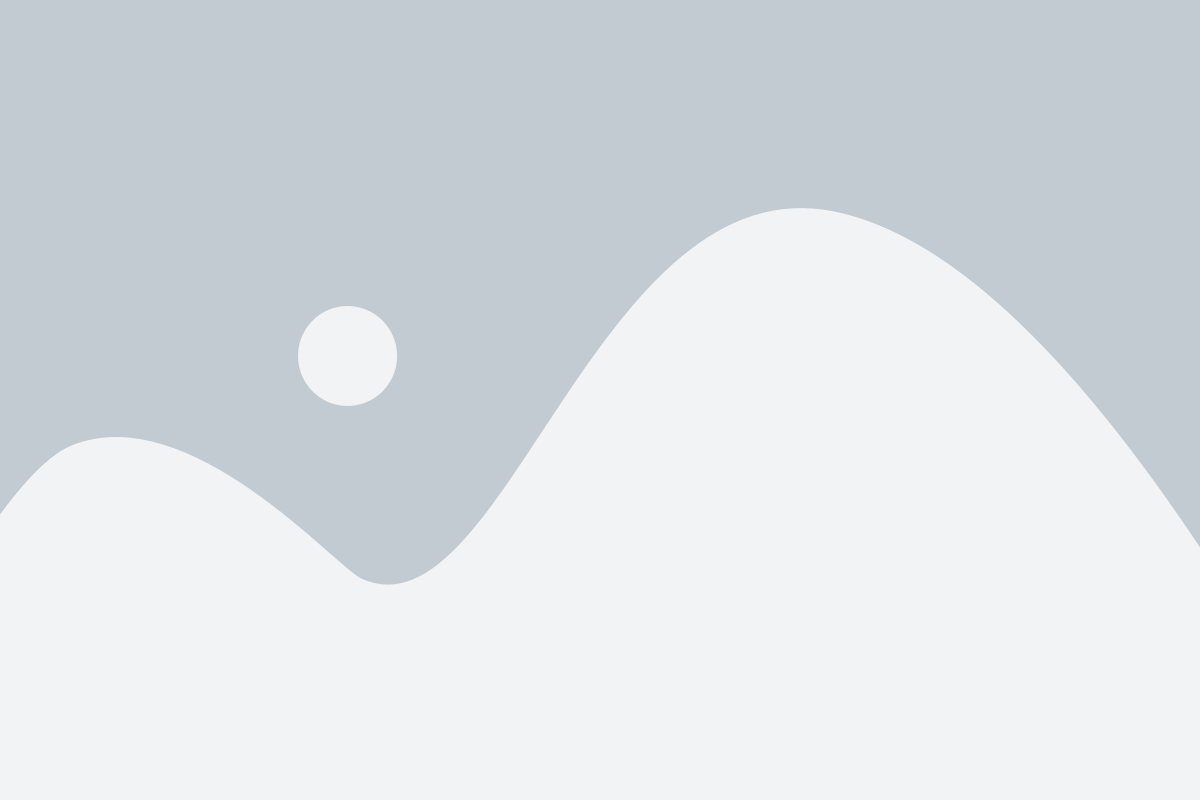
Controlling Travel Speed
Maintaining an appropriate travel speed is essential to allow sufficient time for the molten weld metal to fuse with the previous layer. Welders should adjust the travel speed based on the welding process, material thickness, and joint configuration to optimize fusion conditions.
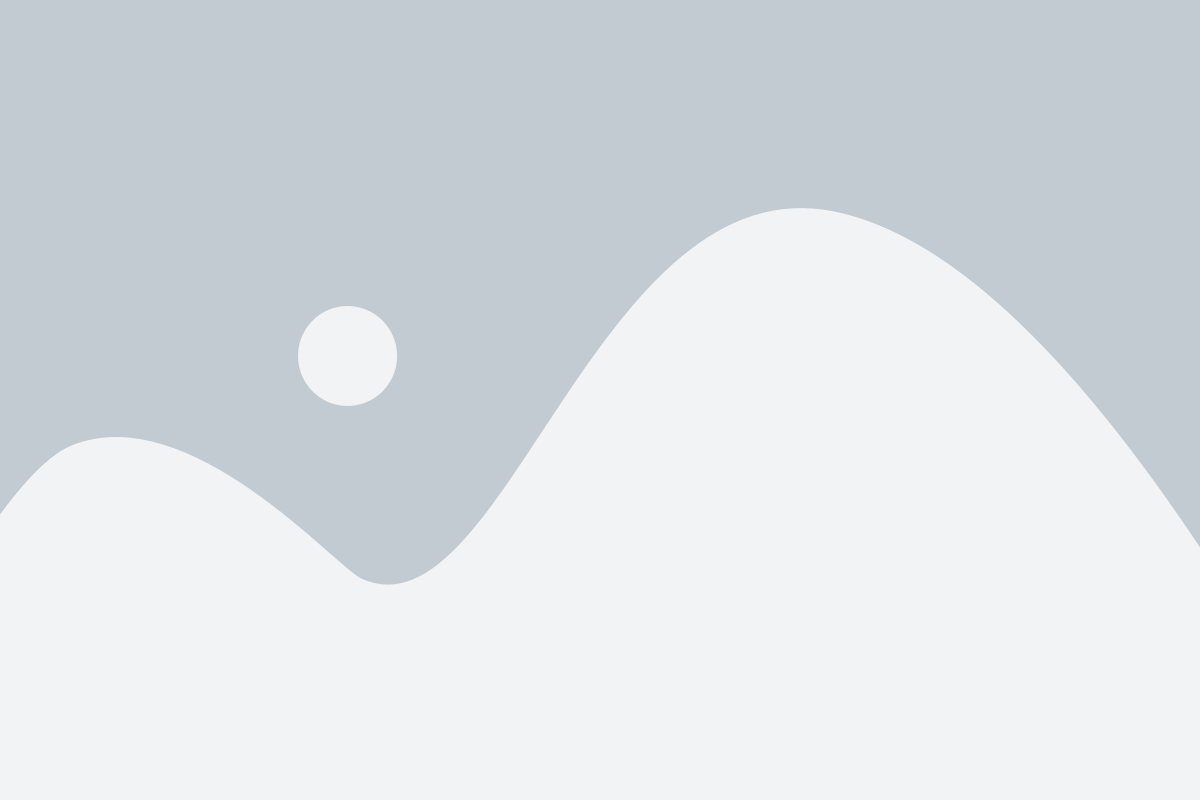
Proper Bead Placement
Proper bead placement and overlap between successive weld passes are critical for promoting inter-run fusion. Welders should ensure consistent bead placement techniques, such as maintaining the correct weaving pattern and ensuring full coverage of the previous weld pass. This ensures that the molten metal from the subsequent pass adequately bonds with the previous layer.
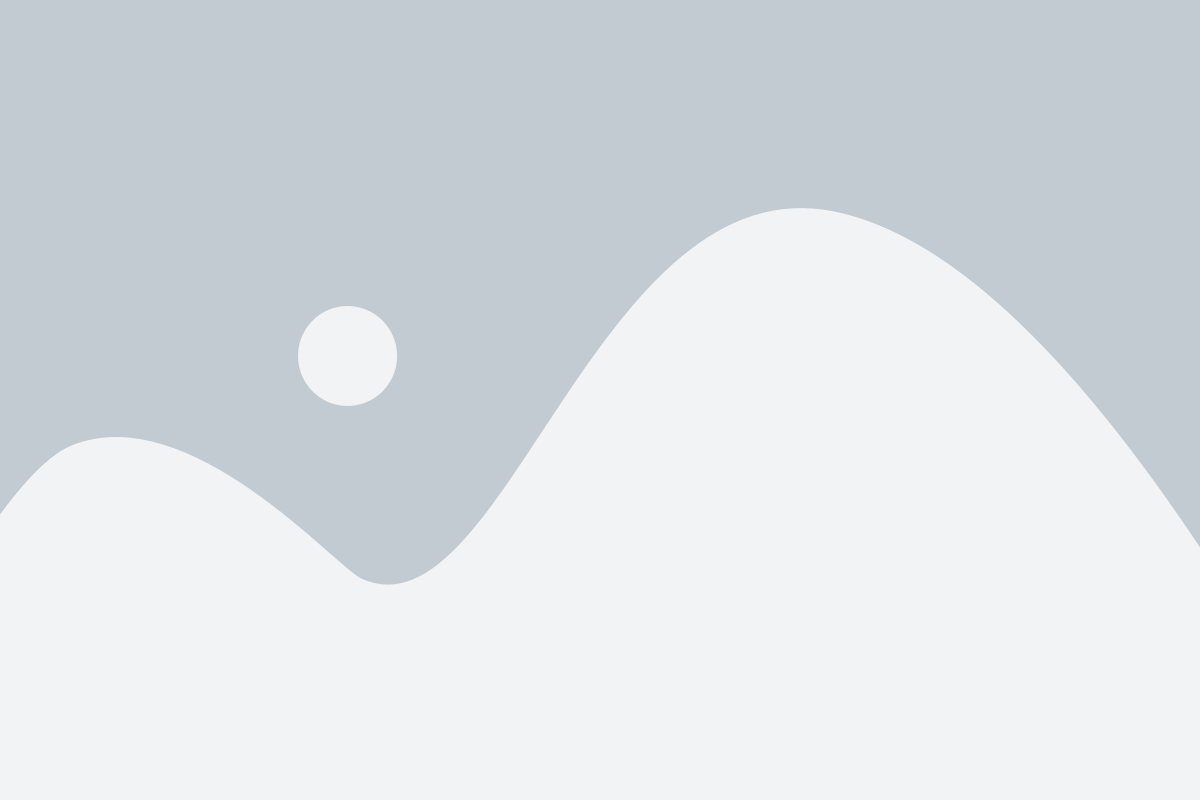
3) Lack of Sidewall Fusion
Lack of sidewall fusion is a welding imperfection characterized by the absence of fusion between the weld and the adjacent base metal at one or both sides of the weld joint. In essence, it signifies a failure to achieve proper bonding between the molten weld metal and the base metal along the sidewalls of the joint.
This imperfection typically manifests as a visible gap or void between the weld and the base metal, indicating incomplete fusion. Without adequate sidewall fusion, the weld joint lacks the necessary strength and integrity to withstand mechanical stresses, making it susceptible to failure under load or stress conditions.
Key Factors (Causes) affecting Lack of Sidewall Fusion
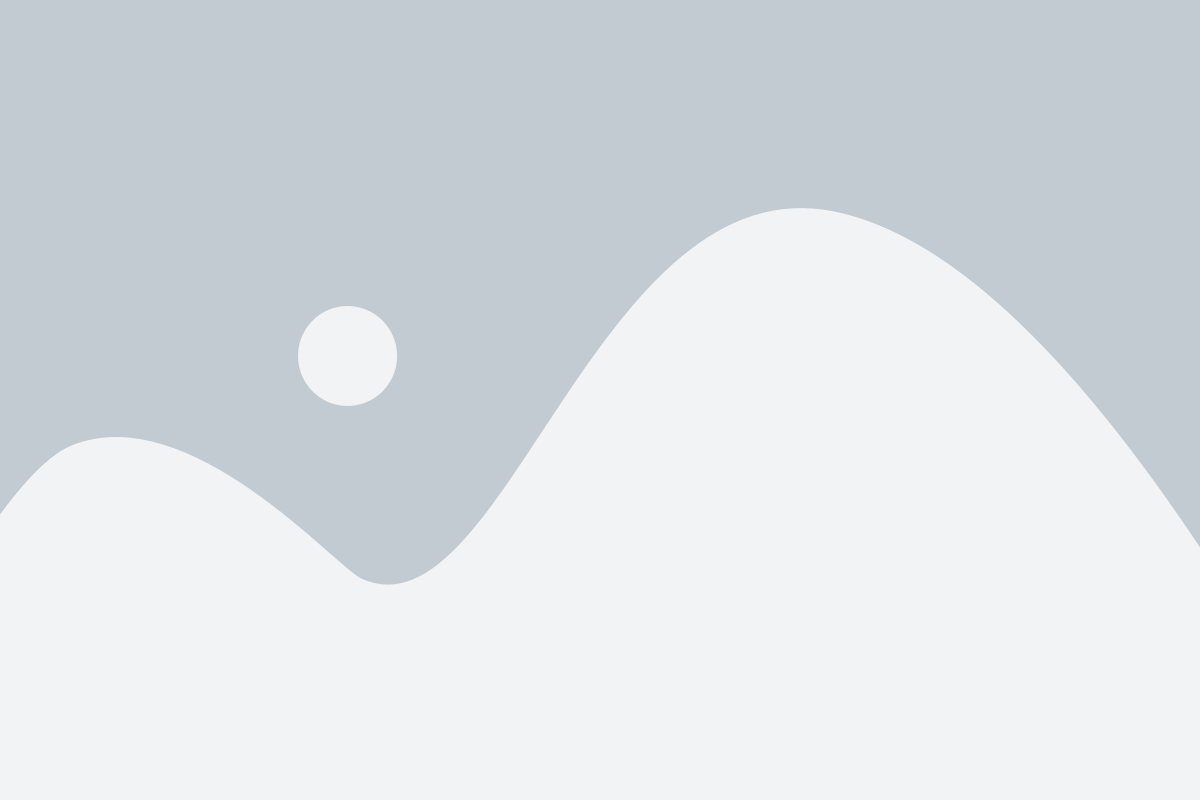
Insufficient Heat Input
Insufficient heat input during welding is a common cause of lack of sidewall fusion. When the heat input is too low, the temperature at the sidewalls of the joint may not reach the required level for proper fusion. As a result, the molten weld metal fails to adequately penetrate and bond with the base metal, leading to incomplete sidewall fusion.
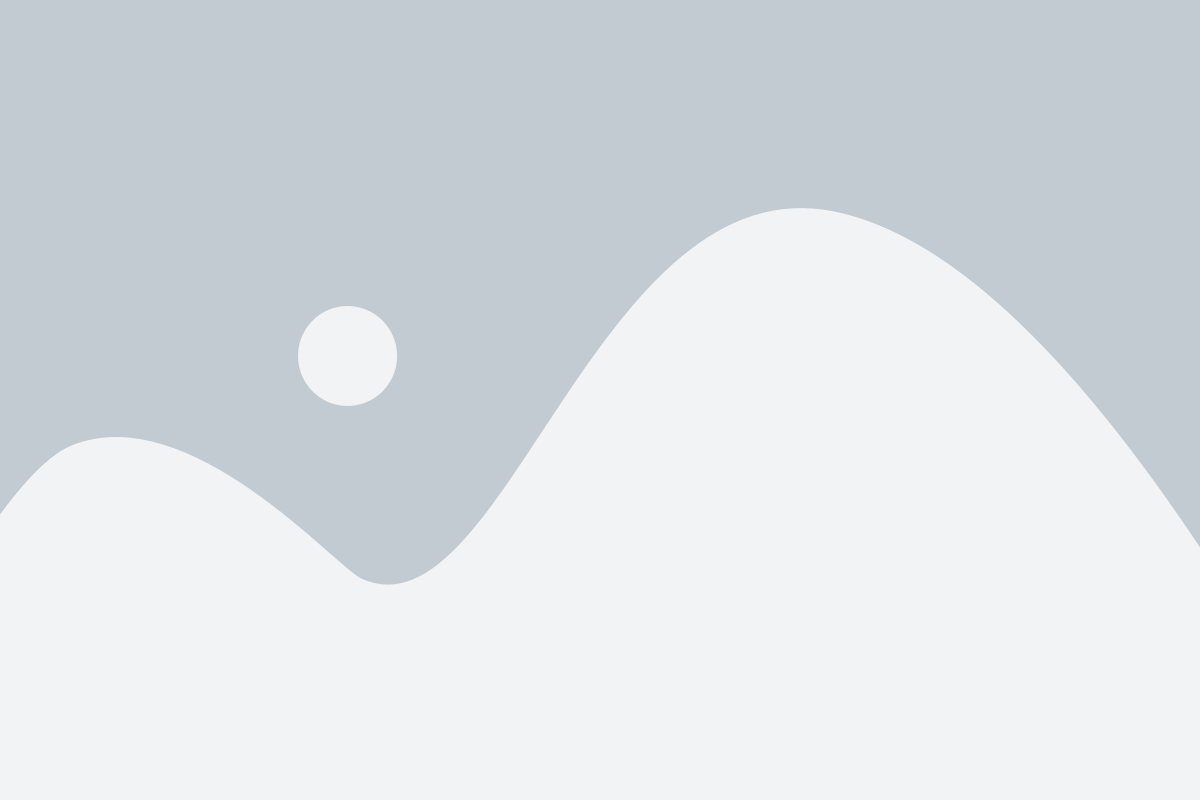
Molten Metal Flooding Ahead
In some cases, excessive molten metal may flow ahead of the welding arc, resulting in insufficient sidewall fusion. This phenomenon often occurs when welding with high currents or travel speeds, causing the molten metal to flood the weld pool before proper fusion can occur.
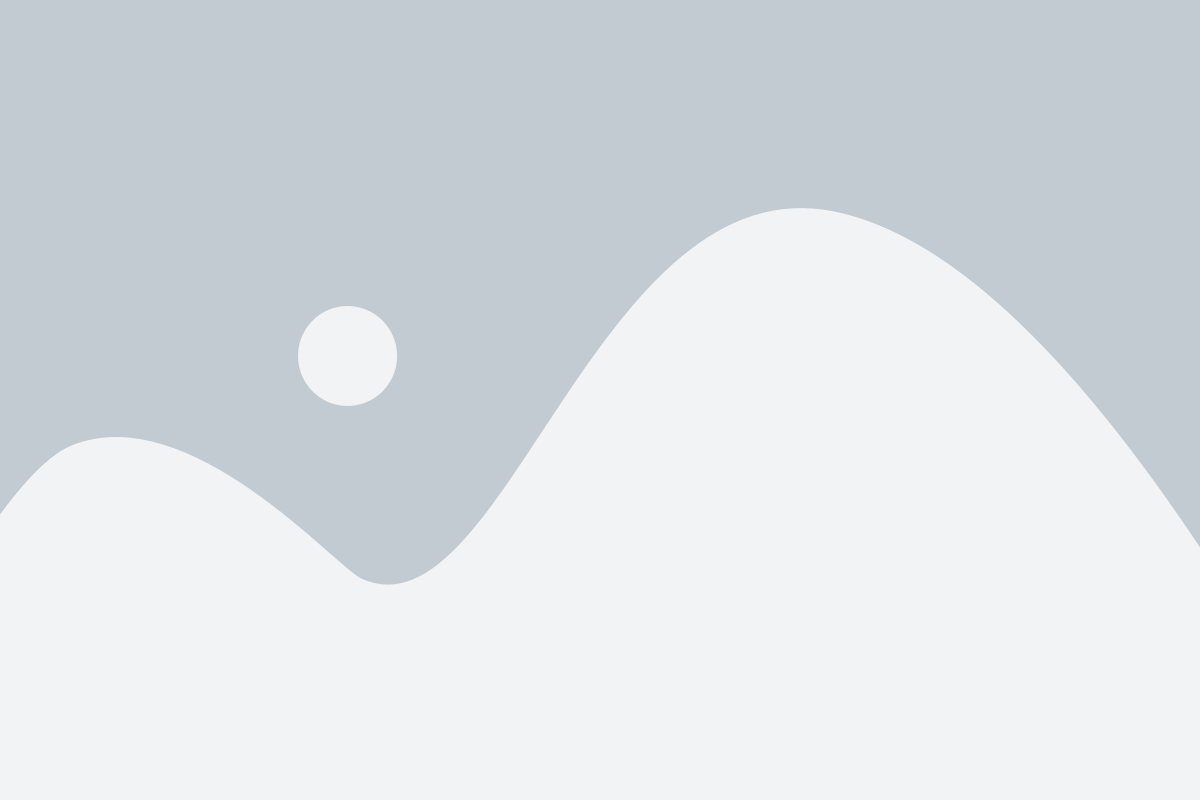
Improper Weld Surface Preparation
Presence of oxide or scale on the surface of the base metal can hinder sidewall fusion by acting as a barrier to proper bonding. Oxide or scale forms naturally on metal surfaces, especially during storage or handling, and must be removed through thorough cleaning before welding. Failure to remove oxide or scale effectively can prevent the molten weld metal from making direct contact with the base metal, leading to lack of sidewall fusion.
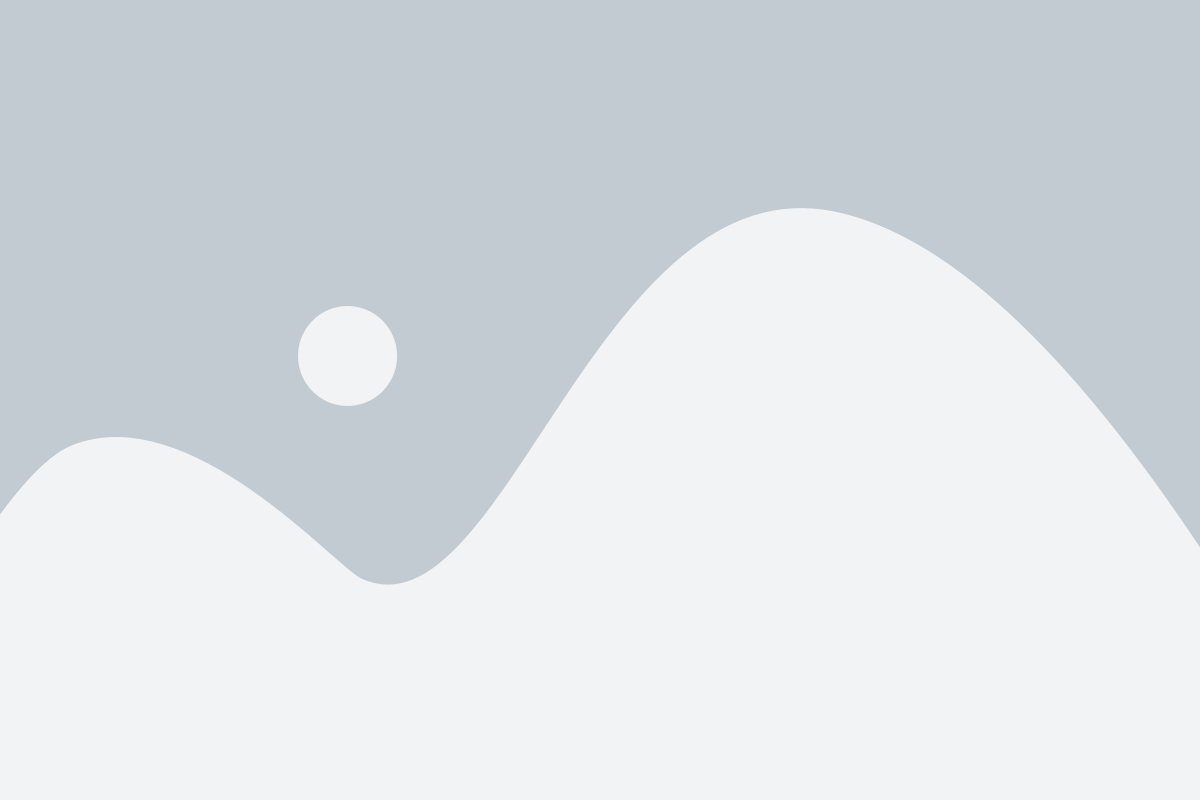
Excessive Inductance
In GMAW dip transfer, excessive inductance settings can adversely affect sidewall fusion. Inductance influences the behavior of the welding arc and the stability of the weld pool. When inductance is set too high, it can disrupt the flow of molten metal and hinder sidewall fusion.
Prevention against Lack of Sidewall Fusion
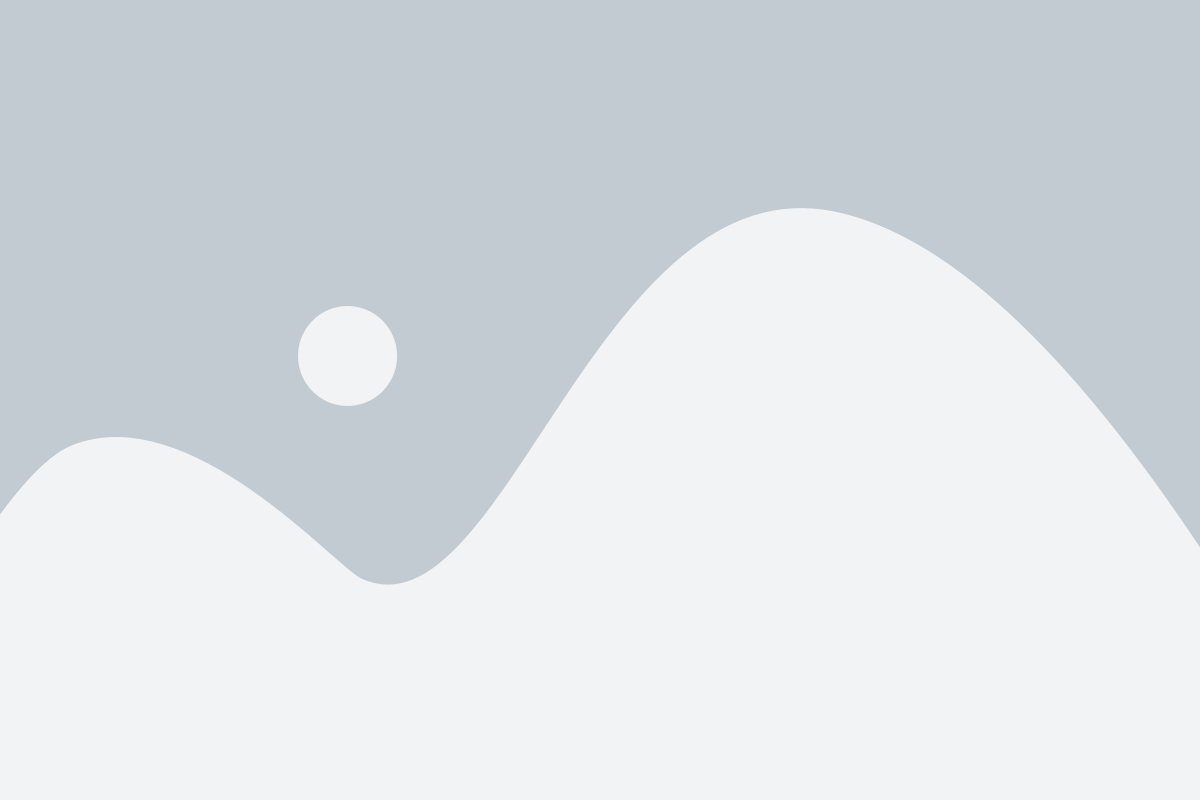
Optimizing Heat Input
Adequate heat input is essential for promoting sidewall fusion in welding. By increasing heat input through adjustments in welding parameters such as increasing arc current & voltage, and decreasing travel speed, welders can ensure that the sidewalls of the joint reach the required temperature for proper fusion. Increasing heat input facilitates better penetration and bonding of the molten weld metal with the base metal, minimizing the risk of lack of sidewall fusion.
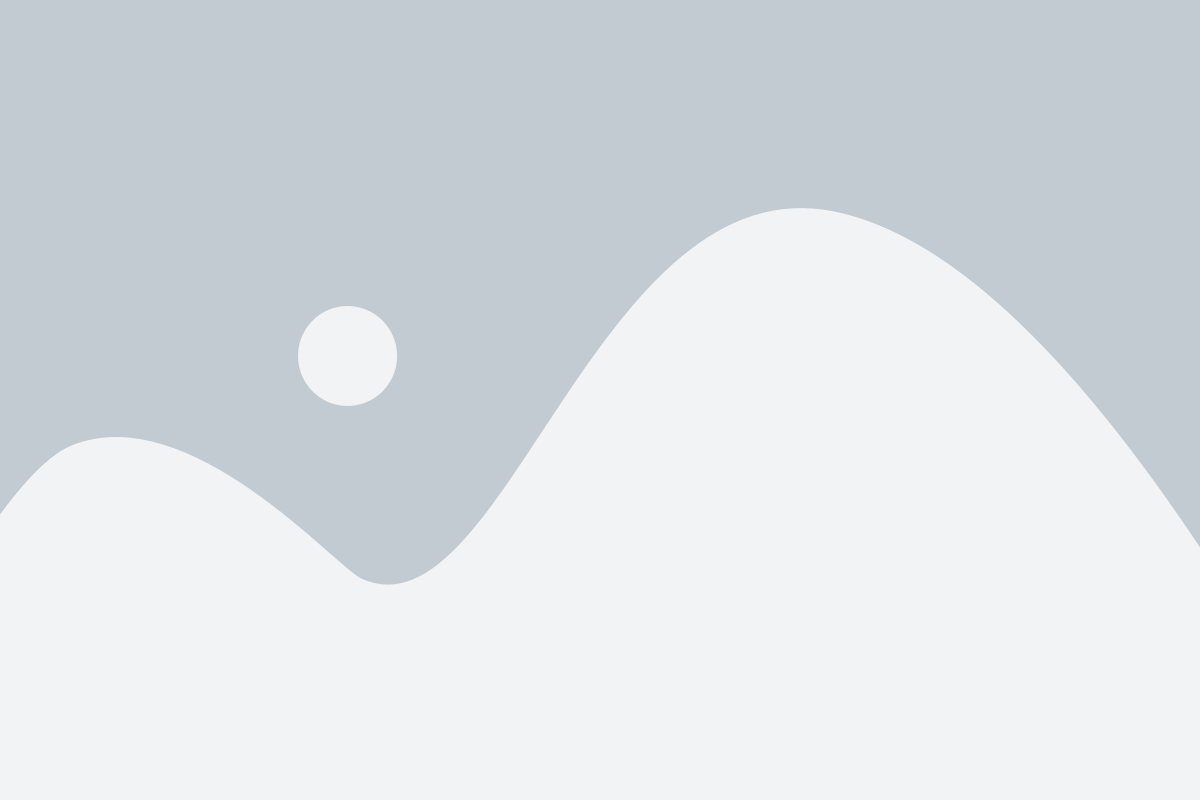
Improve Electrode & Work Position
Proper electrode and work positioning play a crucial role in promoting sidewall fusion. By optimizing the angle and orientation of the welding electrode relative to the joint, welders can ensure better access to the sidewalls and improve the deposition of weld metal. Additionally, adjusting the work position to facilitate gravity-assisted flow of molten metal can promote better sidewall fusion. Proper electrode and work positioning help ensure uniform heat distribution and penetration, reducing the likelihood of lack of sidewall fusion.
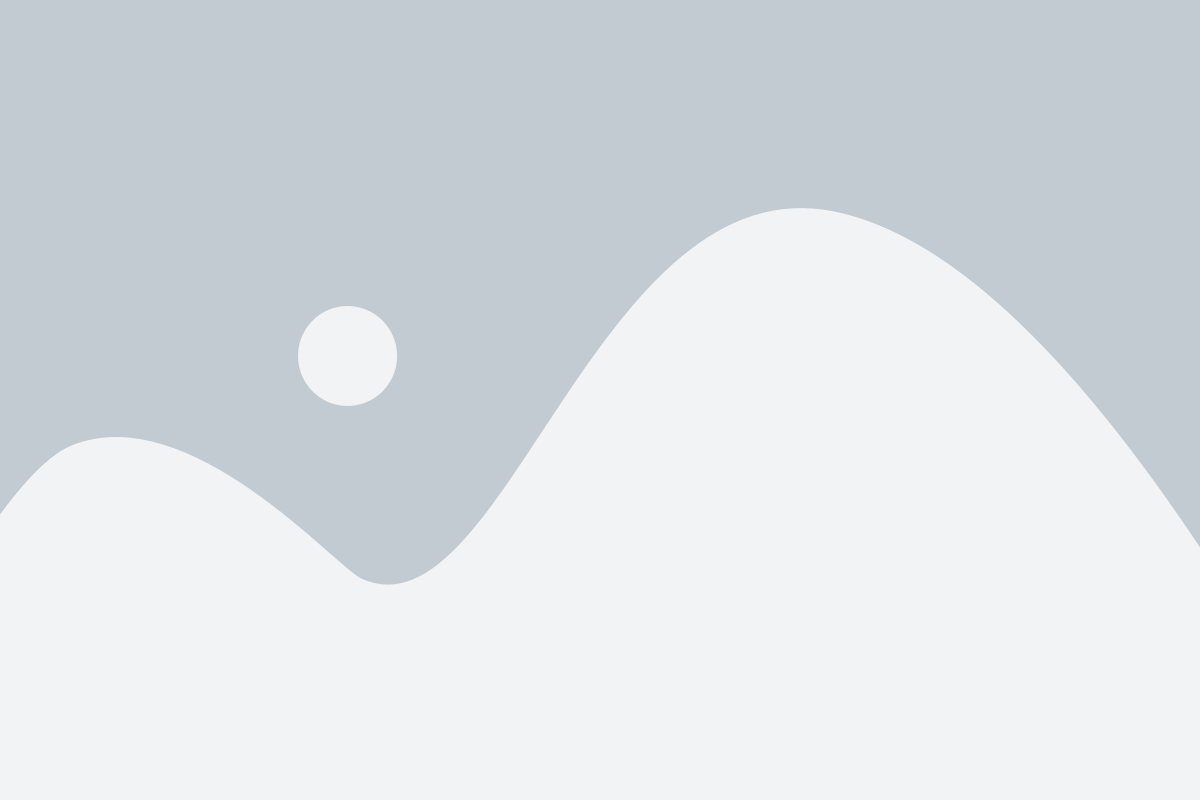
Proper Weld Surface Preparation
Thorough preparation of the weld surface is essential for preventing lack of sidewall fusion. Proper cleaning of the base metal to remove contaminants such as oil, grease, and oxide layers is critical to promoting effective bonding between the weld metal and the base metal. Additionally, ensuring proper fit-up and alignment of the joint helps facilitate better sidewall fusion by promoting intimate contact between the weld metal and the base metal. Proper weld surface preparation creates optimal conditions for sidewall fusion, reducing the risk of defects.
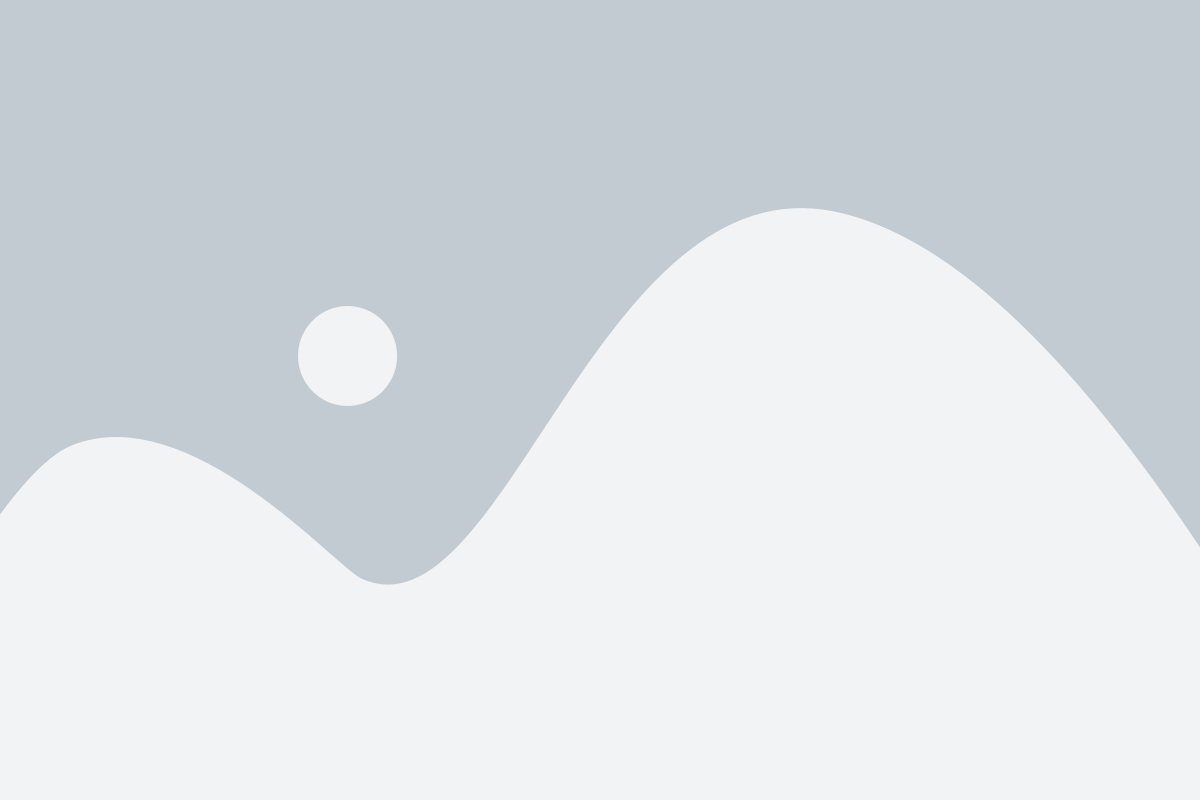
Reduce Inductance
In Gas Metal Arc Welding (GMAW) dip transfer, excessive inductance settings can hinder sidewall fusion by disrupting the flow of molten metal. By reducing inductance settings to appropriate levels, welders can improve arc stability and control the transfer of molten metal, facilitating better sidewall fusion, even if this increases spatter. Proper adjustment of inductance settings ensures consistent and uniform deposition of weld metal along the sidewalls, minimizing the risk of lack of fusion defects.
Differentiate between
Lack of Root Fusion vs. Inter-run Fusion vs. Sidewall Fusion
ASPECT | LACK OF ROOT FUSION | LACK OF INTER-RUN FUSION | LACK OF SIDEWALL FUSION |
---|---|---|---|
Definition | Absence of fusion between weld metal and parent metal at the root of a weld joint. | Absence of fusion along the fusion line between successive weld beads. | Absence of fusion between the weld and adjacent base metal at one or both sides of the weld joint. |
Location | Occurs at the root of the weld joint. | Occurs between successive weld passes or layers. | Occurs at one or both sidewalls of the weld joint. |
Causes | Insufficient heat input, excessive inductance in GMAW dip transfer, improper electrode size, use of vertical-down welding, large root face, small root gap, incorrect angle or electrode manipulation, excessive misalignment at root | Low arc current, high travel speed, inaccurate bead placement. | Insufficient heat input, molten metal flooding ahead of arc, oxide or scale on weld preparation, excessive inductance in GMAW dip transfer. |
Prevention | Optimize heat input, manage inductance, adjust electrode size, use of vertical-up welding, reduce root face, increase root gap, improve electrode angle, correct root misalignment. | Increase arc current, reduce travel speed, retrain welder. | Optimize heat input, improve electrode angle & work position, improve weld surface preparation, reduce inductance, even if this increases spatter |
Consequences | Weak bond between weld metal and parent metal, reduced joint strength. | Lack of fusion between successive weld passes, discontinuities within weld structure. | Incomplete fusion between weld and base metal, compromised joint integrity. |