Introduction to Porosity
A Closer Look
Explore the intricate world of welding imperfections with our comprehensive guide to porosity. Porosity, also known as blowhole, is cavity type discontinuities formed when gas, such as nitrogen, oxygen, or hydrogen, becomes trapped within the weld metal during solidification. Learn about the causes of porosity, and discover preventive measures to ensure flawless welds.
Whether you are a novice welder or seasoned professional, our compact and easily digestible overview provides valuable insights to enhance your welding expertise. Dive into the fascinating realm of welding imperfections and elevate your skills to new heights today!
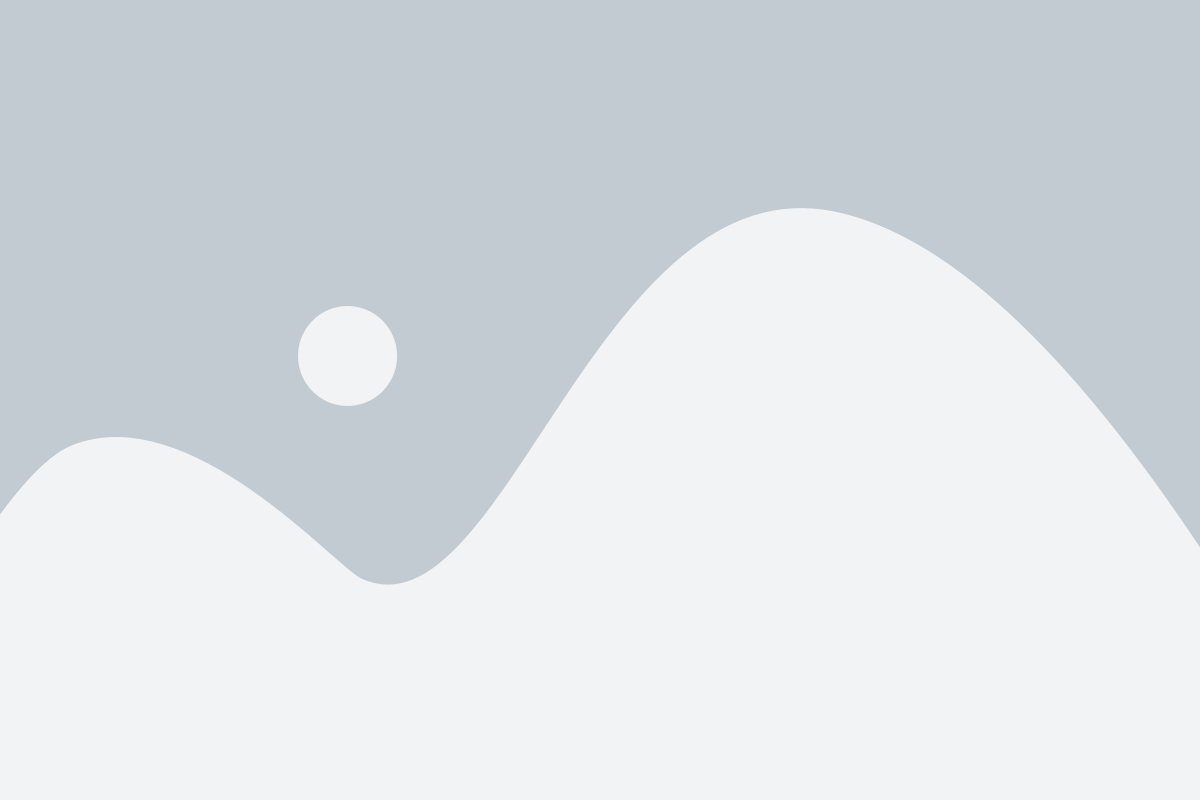
Types of Porosity
Exploring the Cavities
1) Isolated Porosity
Isolated porosity refers to individual gas cavity trapped within the weld metal, typically appearing as spherical voids and may be randomly distributed within the weld metal. Isolated porosity can occur anywhere within the weld metal. It is often found as singular, spherical voids distributed randomly throughout the weld bead.
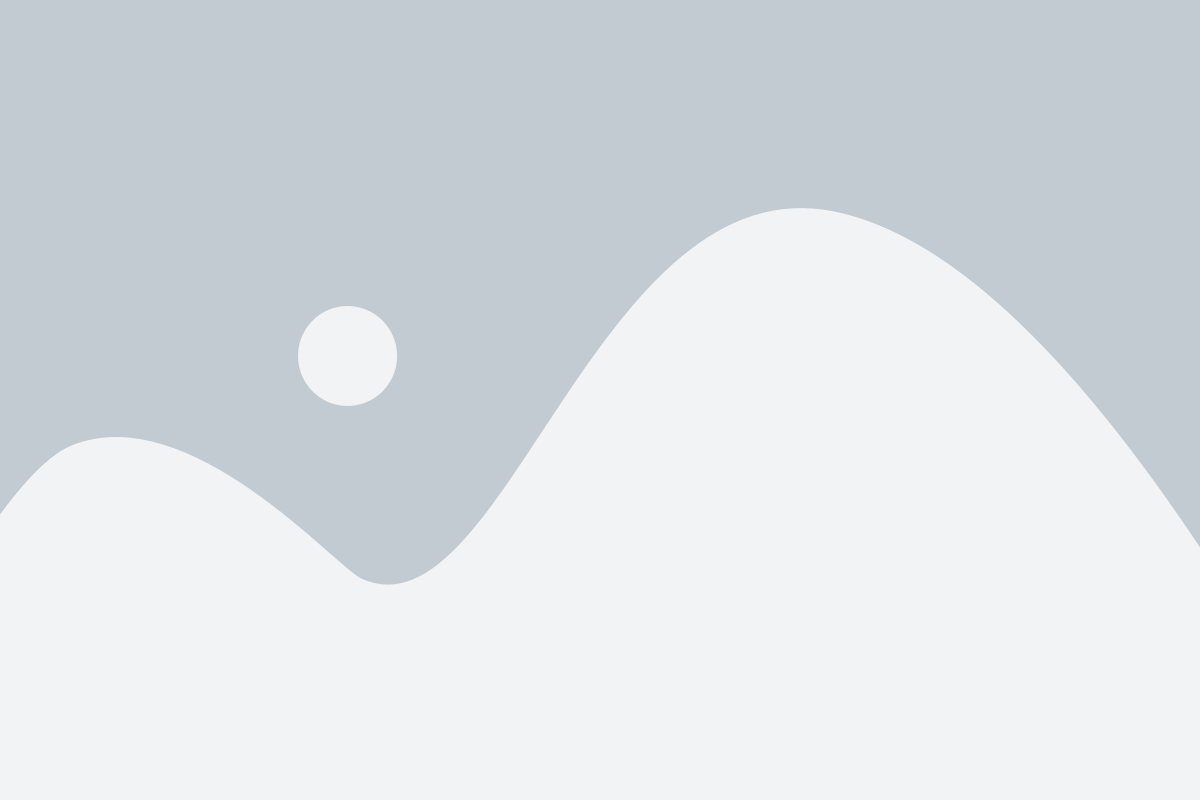
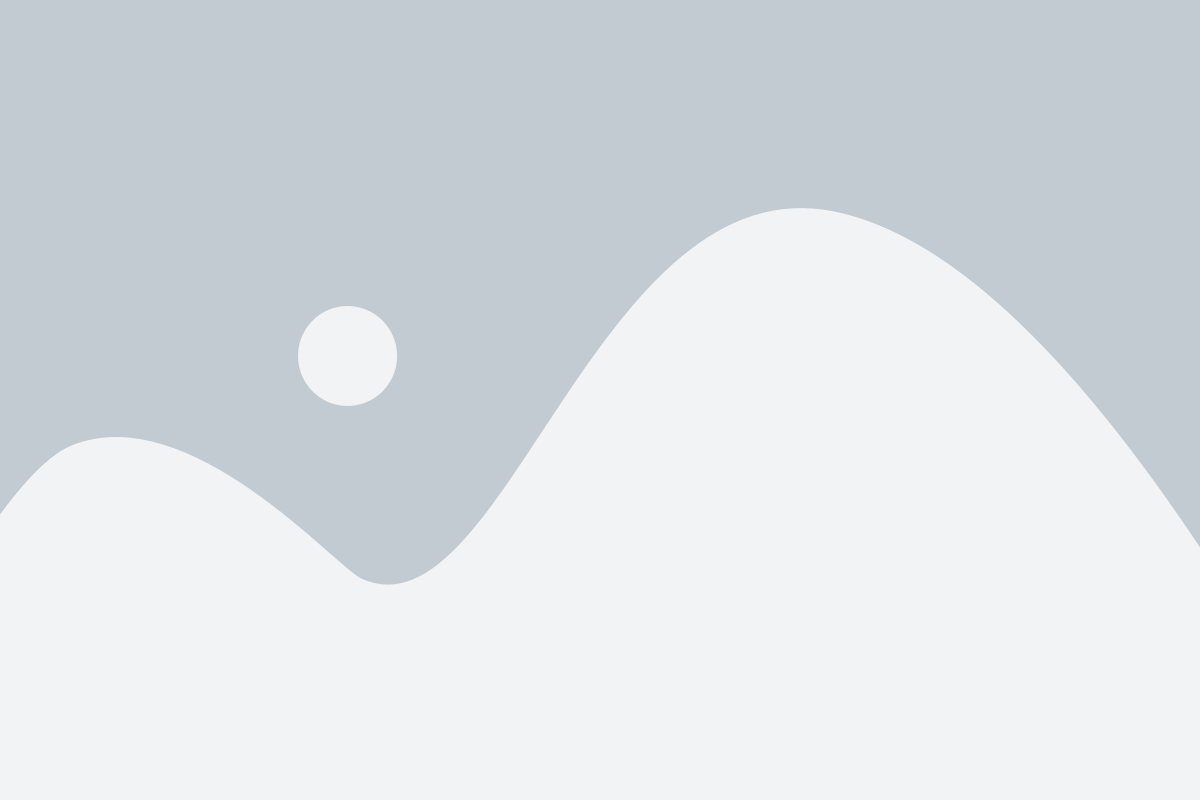
2) Uniformly Distributed Porosity
Uniformly distributed porosity is characterized by fine pores spread evenly throughout the weld bead. This type of porosity occurs when gas is uniformly distributed within the weld metal during solidification. Uniformly distributed porosity is found throughout the entire weld bead. These fine pores are evenly spread, giving a consistent appearance of tiny voids across the weld metal.
3) Aligned Porosity (Linear Porosity)
Aligned porosity, also known as linear porosity, appears as a localized array of pores oriented in a line within the weld. It forms when gas becomes trapped along specific lines or planes within the weld metal. Aligned porosity appears in a linear array, typically oriented along the weld axis. These pores can be found in a straight line or pattern within the weld metal, often due to defects in the weld process that create a path for gas entrapment.
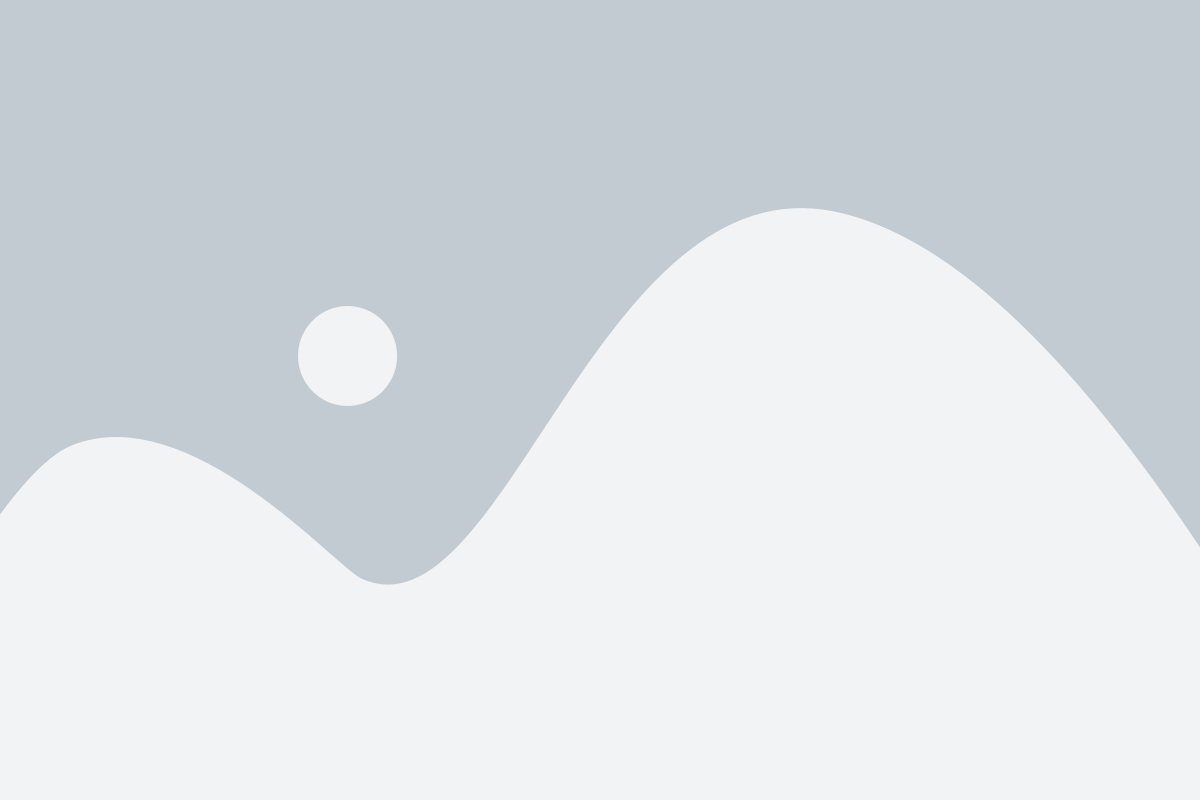
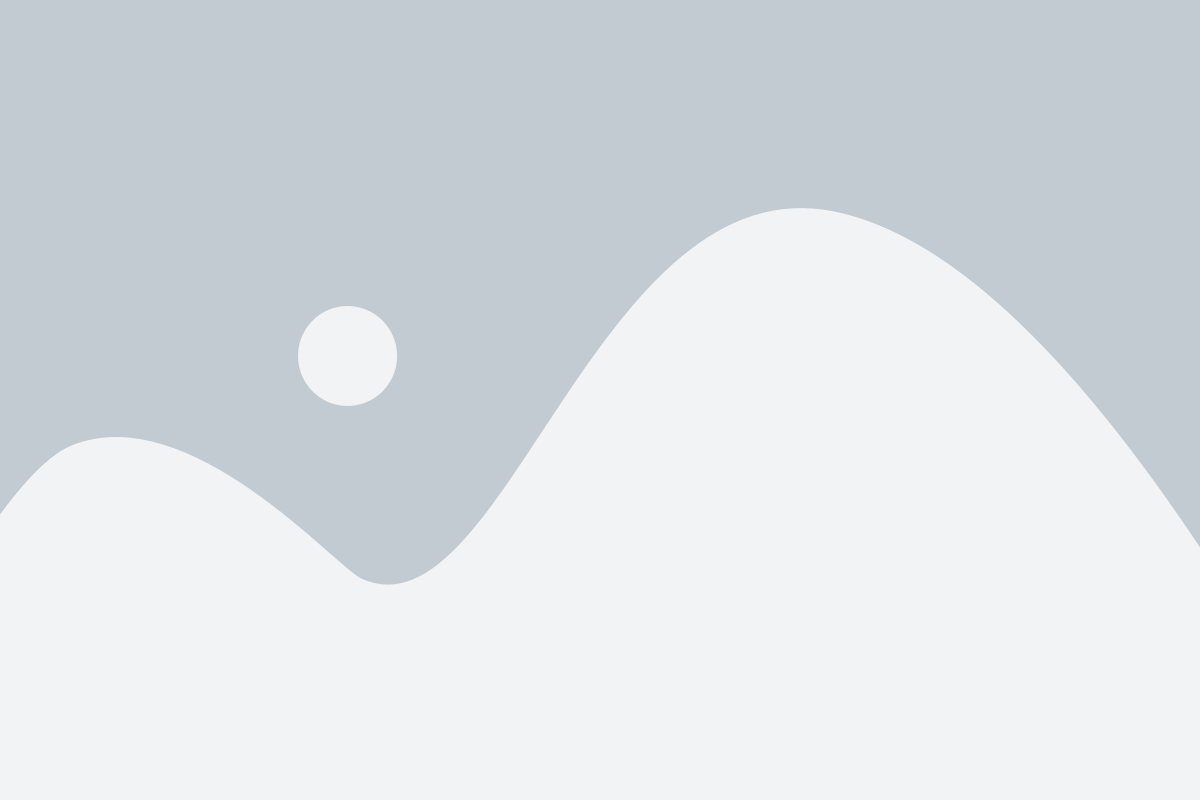
4) Cluster Porosity
Cluster porosity refers to a localized array of pores with a random geometric distribution within the weld metal. Cluster porosity occurs when multiple gas pockets are clustered together within the weld metal. Cluster porosity is located in localized areas within the weld bead. These clusters of pores are randomly distributed in a specific region, rather than being spread out uniformly.
5) Elongated Porosity (Hollow Bead)
Elongated porosity, also known as hollow bead, is a form of porosity having a length greater than its width that lies approximately parallel to the weld axis. Elongated porosity is found along the weld axis, particularly in the root bead. These elongated voids run parallel to the direction of welding and can be found in the root or body of the weld metal.
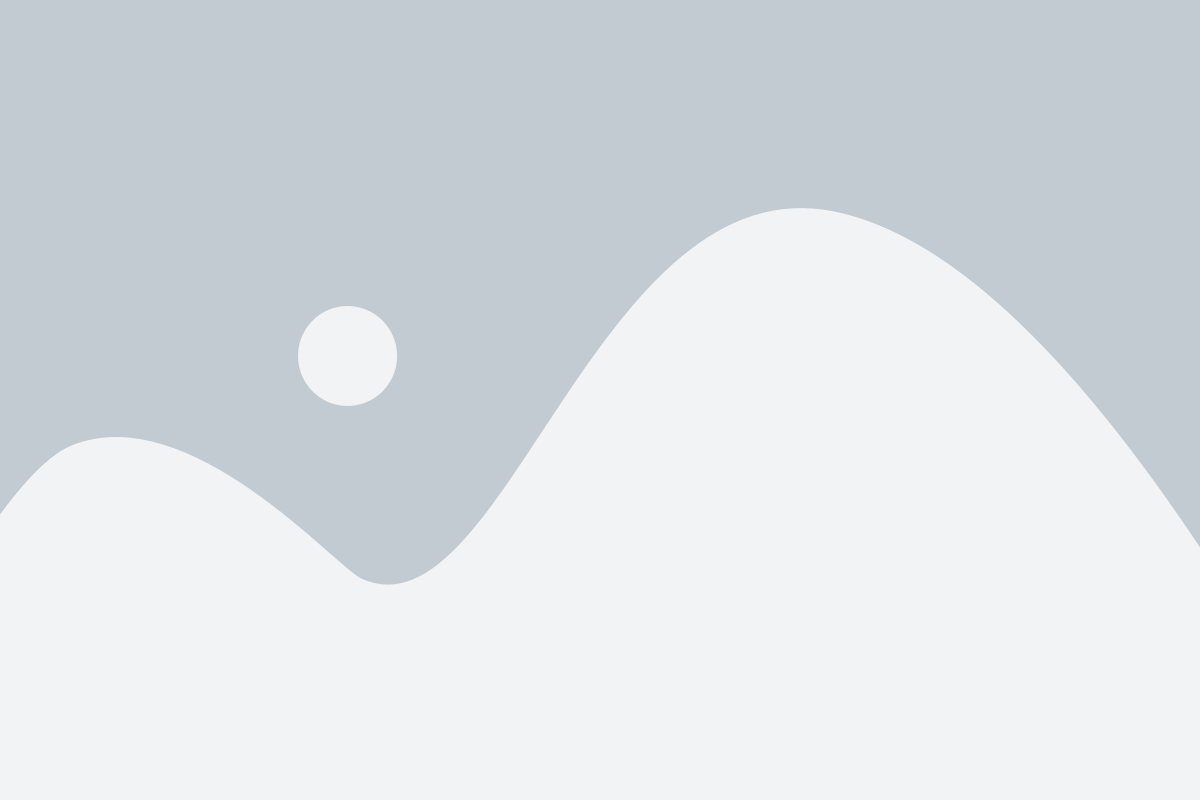
Causes for the Above Types of Porosity
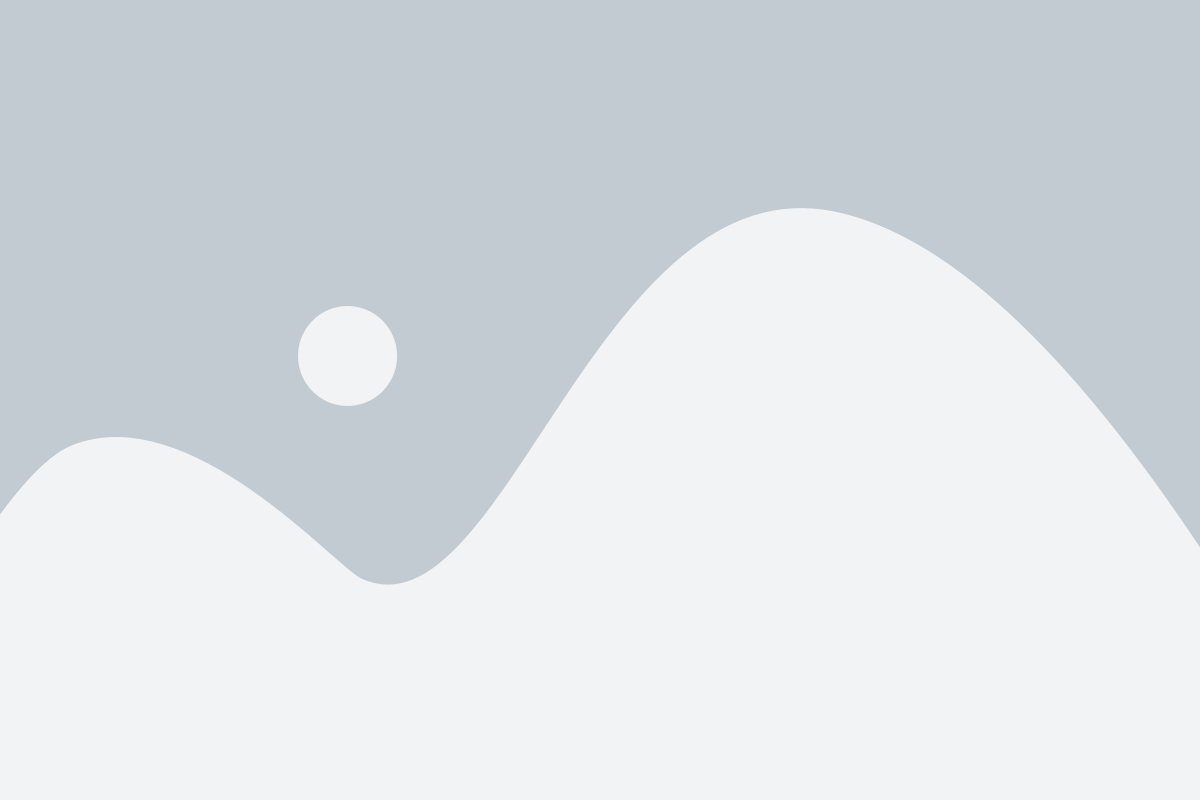
Damp Fluxes or Corroded Electrodes (SMAW)
In SMAW, moisture in the flux or corrosion on the electrode can decompose into hydrogen gas when exposed to the high temperatures of the welding arc. This hydrogen gas becomes trapped in the molten weld pool, leading to the formation of isolated gas cavities (porosity) as the weld solidifies.
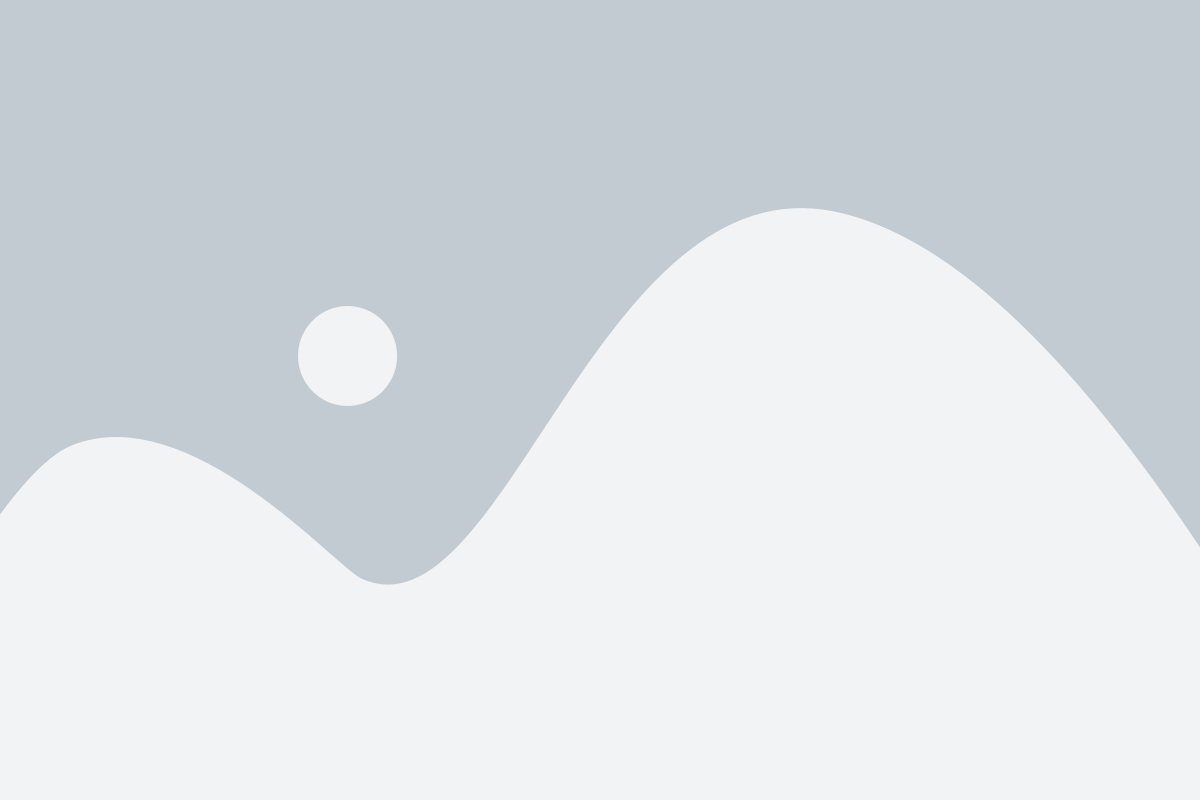
Contaminated Prepared Surface
Contaminants such as grease, hydrocarbons, or water on the surface of the material to be welded vaporize upon exposure to the welding heat, releasing gases into the weld pool. The rapid formation and entrapment of these gases result in isolated pores within the solidified weld metal.
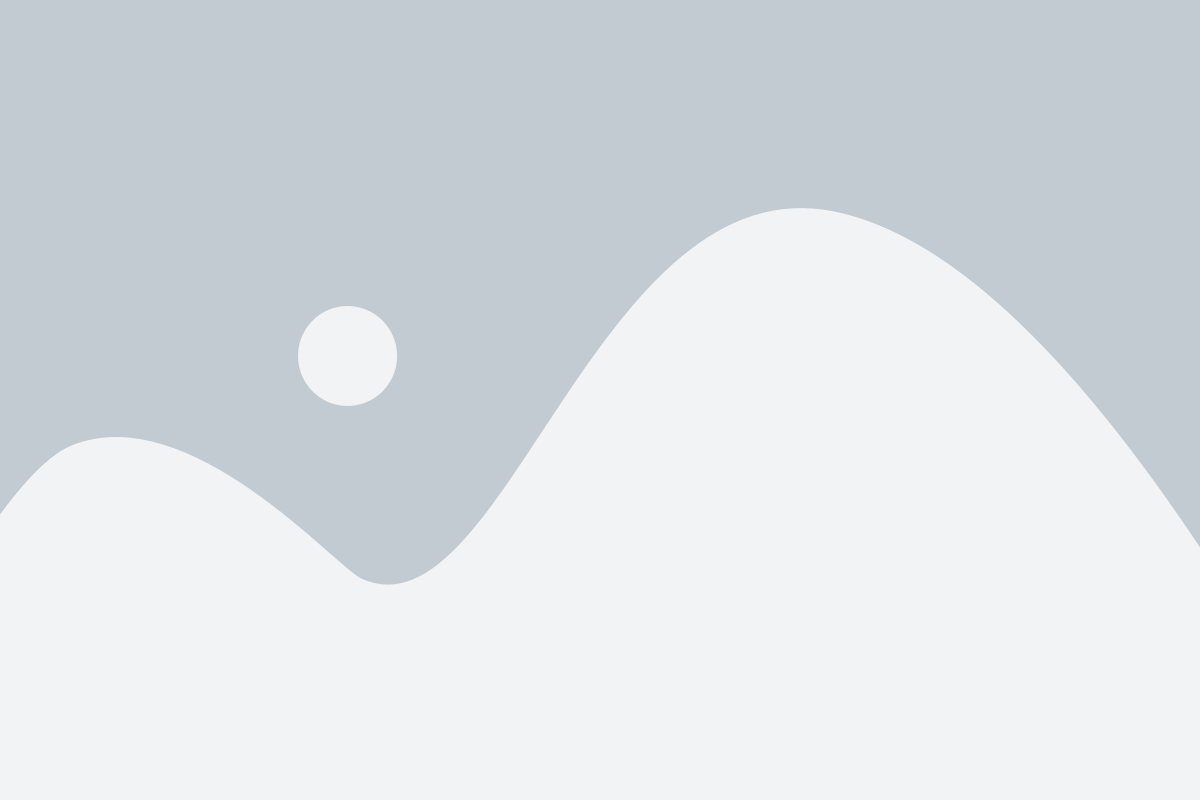
Air Entrapment in Gas Shield
In GTAW & GMAW, leaks in the gas supply system or improper setup can allow atmospheric air to mix with the shielding gas. Even a small amount of air can introduce oxygen and nitrogen into the weld pool, forming isolated gas pockets as the weld solidifies.
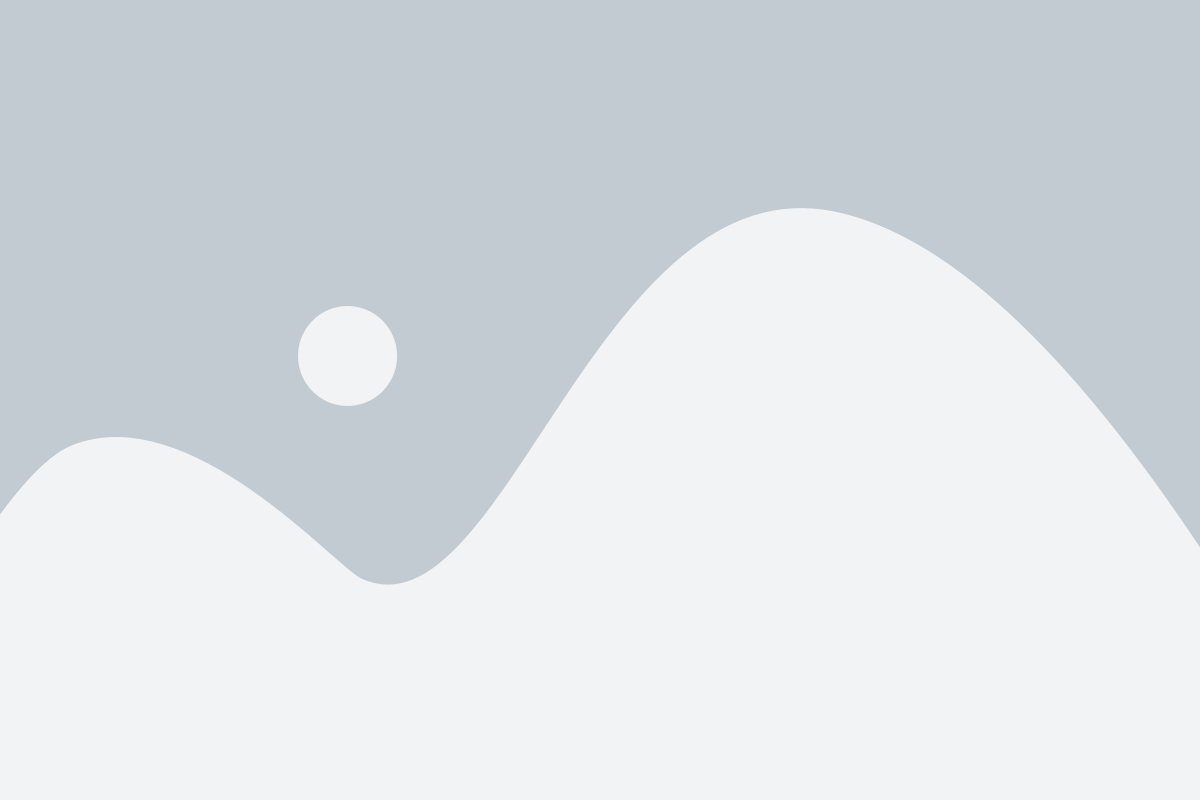
Insufficient Deoxidant
If the electrode, filler material, or parent metal lacks sufficient deoxidants like manganese, silicon & aluminium, gases such as oxygen and nitrogen are not adequately removed. These gases remain dissolved in the molten weld pool and are trapped as the metal solidifies, resulting in isolated porosity.
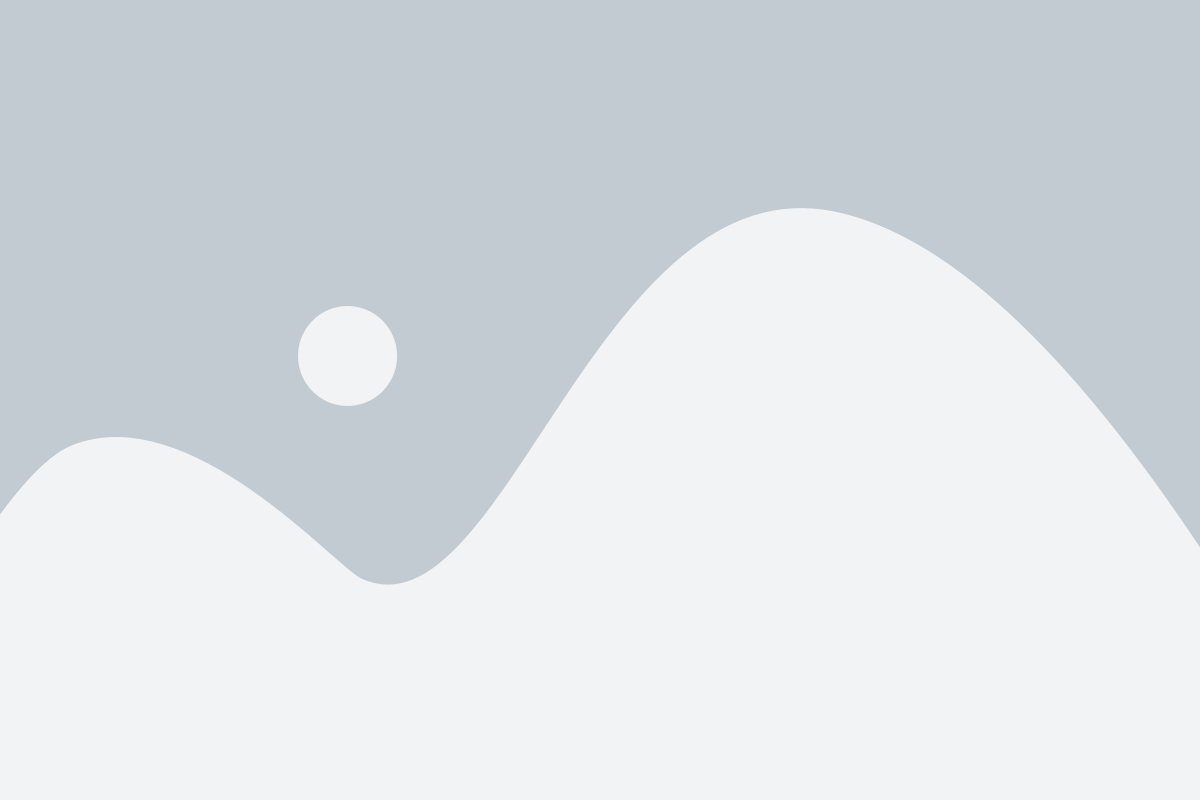
High Arc Voltage or Length
High arc voltage or long arc length increases the weld pool's exposure to the surrounding atmosphere. This exposure allows more atmospheric gases to enter the weld pool, causing isolated gas pockets as the metal solidifies.
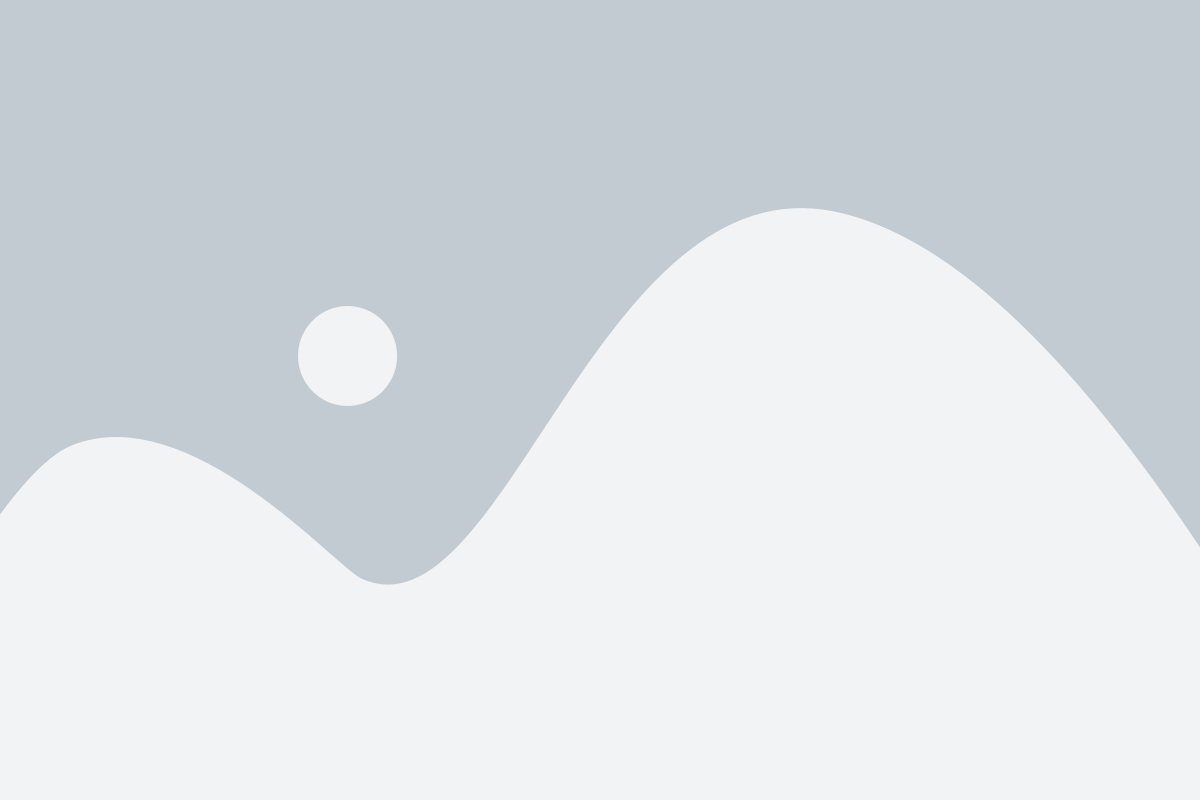
High Shielding Gas Flowrate
An excessively high shielding gas flow rate can create turbulence in the gas shield in GTAW and GMAW processes. Turbulence disrupts the protective gas shield, allowing atmospheric gases to mix with the shielding gas. This mixing introduces oxygen and nitrogen into the weld pool, leading to isolated gas entrapment and porosity as the weld solidifies.
Prevention against the Above Types of Porosity
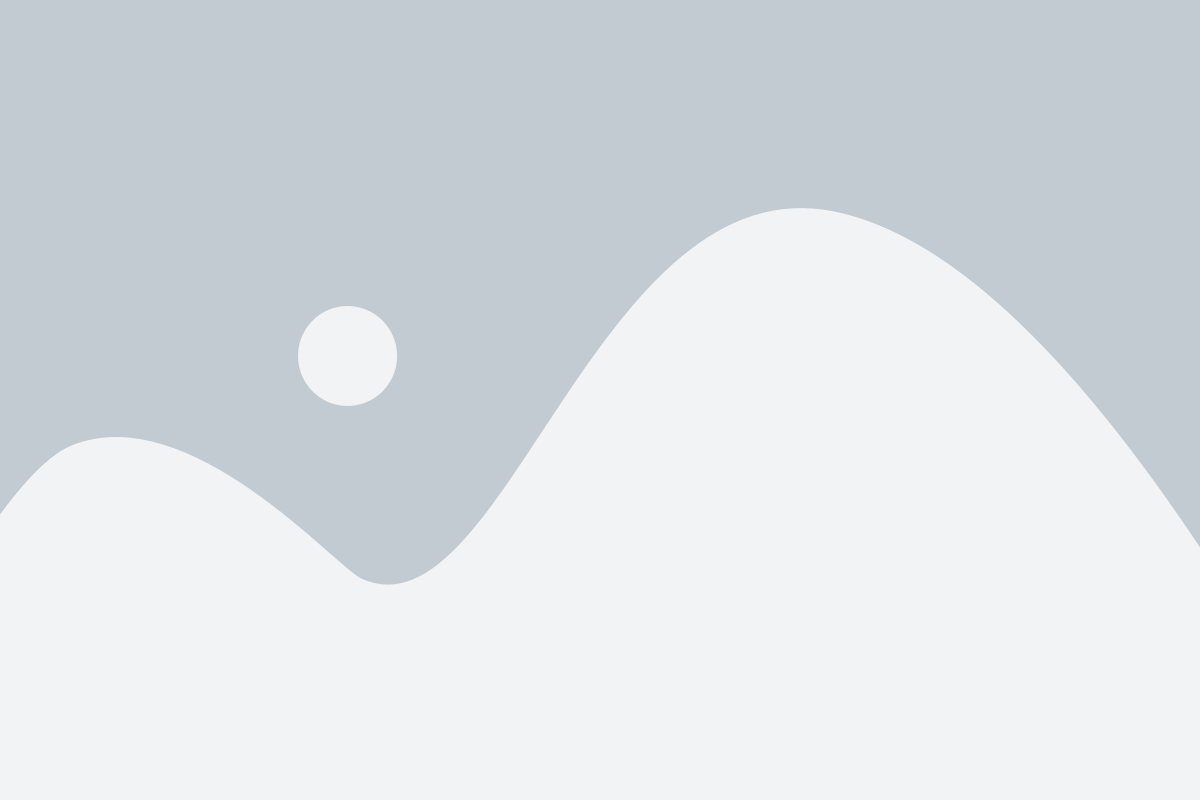
Dry Non-Corroded Electrodes
Store electrodes in a moisture-controlled environment to prevent the absorption of moisture. Use fresh, non-corroded electrodes to avoid introducing hydrogen into the weld pool, by regularly inspecting electrodes for any signs of damage or contamination before use.
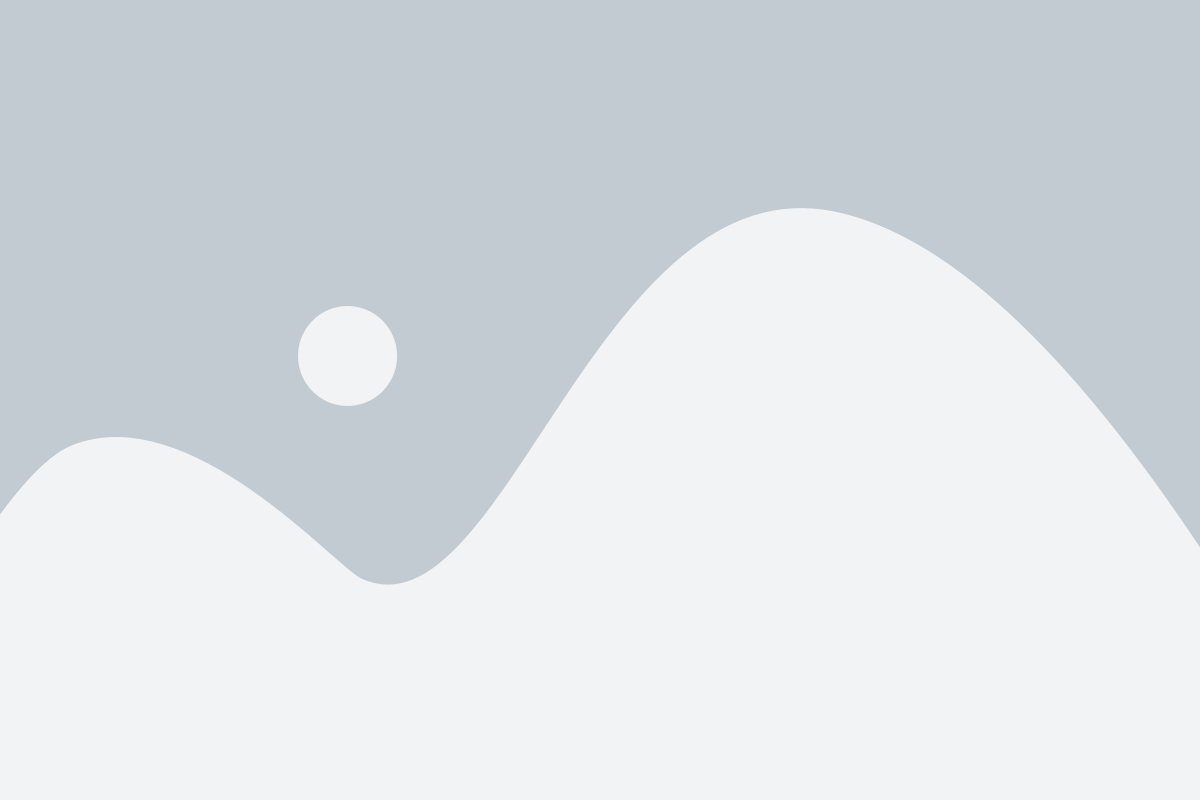
Clean Prepared Surface
Remove all grease, oil, rust, and other contaminants from the weld area using appropriate cleaning methods such as degreasing, wire brushing, or grinding. Ensure that the surface is dry and free from any residue before starting the welding process.
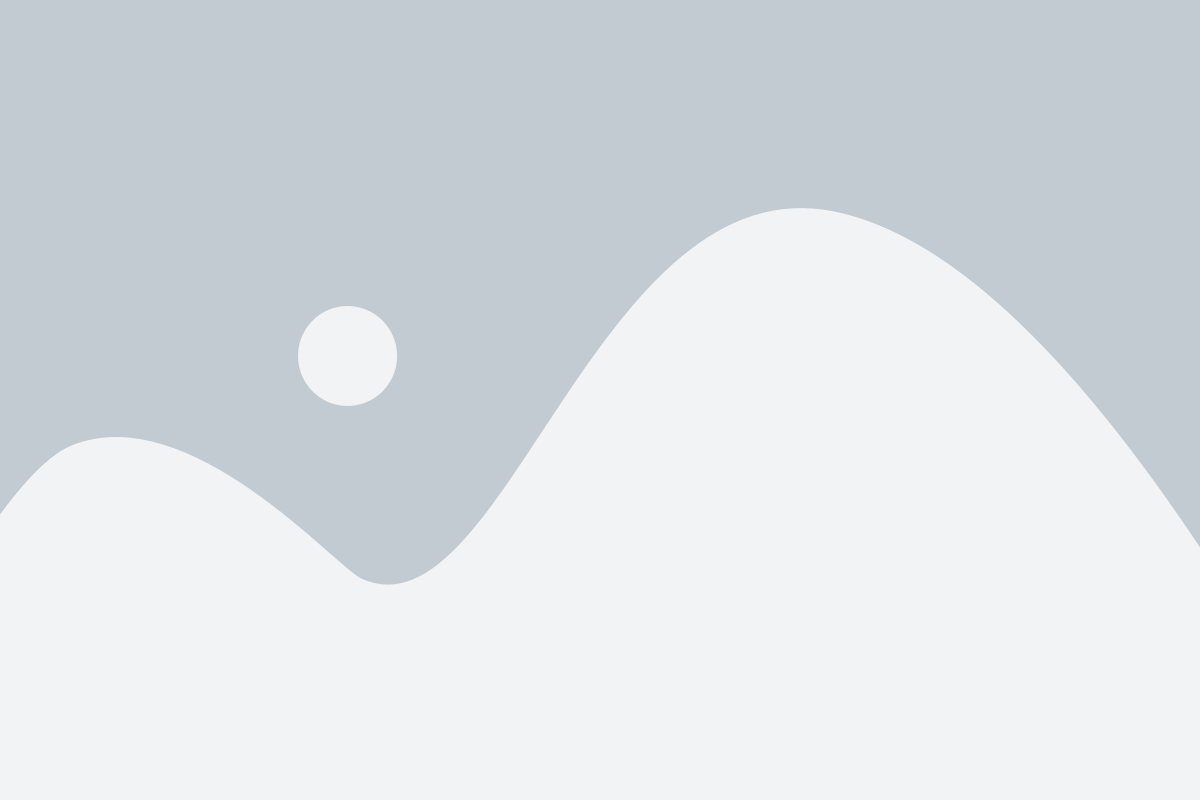
Check Hose Connections
Inspect gas hoses and connections for leaks or damage regularly. Ensure tight, secure connections to prevent air from entering the shielding gas system. Use bubble soap solution to check for leaks and repair any detected issues promptly to maintain an effective gas shield.
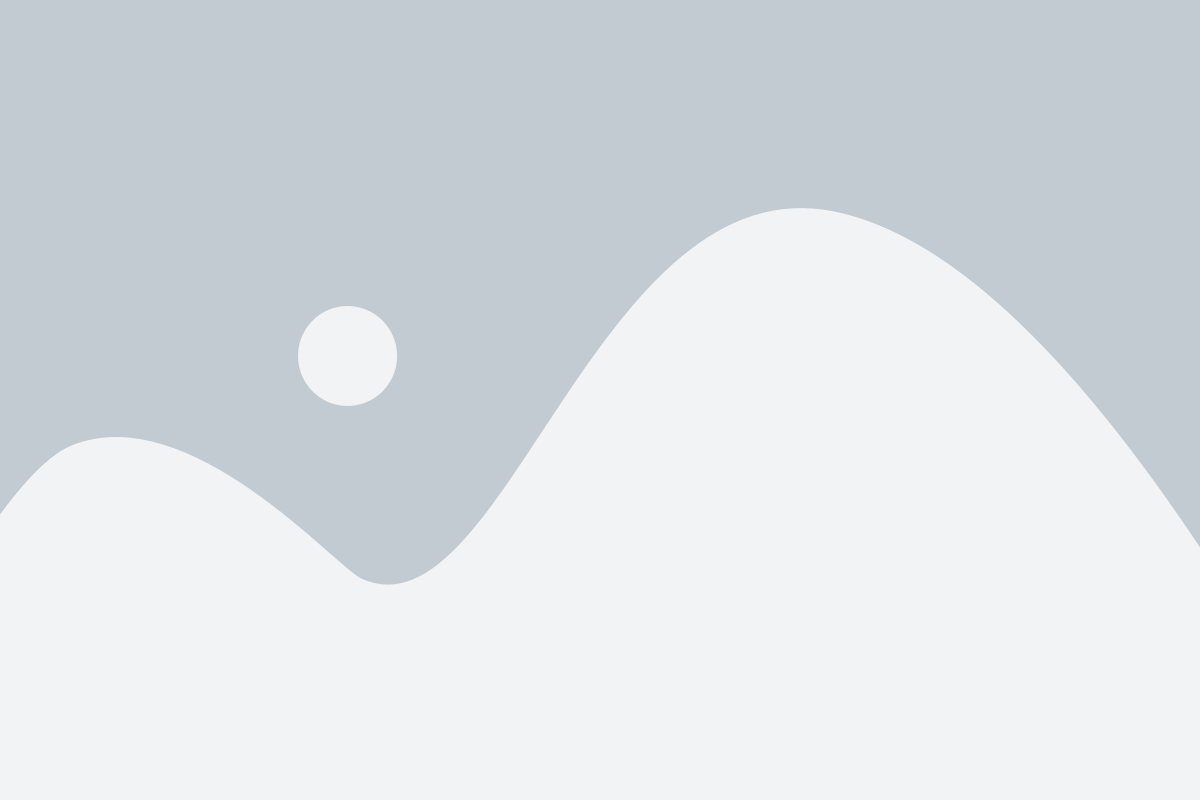
Sufficient Deoxidant Electrodes
Choose electrodes specifically formulated with deoxidizing agents such as manganese, silicon & aluminium. These deoxidants help remove oxygen from the weld pool, reducing the risk of gas entrapment. Follow manufacturer recommendations for electrode selection to match the welding application and base material.
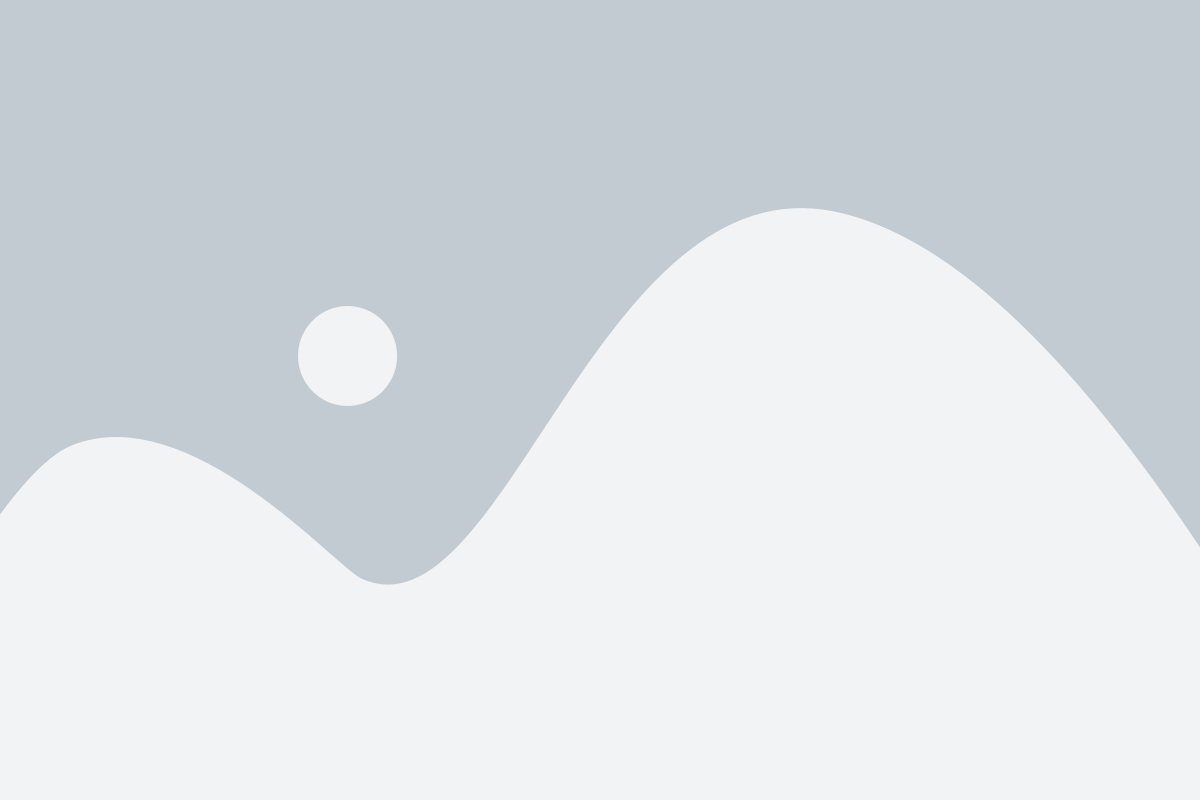
Reduce Voltage & Arc Length
Maintain an optimal arc length to minimize the exposure of the weld pool to the surrounding atmosphere. Avoid excessive arc voltage, which can increase the potential for atmospheric gas absorption. Adjust welding parameters to ensure a stable arc and consistent weld quality.
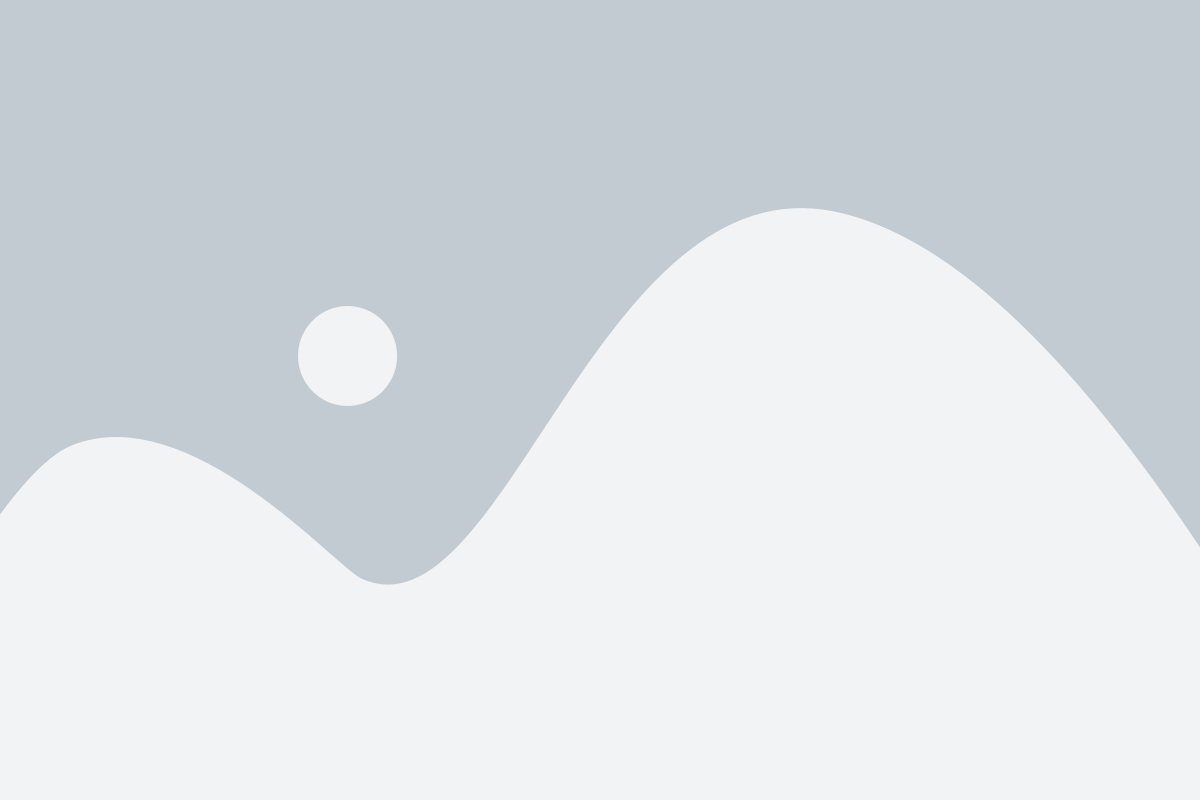
Risk of Reaction before Surface Treatment
Evaluate the compatibility of surface treatments such as primers or coatings with the welding process. Identify potential reactions that may release gases during welding, such as the decomposition of certain primers. Apply surface treatments in accordance with manufacturer guidelines.
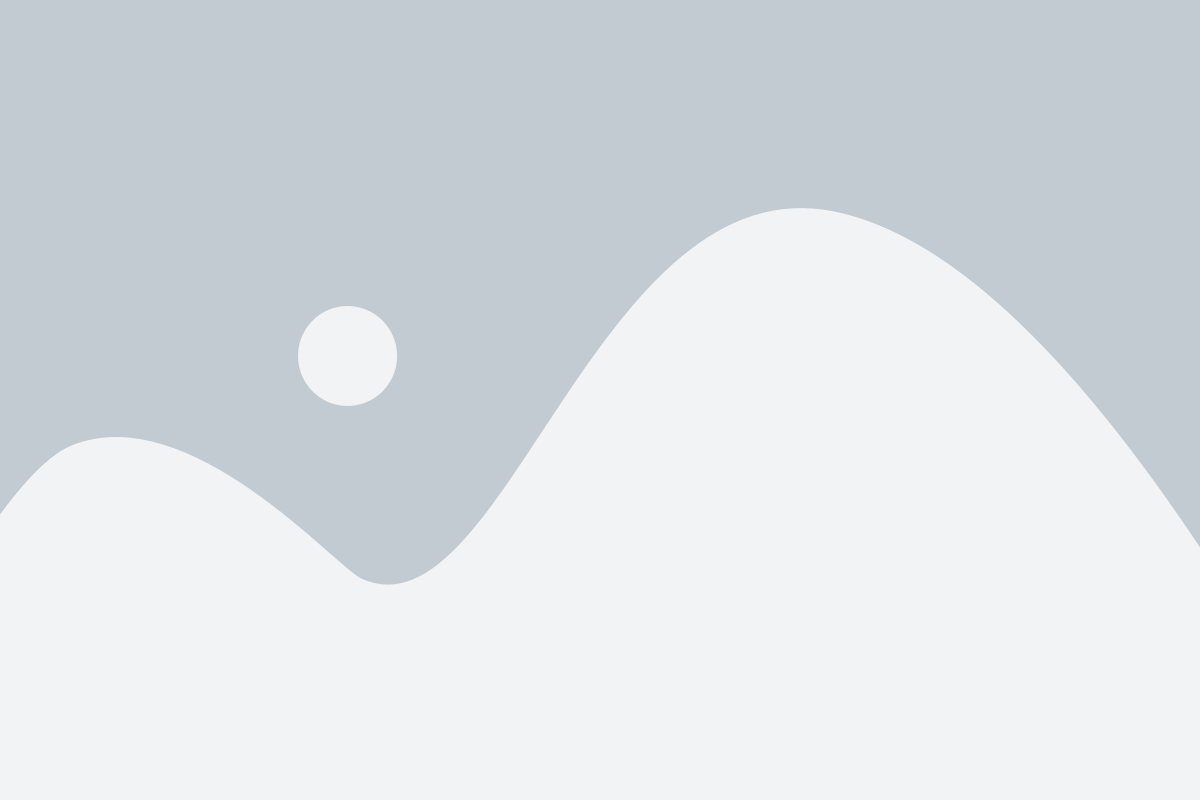
Risk of Reaction before Surface Treatment
Evaluate the compatibility of surface treatments such as primers or coatings with the welding process. Identify potential reactions that may release gases during welding, such as the decomposition of certain primers. Apply surface treatments in accordance with manufacturer guidelines.
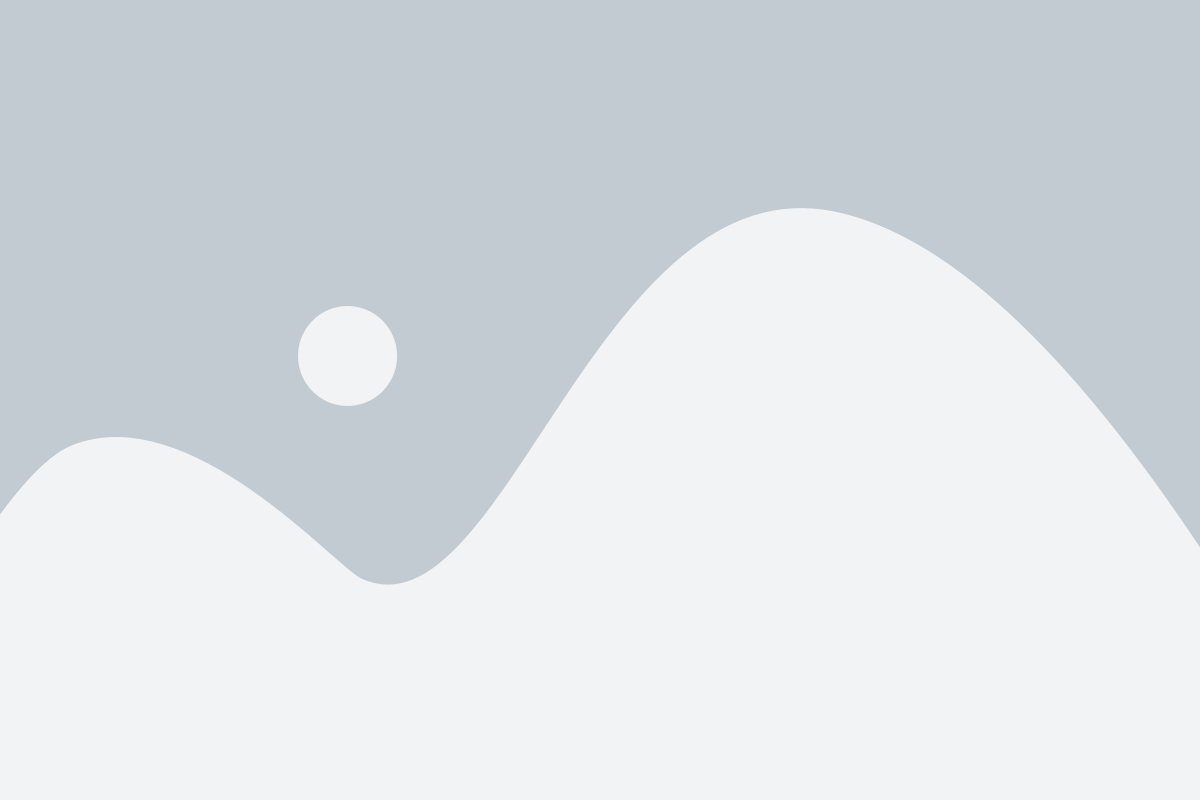
Optimize Gas Flow Rate
Set the gas flow rate according to the welding process and environmental conditions. Avoid excessively high flow rates that can create turbulence and allow atmospheric gases to mix with the shielding gas. Use flow meters and regulators to maintain a consistent and appropriate gas flow, ensuring an effective gas shield around the weld pool.
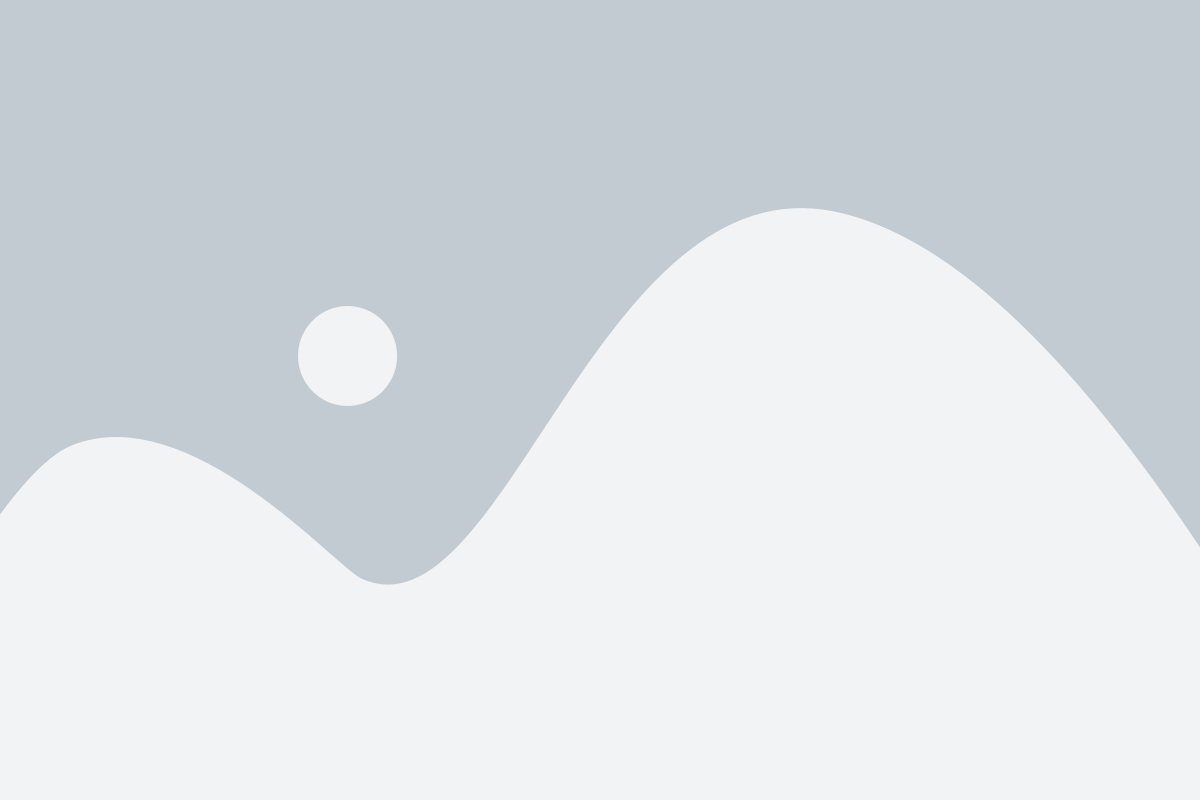
6) Piping Porosity (Wormhole)
Piping porosity, also known as wormhole, is a form of porosity having a length greater than its width that lies approximately perpendicular to the weld face. It often appears in a herringbone pattern when viewed radiographically and can extend from the weld face inward.
Causes for Piping Porosity
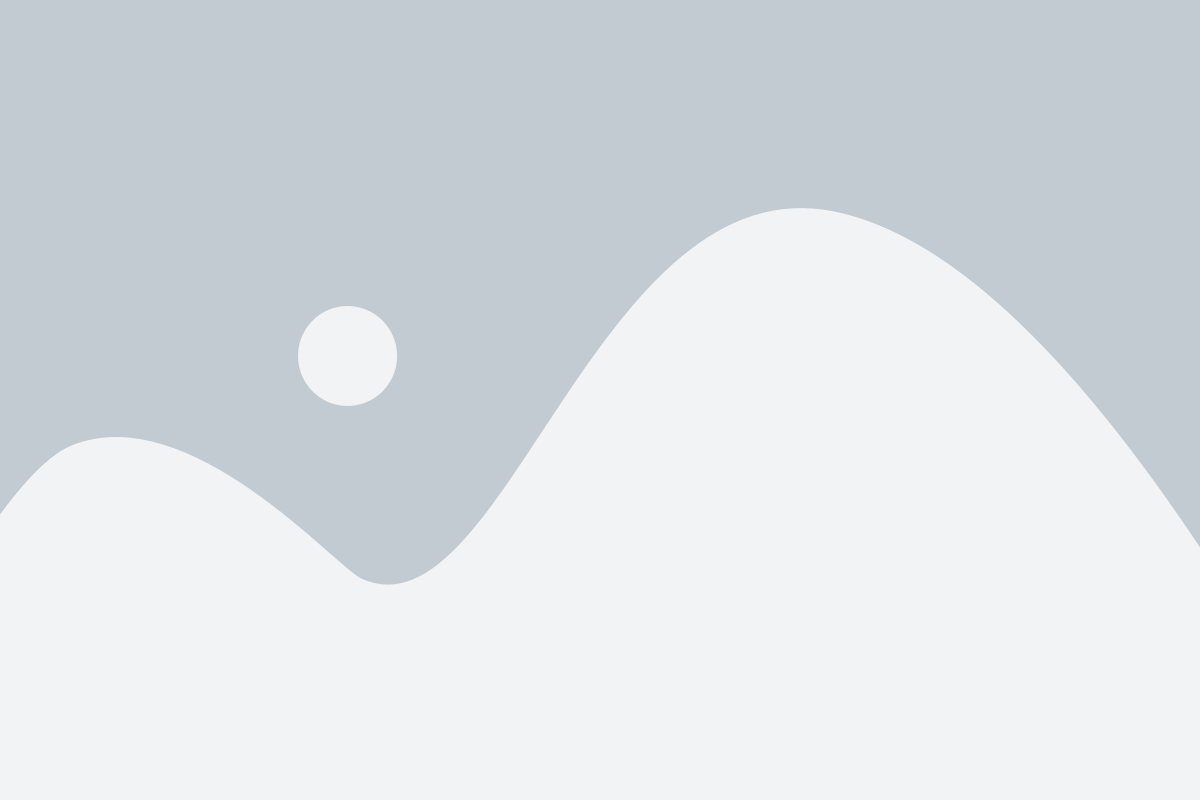
Contaminated Prepared Surface
Surface contaminants such as grease, oil, rust, and other contaminants can introduce gases into the weld pool as they vaporize during welding. These gases get trapped in the weld metal, forming elongated cavities known as wormholes which are approximately perpendicular to the weld face.
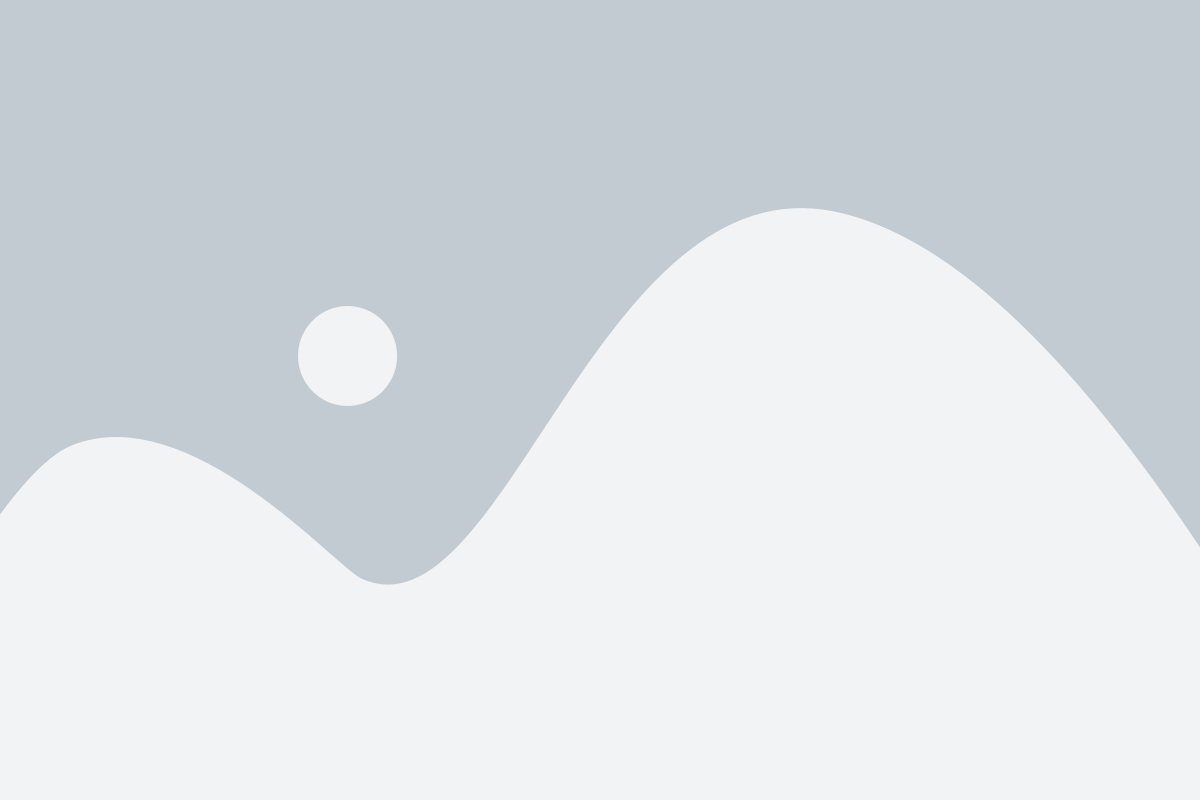
Laminated Base Metal
Layers within lamination defect can trap air and gases, which are released during the welding process. As welding heat causes these trapped gases to expand and escape, they can form elongated pores or wormholes in the weld metal.
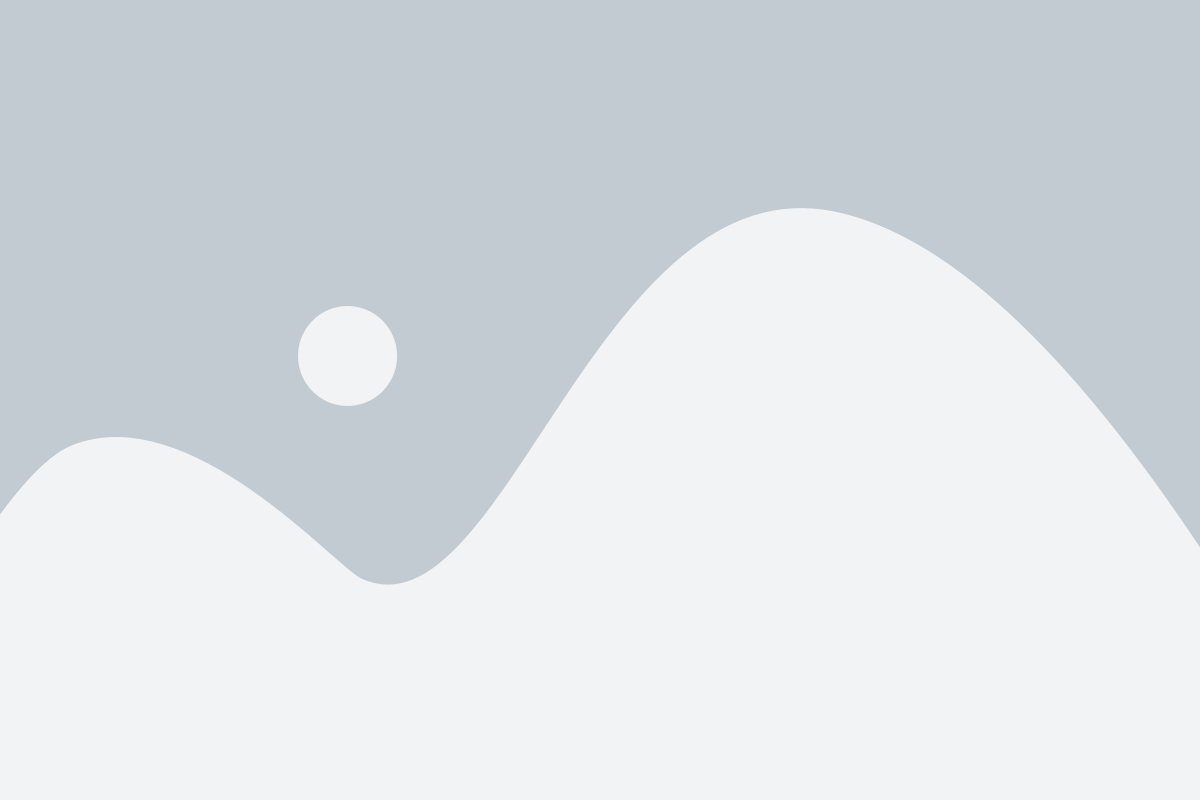
Poor Joint Geometry
Crevices formed by poor joint design or fit-up can trap gases, which then get released during welding. As the weld pool solidifies, these gases get trapped, forming wormholes perpendicular to the weld face.
Prevention against Piping Porosity
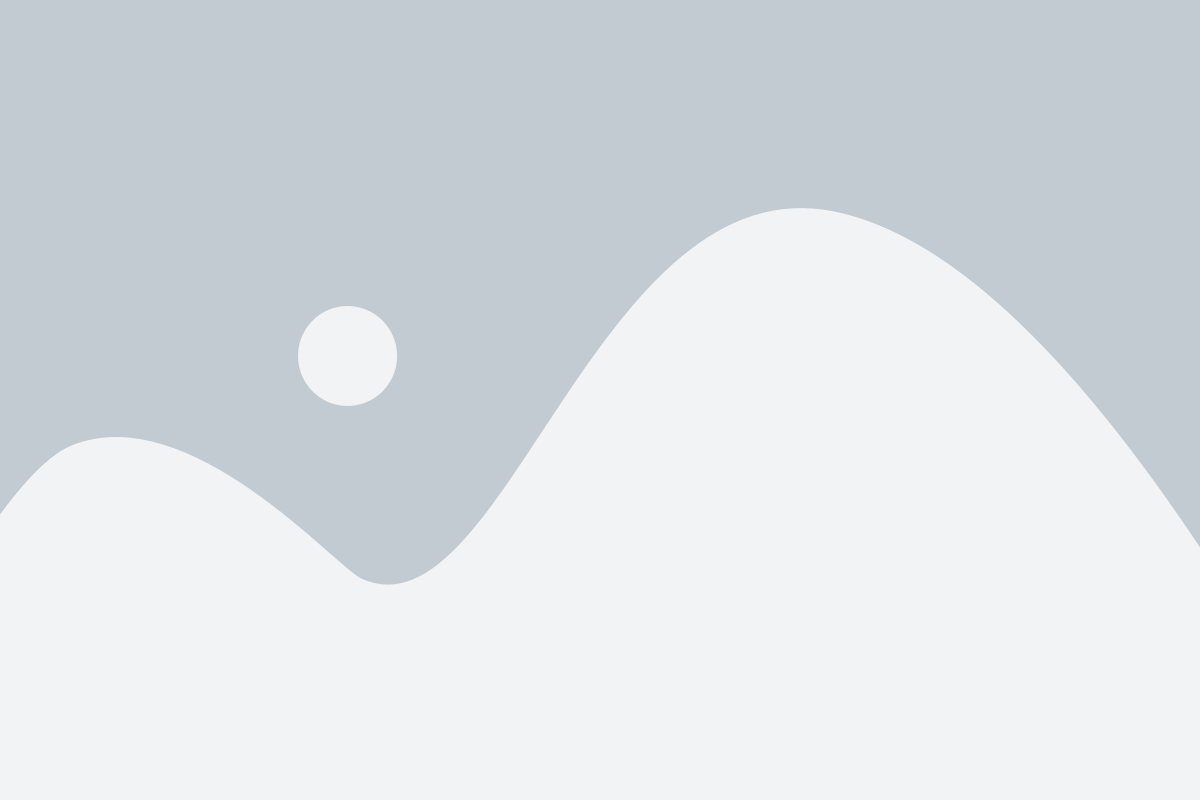
Clean Prepared Surface
Remove all grease, oil, rust, and other contaminants from the weld area using appropriate cleaning methods such as degreasing, wire brushing, or grinding. Ensure that the surface is dry and free from any residue before starting the welding process.
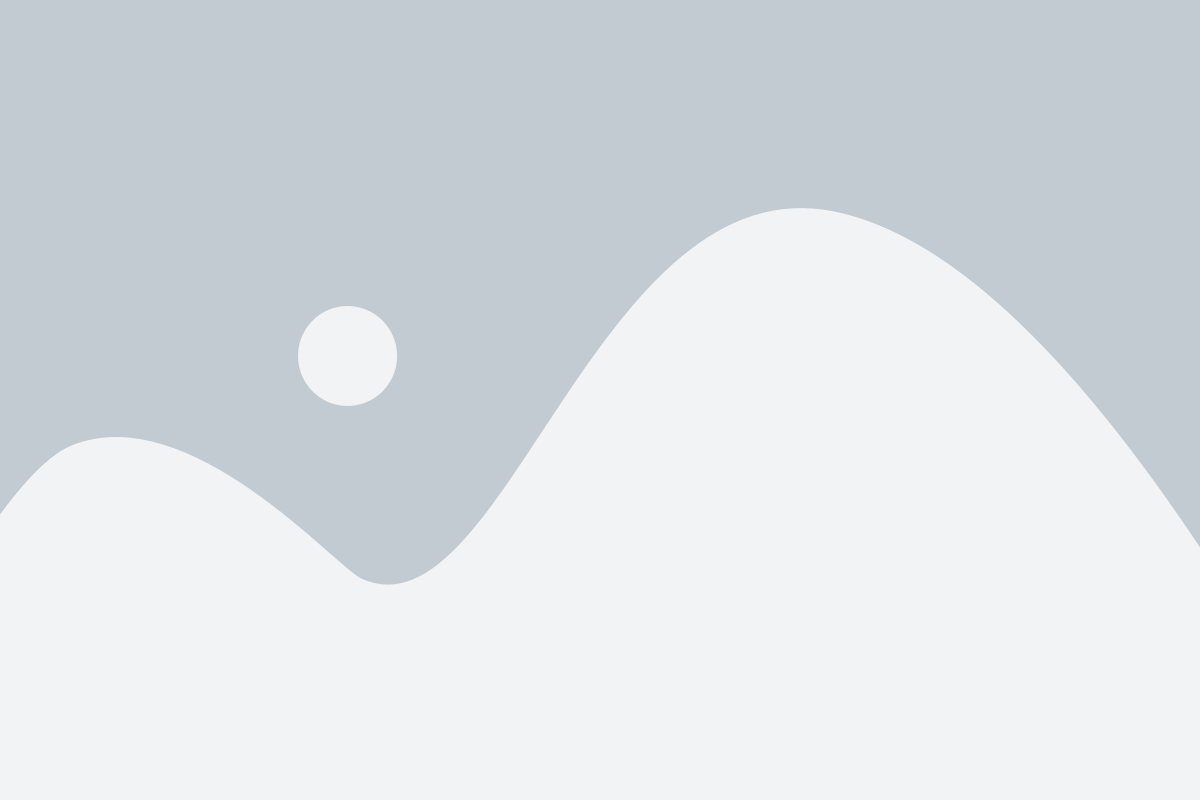
Delaminated Base Metal
Ensure the base metal is free from laminations that can trap gases. Use appropriate NDT such straight beam UT to check for laminations inside the base metal before the commencement of welding. If laminations or other internal defects are detected, replace the affected base metal with a sound piece before welding.
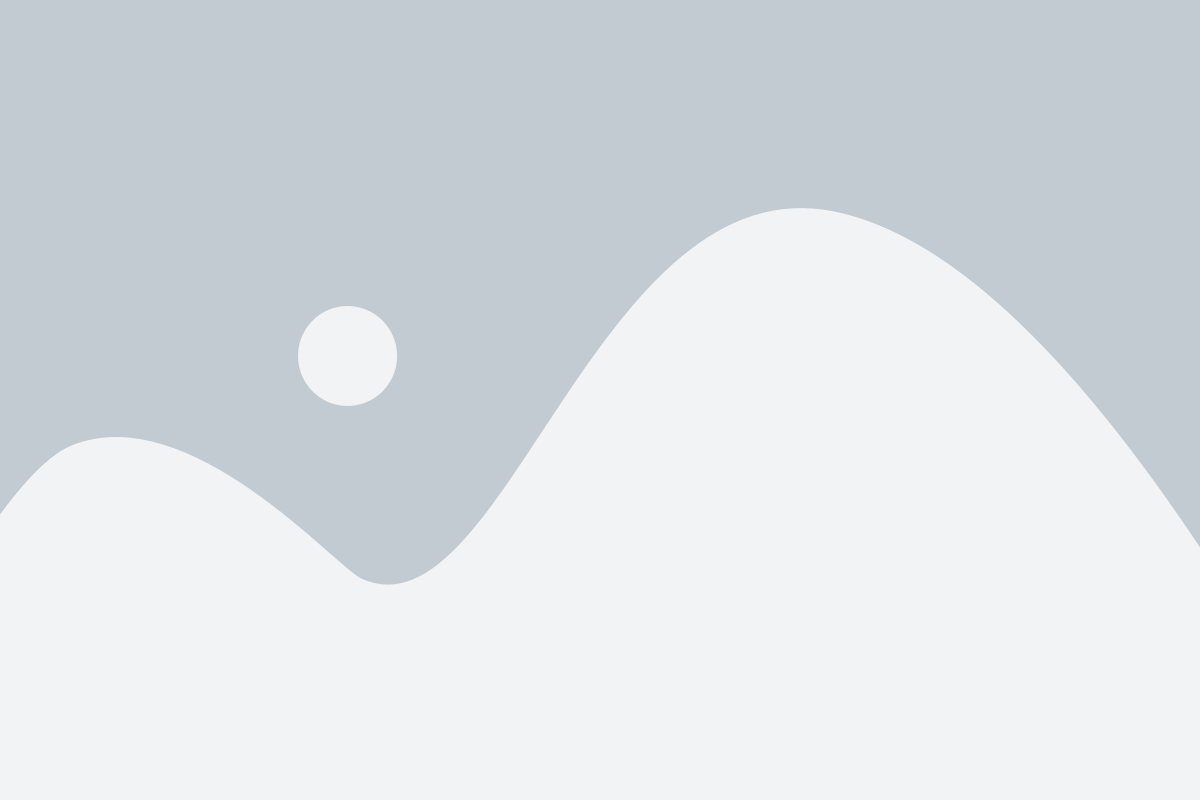
Good Joint Geometry
Modify joint preparation methods to smooth out any irregularities or crevices. Ensure precise alignment and fit-up of the joint components to eliminate gaps where gases could accumulate.
7) Crater pipe
A crater pipe is a shrinkage cavity caused due to the rapid solidification of the weld pool at the end of a weld run. It is commonly located in the weld termination area and is a result of rapid solidification and shrinkage during the cooling process.
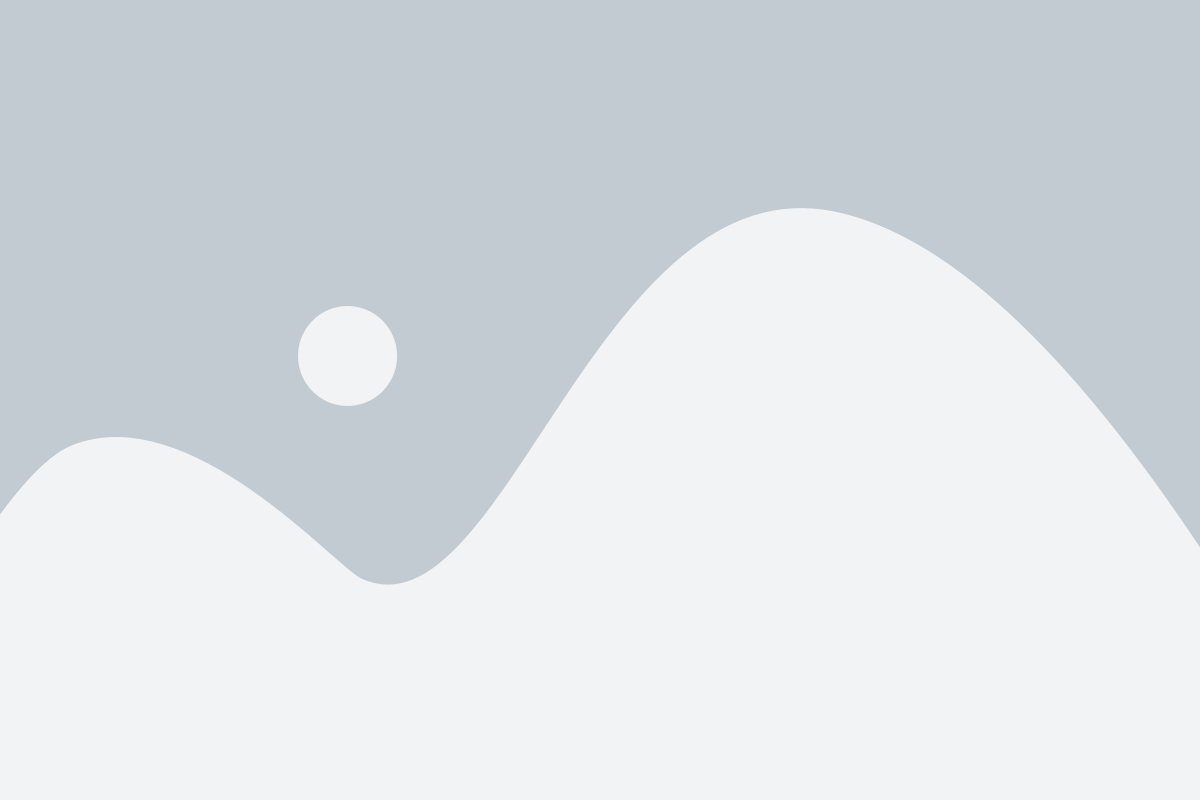
Causes for Crater Pipe
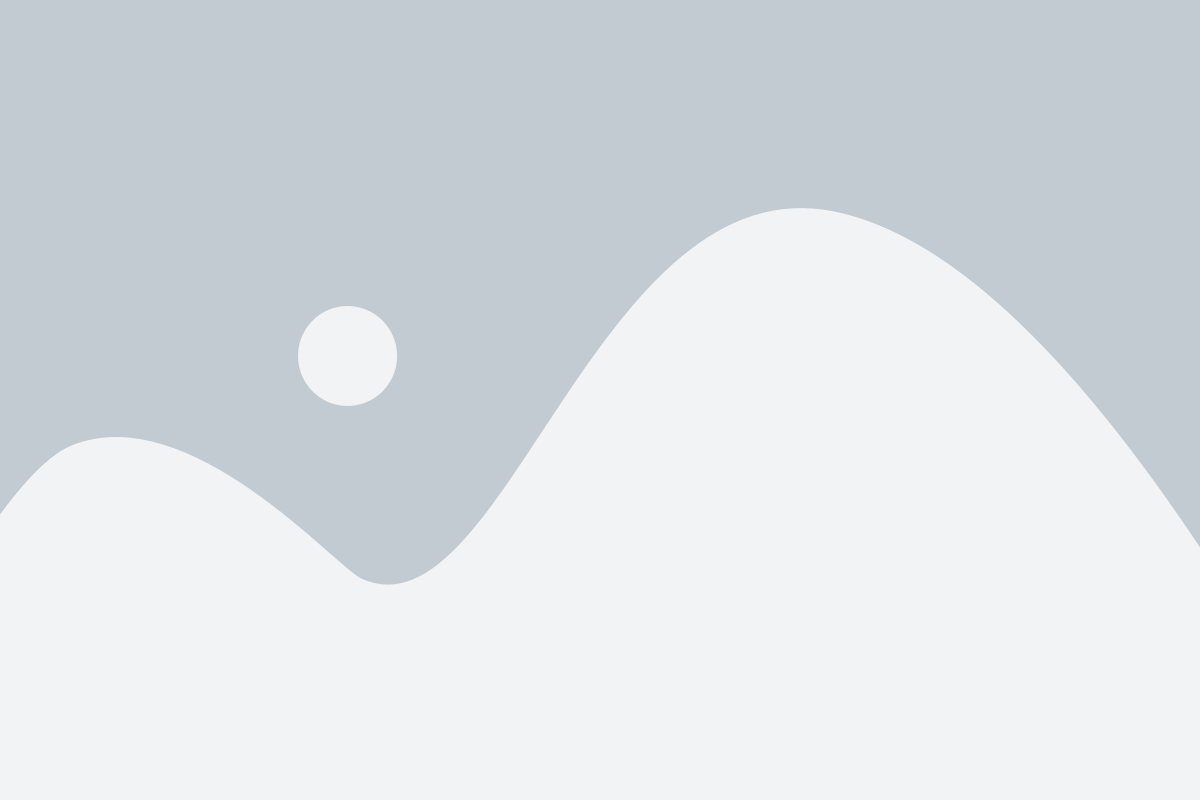
Low Welder Skill
Inexperienced welders may cause rapid solidification by providing insufficient heat input such as low current or high travel speed.
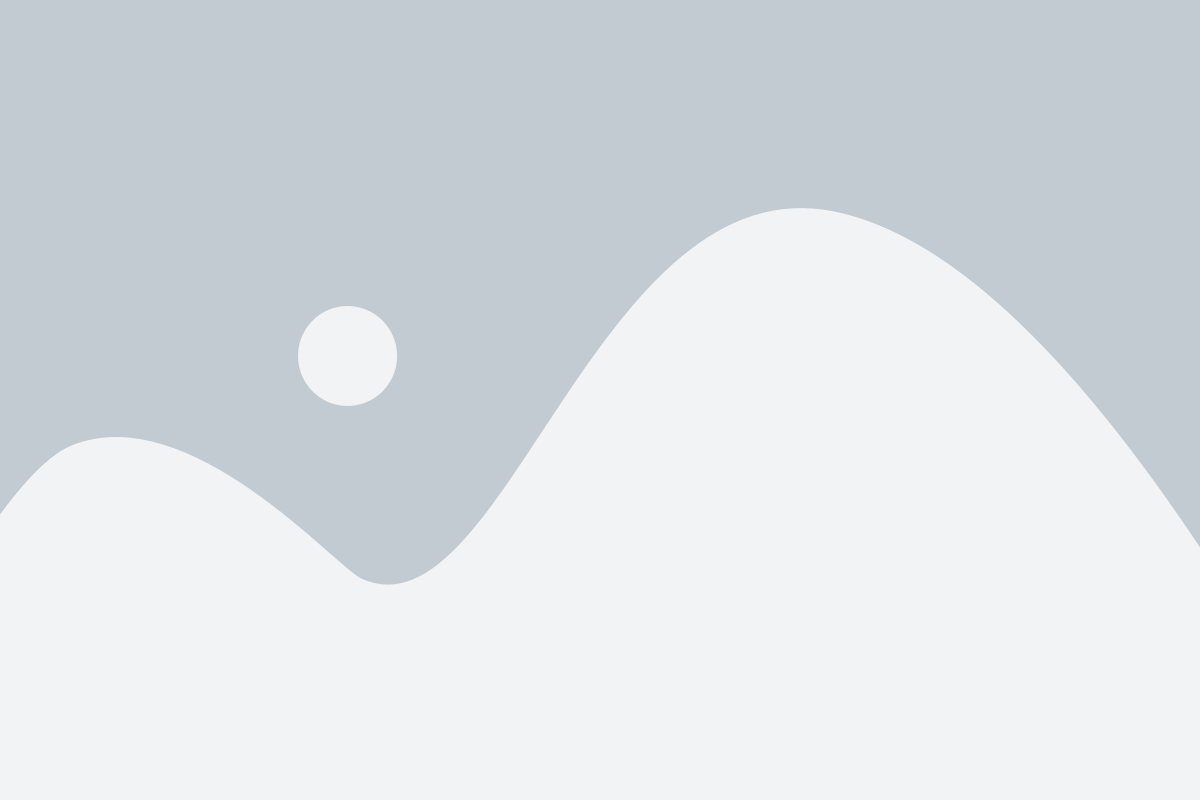
Inoperative Crater Filler & Slope Out in GTAW
If the slope-out feature fails, the weld pool solidifies too quickly, causing crater pipes. Misuse or misunderstanding of crater filler can leave insufficient material to prevent shrinkage cavities.
Prevention against Crater Pipe
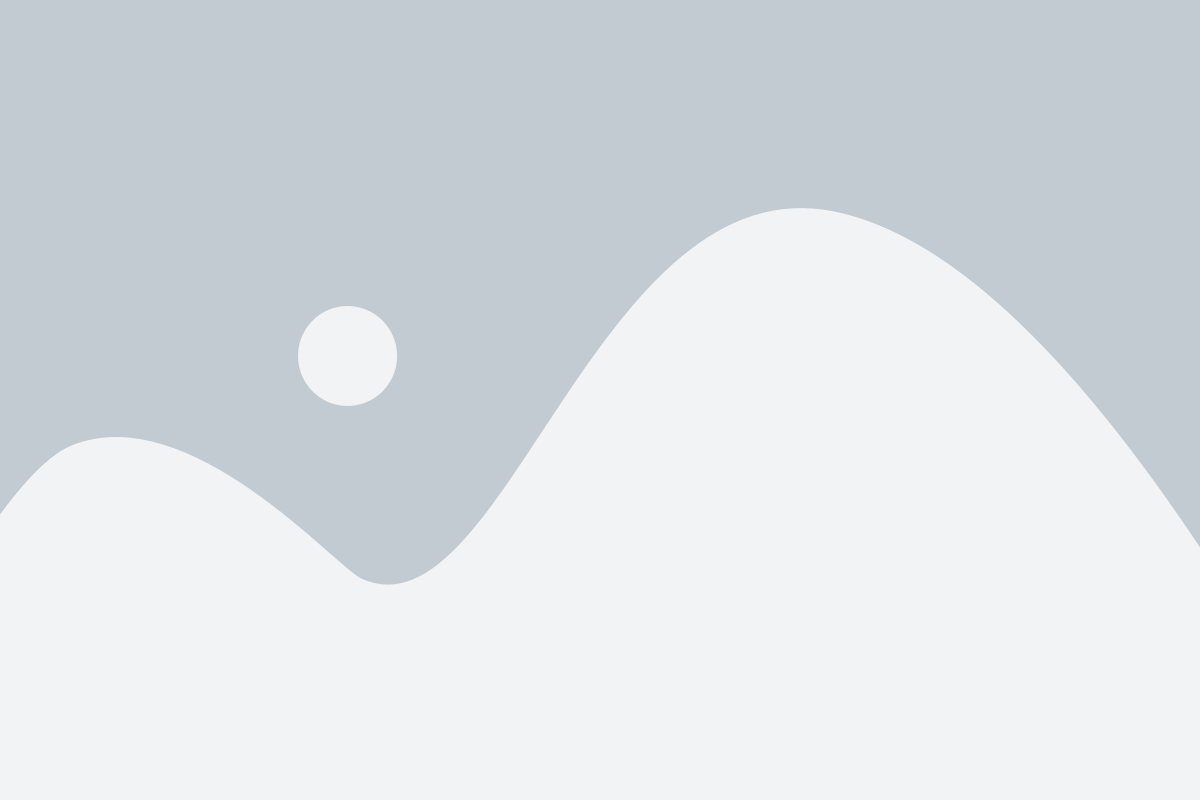
Retrain Welder
Provide targeted training programs to emphasize the importance of maintaining adequate heat input during welding. Focus on techniques for controlling arc length and heat distribution, ensuring welders can effectively manage the weld pool, particularly at termination points.
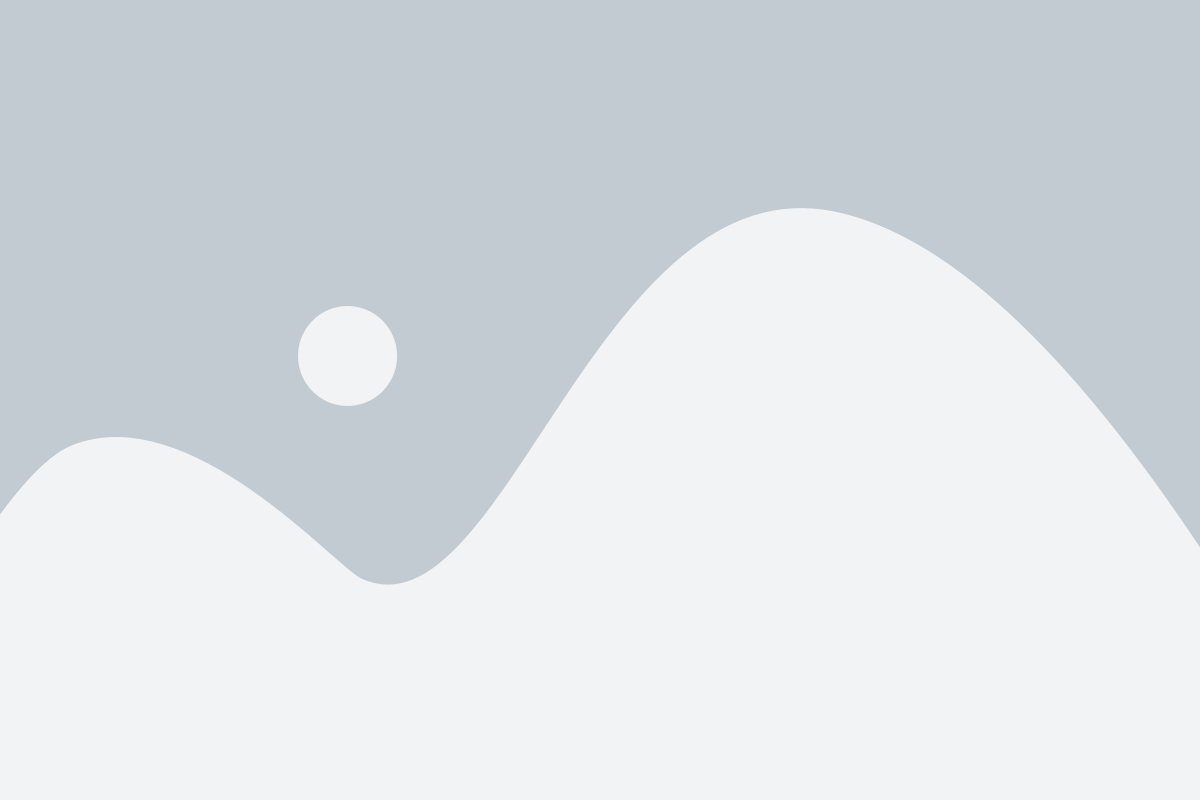
Correct Crater Filling Techniques
Educate welders on utilizing the slope-out function to gradually reduce welding current at the end of a weld. This technique allows for controlled solidification, minimizing the risk of crater formation. Also, stress the importance of adding filler material to adequately fill the crater and compensate for shrinkage.