Introduction to Underfill
Understanding Value of Strength
Welcome to our comprehensive guide on welding imperfections! Today, let’s explore the concept of underfill. In welding, underfill is a groove weld condition when the weld face or root surface is below the adjacent surface of the base metal. This can weaken the weld joint, compromising its integrity and structural strength.
Understanding underfill is crucial for welding professionals to ensure quality and safety in welded components. We’ll delve into its causes, detection methods, and preventive measures in our upcoming posts. Stay tuned to master the art of identifying and addressing underfill for impeccable welds!
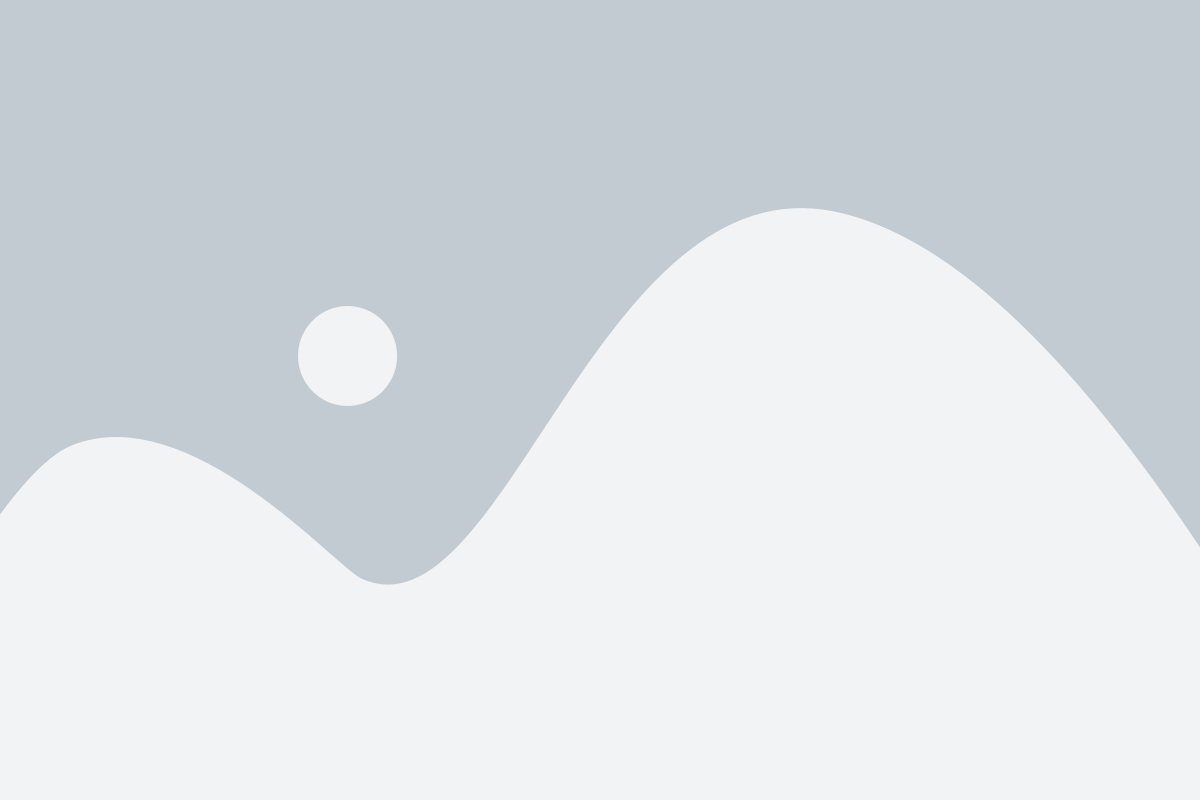
Types of Underfill
Exploring Welding Inferiority
1) Underfill at the Face Side
Underfill at the face side refers to a groove weld condition where the weld face, which is the exposed surface of the weld bead, is not level with the surface of the base metal surrounding the weld. In simpler terms, it means that the weld bead doesn’t fill the groove completely, leaving a depression or recess in the weld’s outer surface.
Underfill at the face side is a concern because it compromises the appearance, strength, and integrity of the weld joint. It creates a stress concentration point and reduces the effective cross-sectional area of the weld, making it susceptible to cracking, fatigue failure, and other defects.
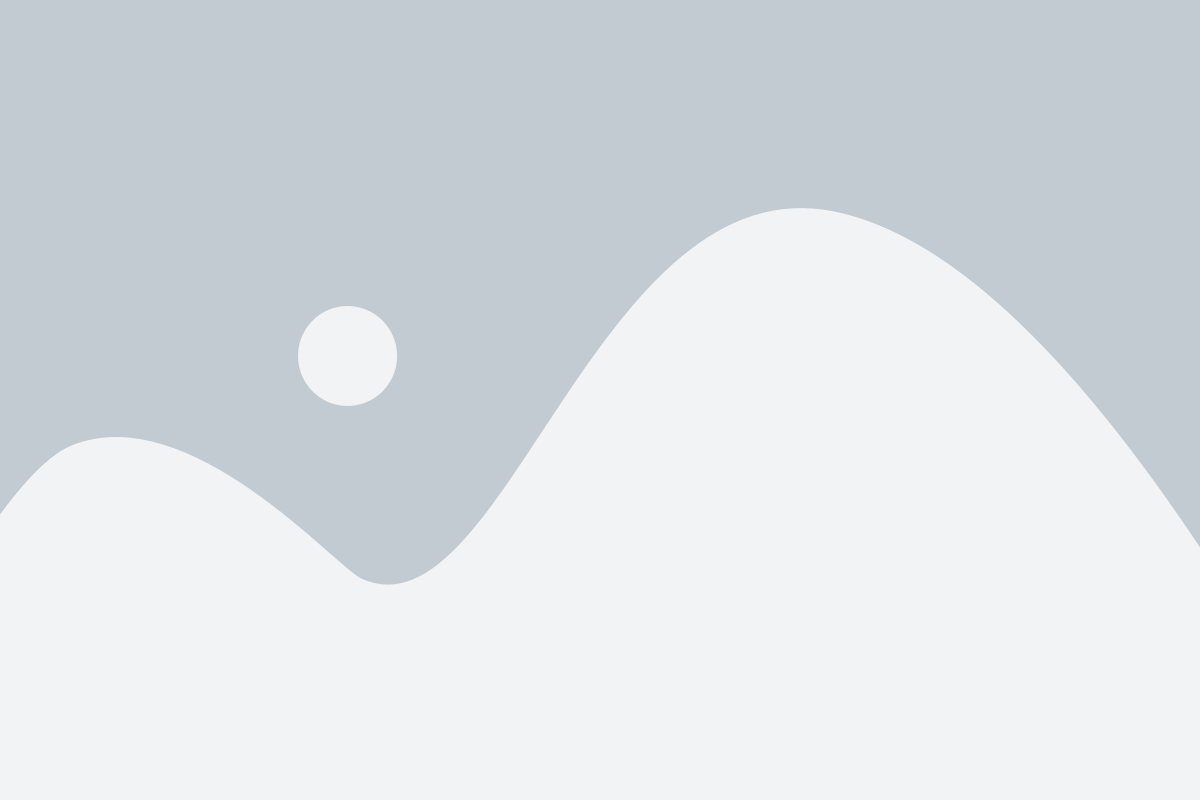
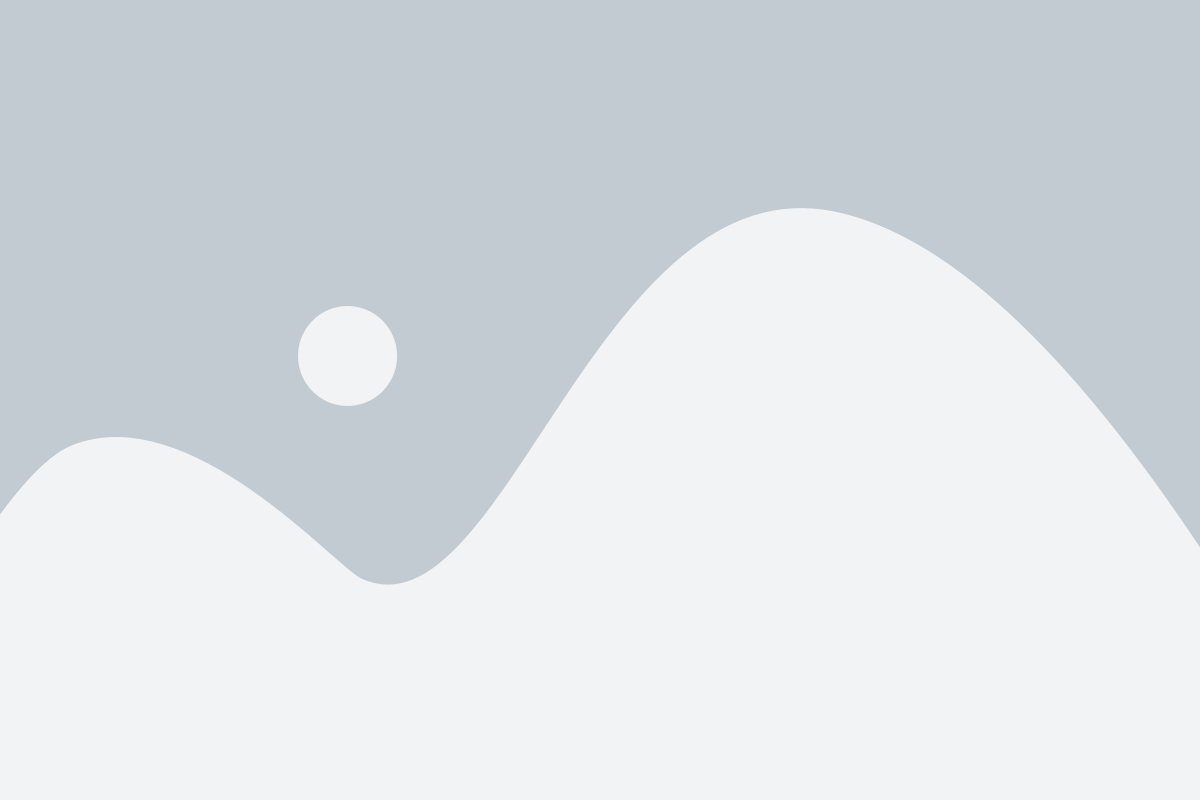
2) Underfill at the Root Side
Underfill at the root side refers to a groove weld condition where the root surface of the weld, which is the portion nearest to the root of the joint, is below the level of the adjacent base metal surface. This occurs when the weld penetration is insufficient to completely fill the groove or when the root reinforcement is inadequate.
Unlike underfill at the face side, which affects the outer appearance of the weld, underfill at the root side poses a more critical concern because it directly impacts the strength and integrity of the weld joint.
Key Factors (Causes)
Impact of Improper Welding Techniques
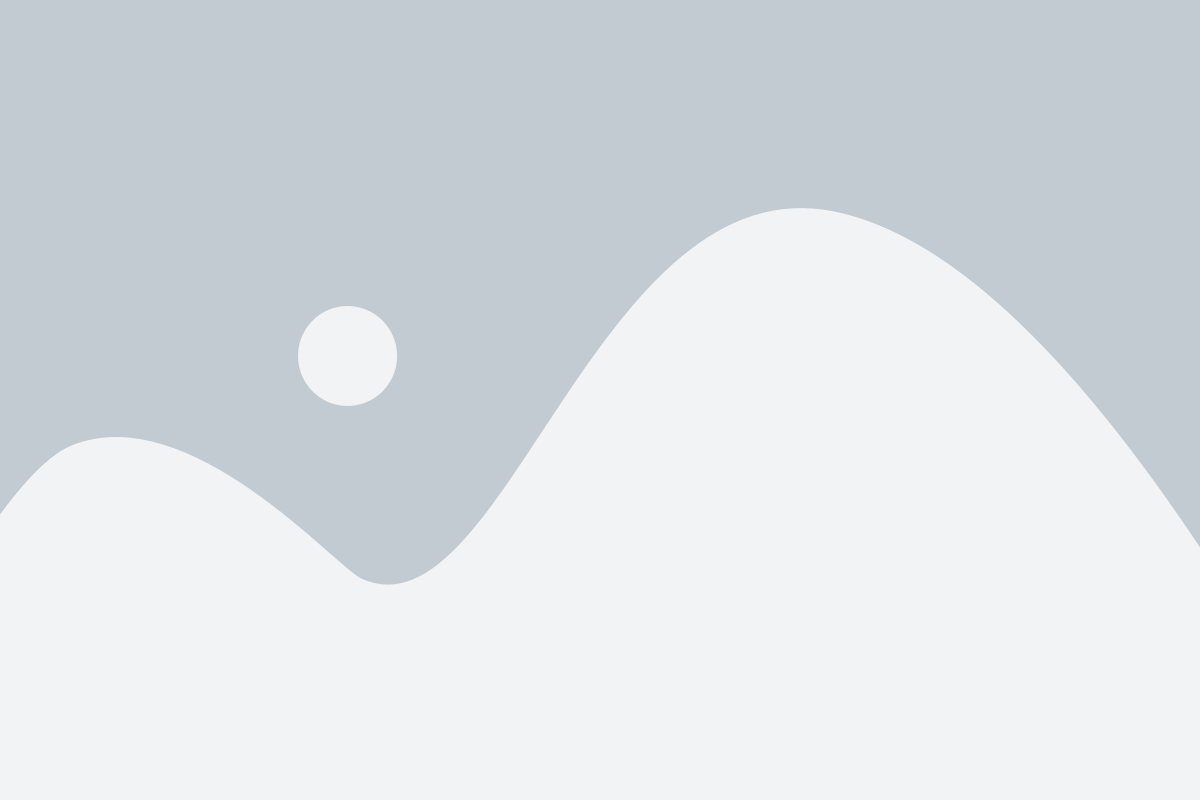
Low Current
When the welding current is set too low, there is insufficient heat input into the weld pool. As a result, the weld metal may not reach the required temperature for proper fusion with the base metal, leading to underfill. The insufficient heat generated by low welding current can result in a narrow and shallow weld bead that fails to adequately fill the groove.
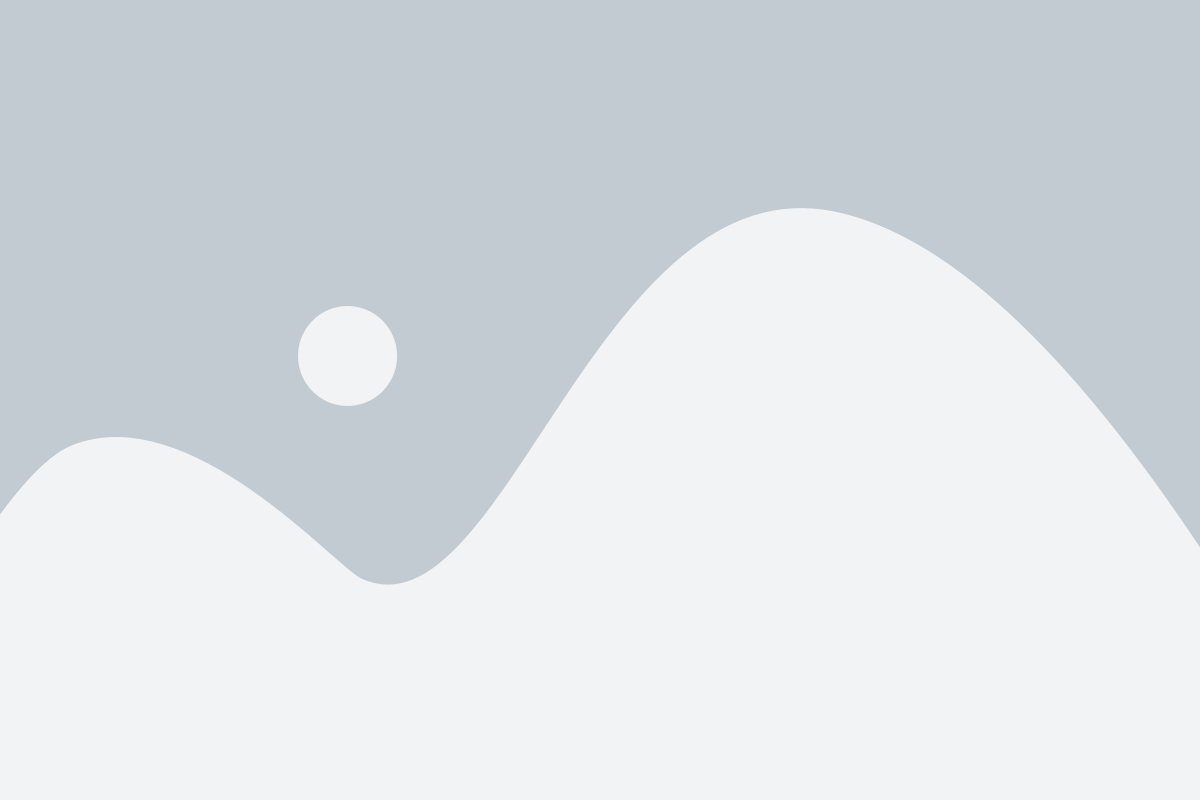
Low Filler Metal Feed Rate
The feed rate at which filler metal is supplied into the weld pool directly affects the size and shape of the weld bead. When the filler metal feed rate is too low, there may not be enough material available to fill the groove adequately, resulting in underfill. Insufficient filler metal deposition can lead to a concave or recessed weld bead profile, indicating underfill at the face side of the groove weld.
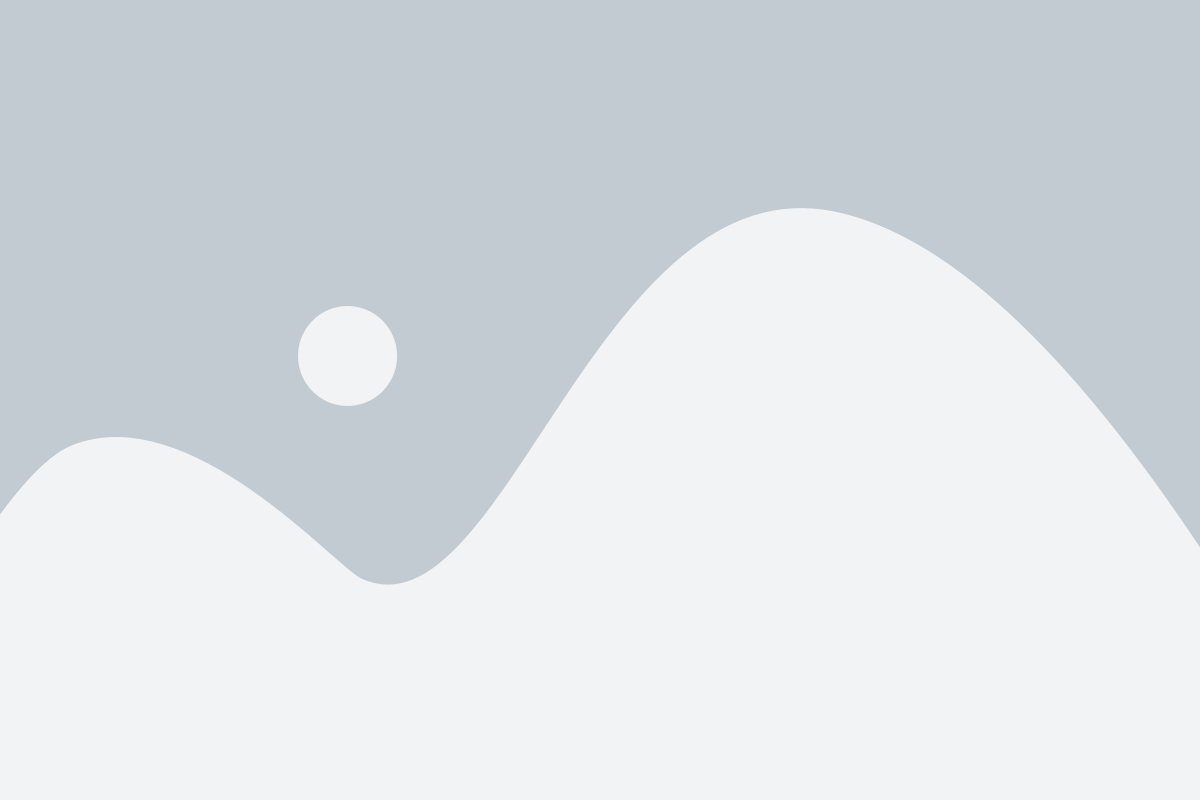
High Travel Speed
Travel speed directly impacts the time available for heat transfer and weld pool formation. When the travel speed is too high, the weld pool may not have sufficient time to fully penetrate and fuse with the base metal, resulting in underfill. High travel speed can cause the weld pool to become elongated and shallow, leading to incomplete fusion and inadequate groove fill.
Prevention
Welder Responsibilities
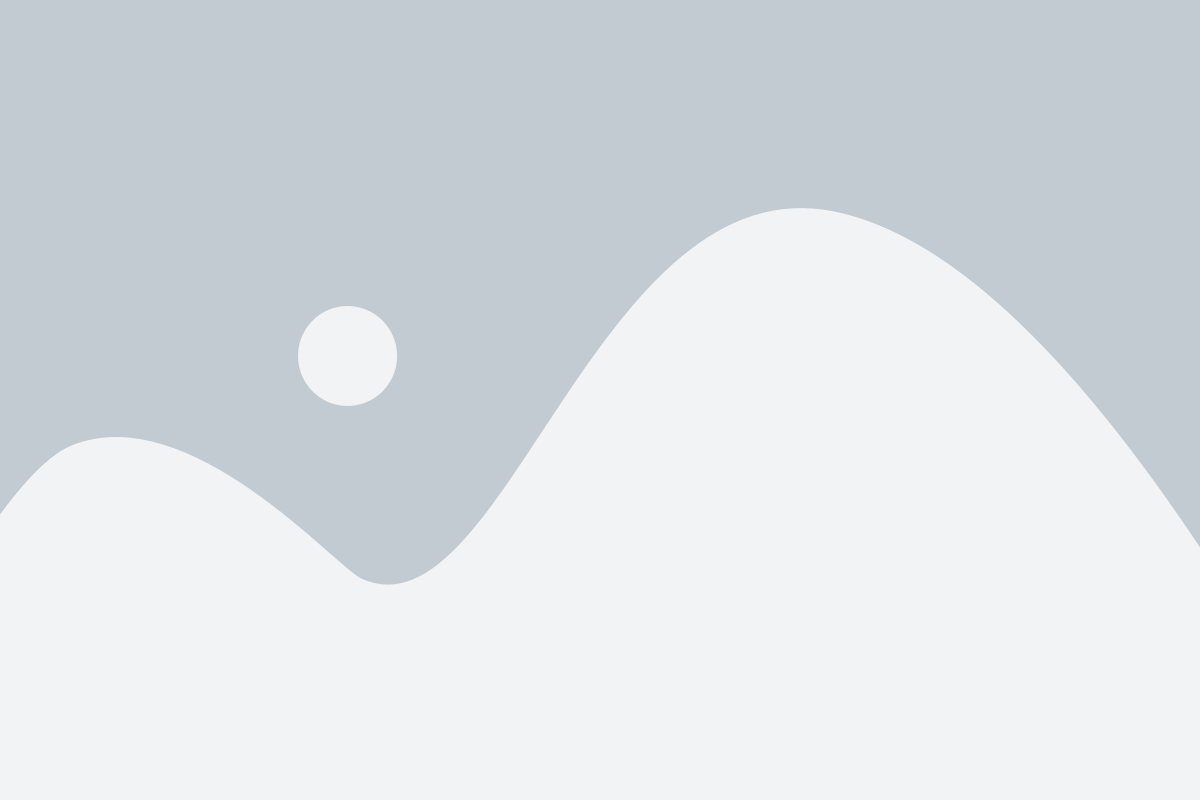
Welder Skill
Preventing underfill at the face side primarily relies on welder skill. Proper training ensures welders understand welding techniques and parameters to achieve complete groove fill. Additionally, welders should continuously monitor and adjust welding parameters during the process to prevent underfill. Regular training and practice enhance welder proficiency, minimizing the risk of underfill and ensuring weld quality.
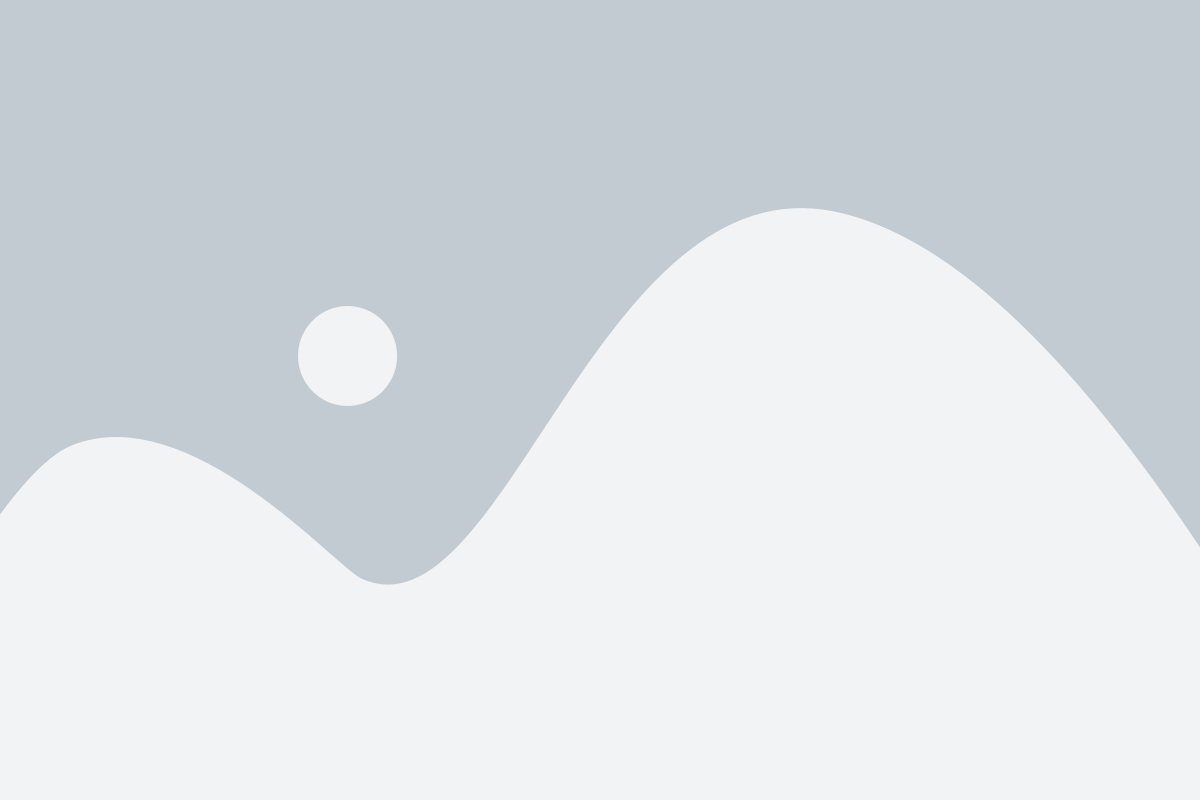
Optimize Current
To address underfill caused by low current, ensure that the welding machine is set to the appropriate current level based on factors such as material thickness, joint configuration, and electrode size. Increasing the welding current within the recommended range can provide greater heat input, promoting proper fusion and ensuring complete groove fill.
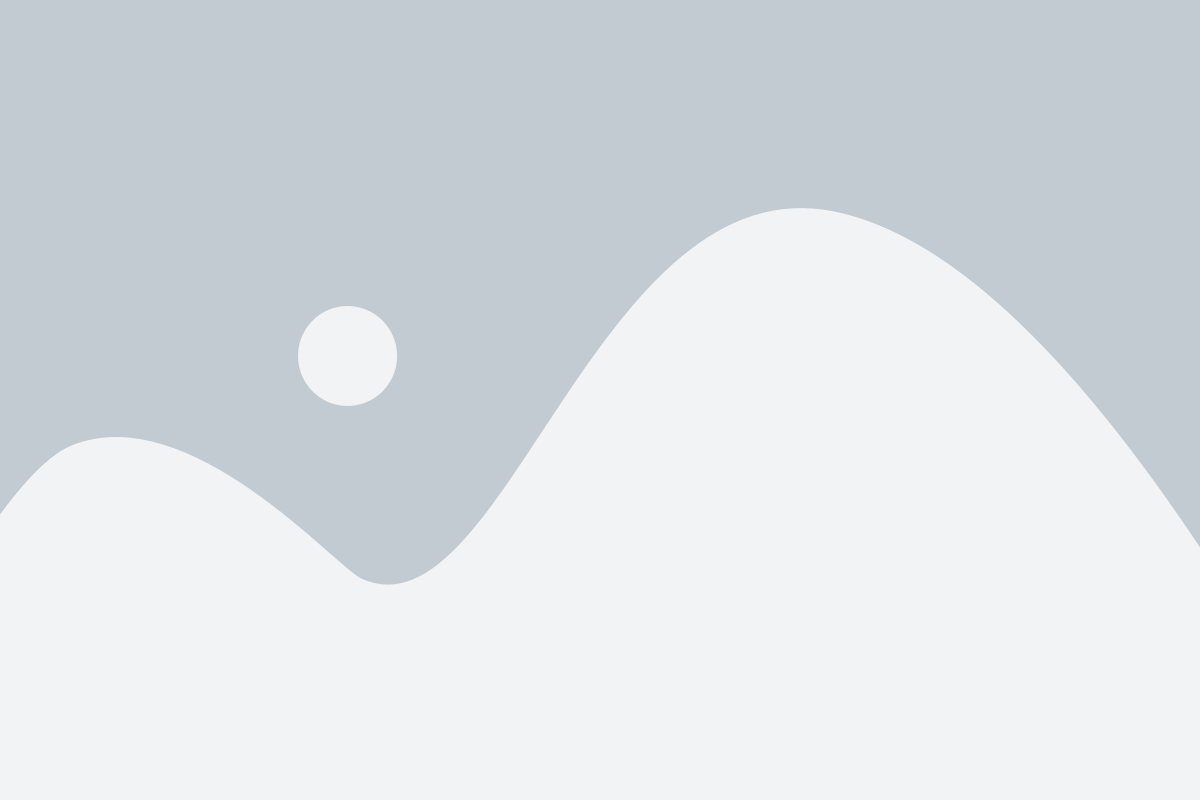
Optimize Filler Metal Feed Rate
To mitigate underfill caused by low filler metal feed rate, feed rate should be adjusted & optimized to ensure consistent and adequate deposition throughout the welding process. Increasing the filler metal feed rate or adjusting the welding speed can help maintain proper weld bead shape and ensure complete groove fill.
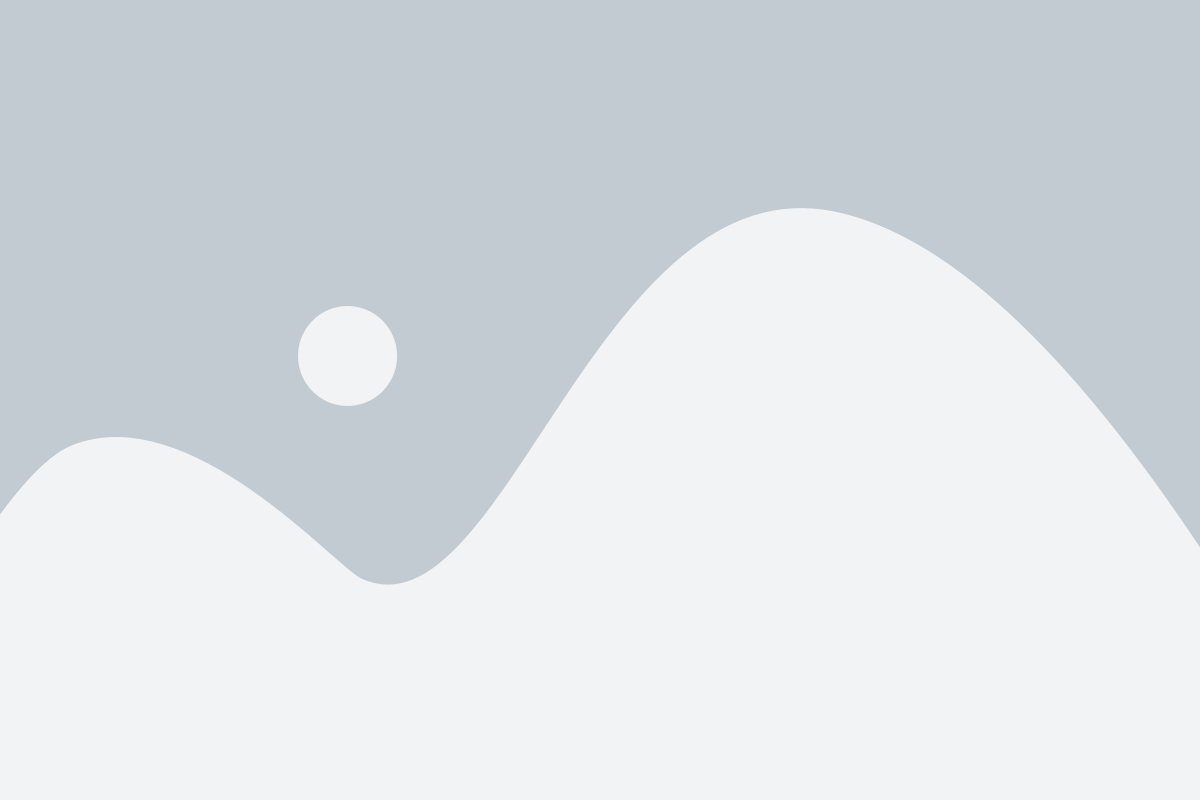
High Travel Speed
To address underfill caused by high travel speed, slow down the welding travel speed to allow sufficient heat input and adequate fusion. Adjusting the welding parameters, such as travel speed and arc length, to maintain a stable weld pool, which can help prevent underfill.