Mastering Welding Positions
Fundamentals & Advancements in Welding Techniques
Cultivating mastery in welding starts with understanding welding positions. These positions dictate how a welder approaches their work, ensuring precision and strength in every joint. From the foundational flat position to the challenging overhead stance, each demands unique techniques and skills.
Beginners grasp the fundamentals in flat and horizontal positions, gradually advancing to vertical and overhead as proficiency grows. Mastery extends to specialized positions like vertical-up, vertical-down, and overhead positions, essential for diverse welding projects. Dive into this essential aspect of welding to unlock your potential and sculpt a future in metal mastery.
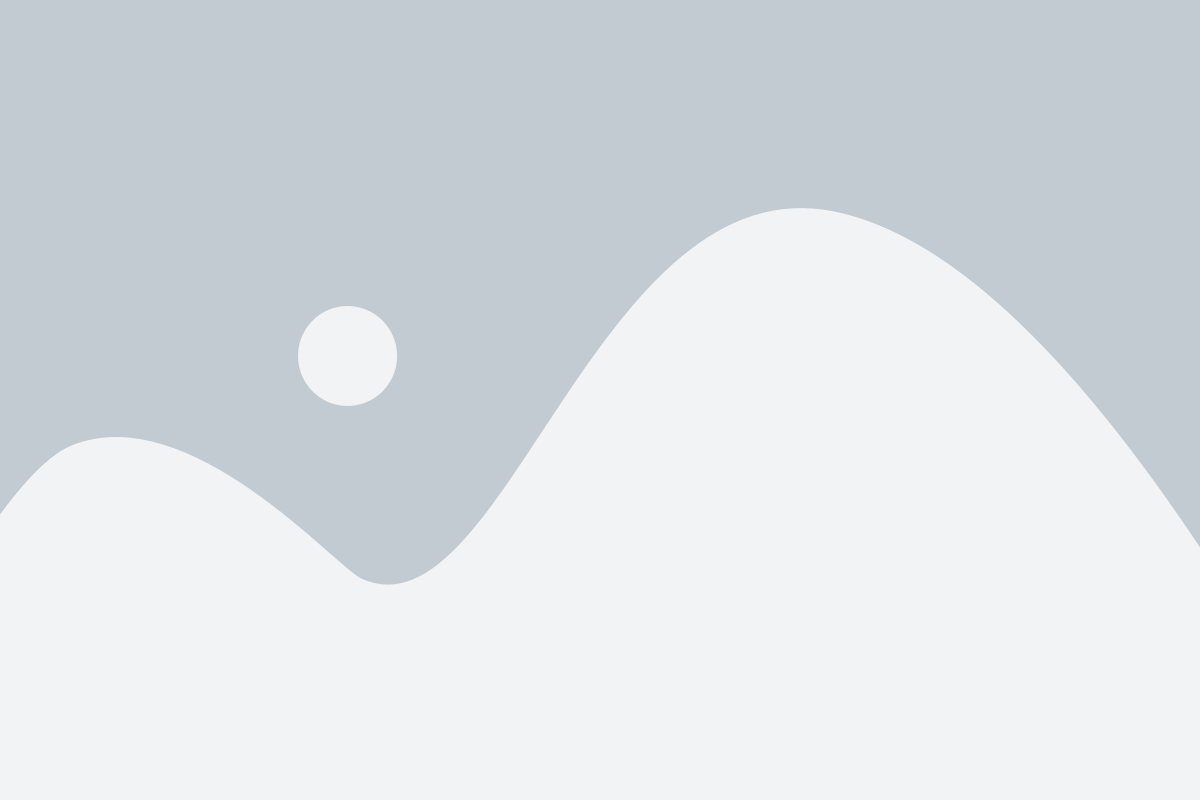
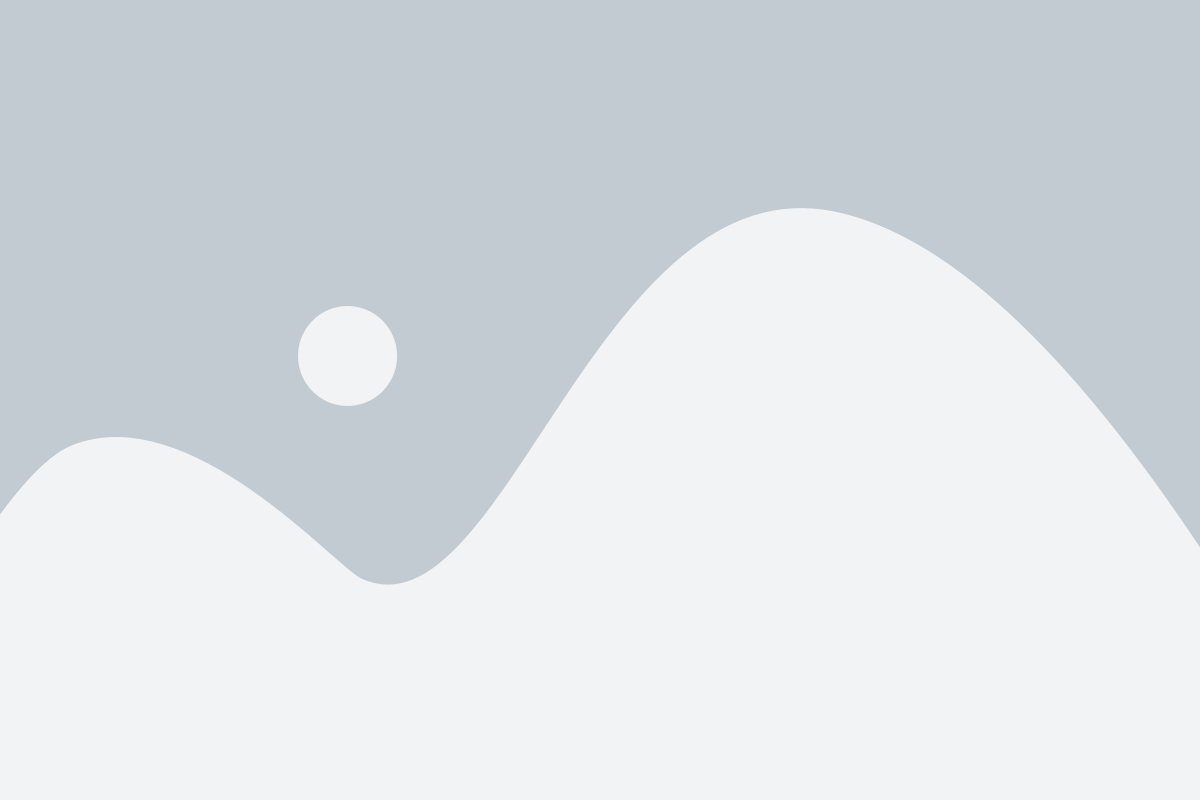
Importance of Welding Positions
Unlocking Welding Precision & Versatility
Foundation of Precision: Welding positions dictate the orientation of weld joints, ensuring accuracy and strength in metal fabrication.
Versatile Techniques: Understanding various positions like flat, horizontal, vertical, and overhead empowers welders to adapt to diverse project requirements.
Skill Advancement: Proficiency in different positions signifies a welder’s expertise, enabling them to tackle complex welding tasks with confidence.
Industry Relevance: Employers prioritize welders proficient in multiple positions, enhancing career prospects and opportunities for advancement.
Safety and Quality Assurance: Correct positioning minimizes welding defects and ensures structural integrity, promoting workplace safety and product reliability.
Global Application: Mastery of welding positions transcends borders, offering lucrative career prospects in industries worldwide.
Continuous Learning: Evolving technologies and techniques in welding positions necessitate ongoing skill development to stay competitive in the field.
Community & Collaboration: Engaging with peers and experts in welding positions fosters knowledge exchange and professional growth within the welding community.
Future Innovation: Profound understanding and application of welding positions pave the way for innovation and advancements in metalworking industries globally.
Environmental Impact: Efficient use of welding positions contributes to sustainable manufacturing practices, reducing material waste and energy consumption.
Groove Welding Positions for Plate
Challenges and Solutions
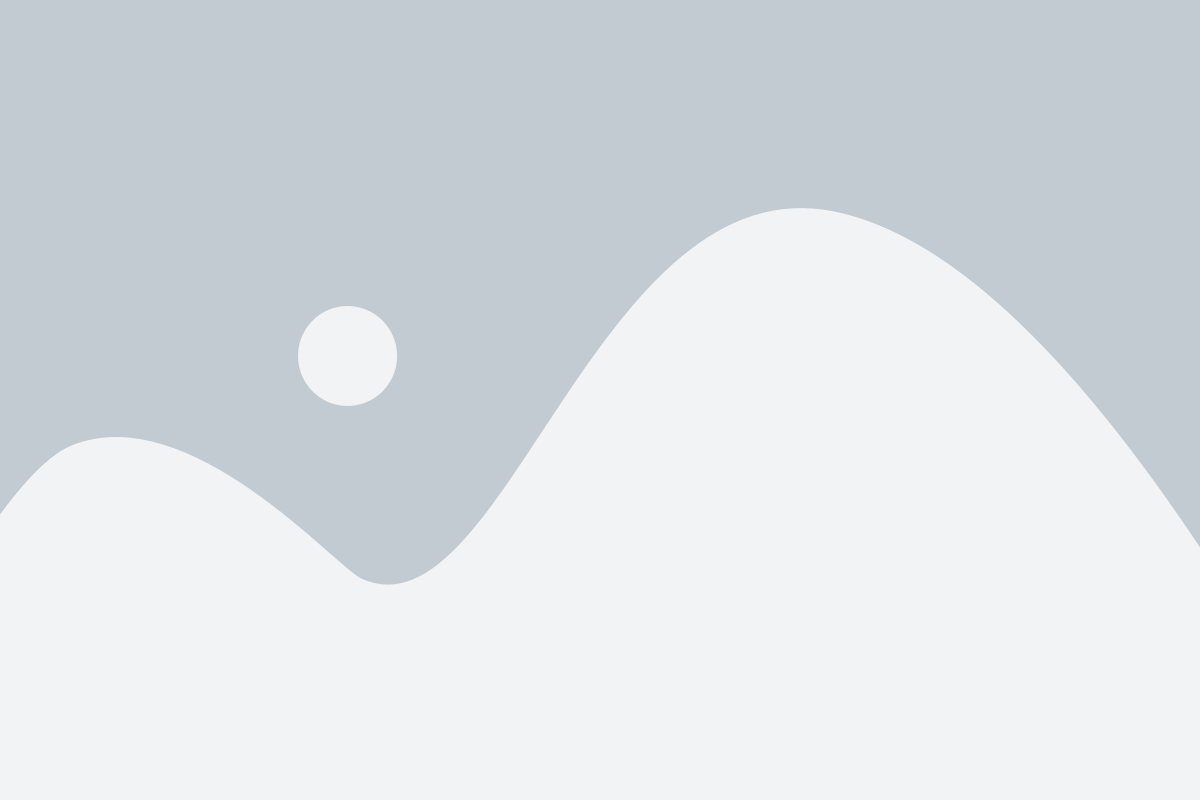
Flat Groove Welding Position (1G)
This position is often the starting point for welders. The plate lies flat, and the weld groove faces upward. It is typically used for welding joints in structures where both pieces are positioned horizontally. It is commonly used for plate welding where the welder operates from the top side of the joint.
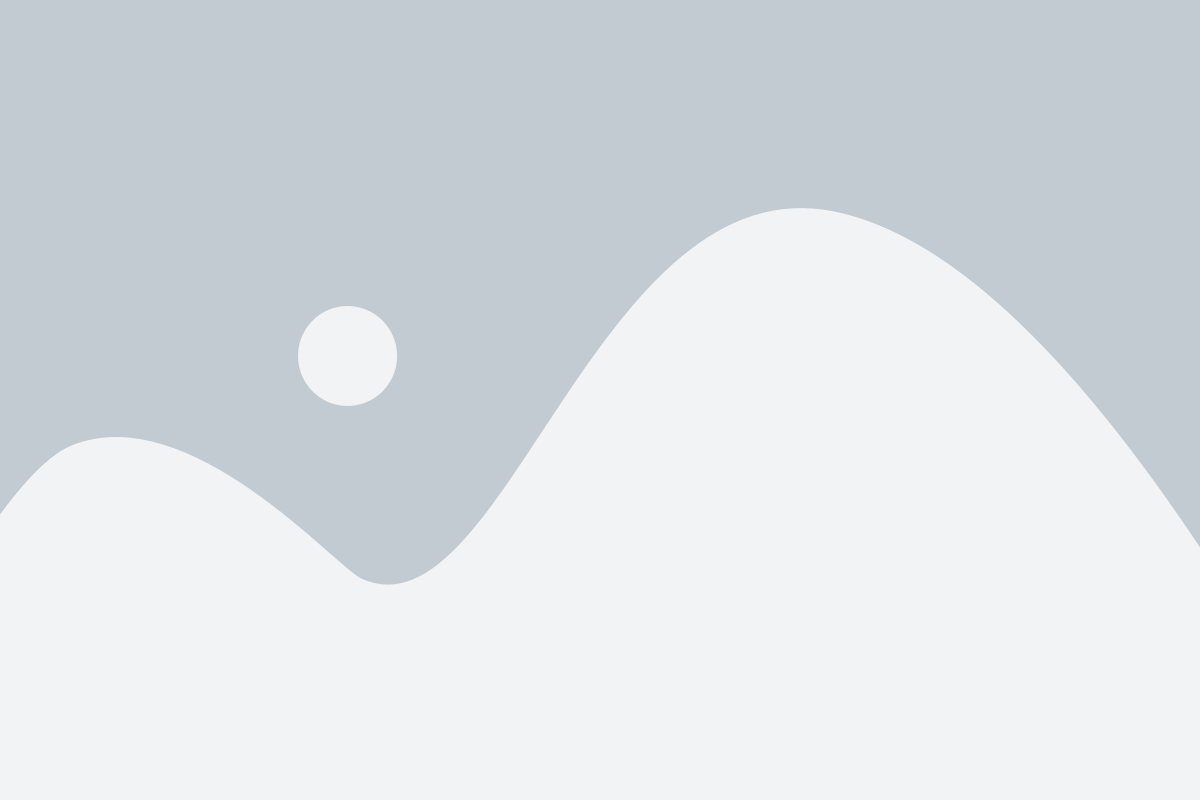
Horizontal Groove Welding Position (2G)
In the 2G position, the plate is positioned horizontally, and the weld groove is also horizontal. This position is common in shipbuilding and structural welding, where welders work from the side of the joint.
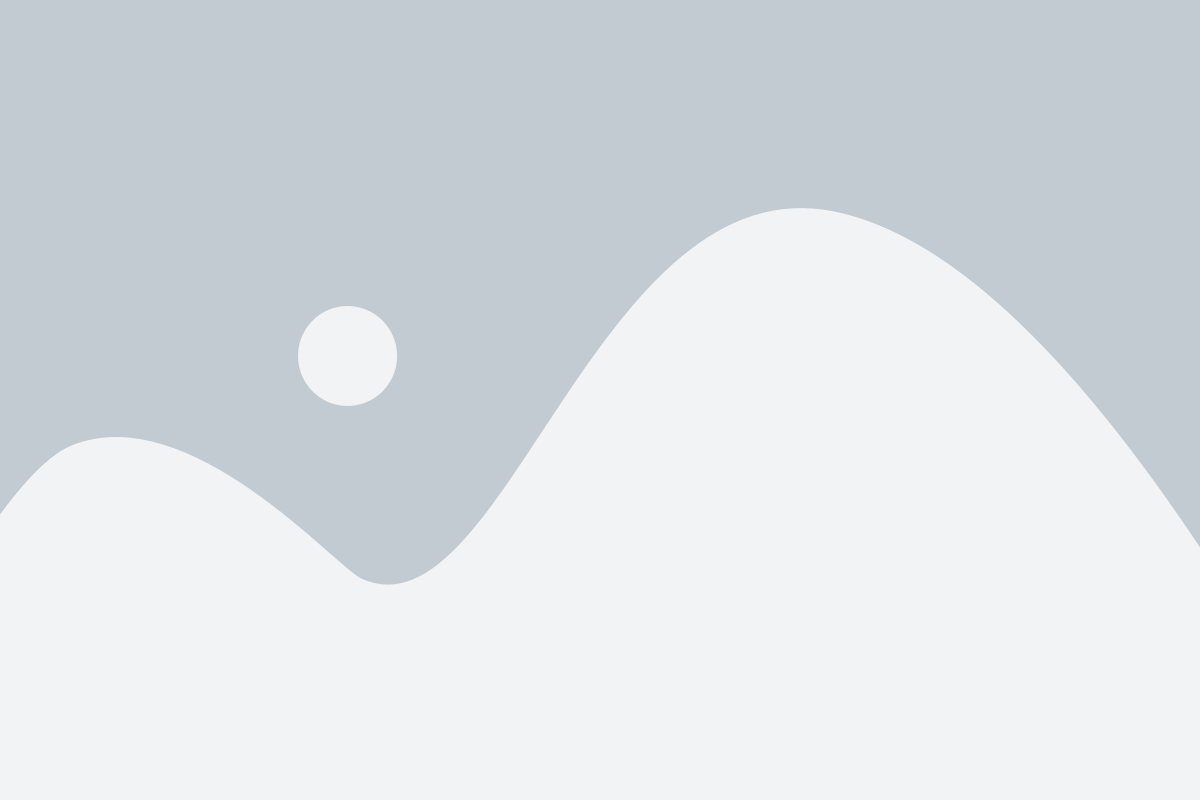
Vertical Groove Welding Position (3G)
Welding in the 3G position involves welding on a vertical surface with the groove placed vertically. It is often used in construction and bridge fabrication, requiring welders to work either from the top or bottom of the joint.
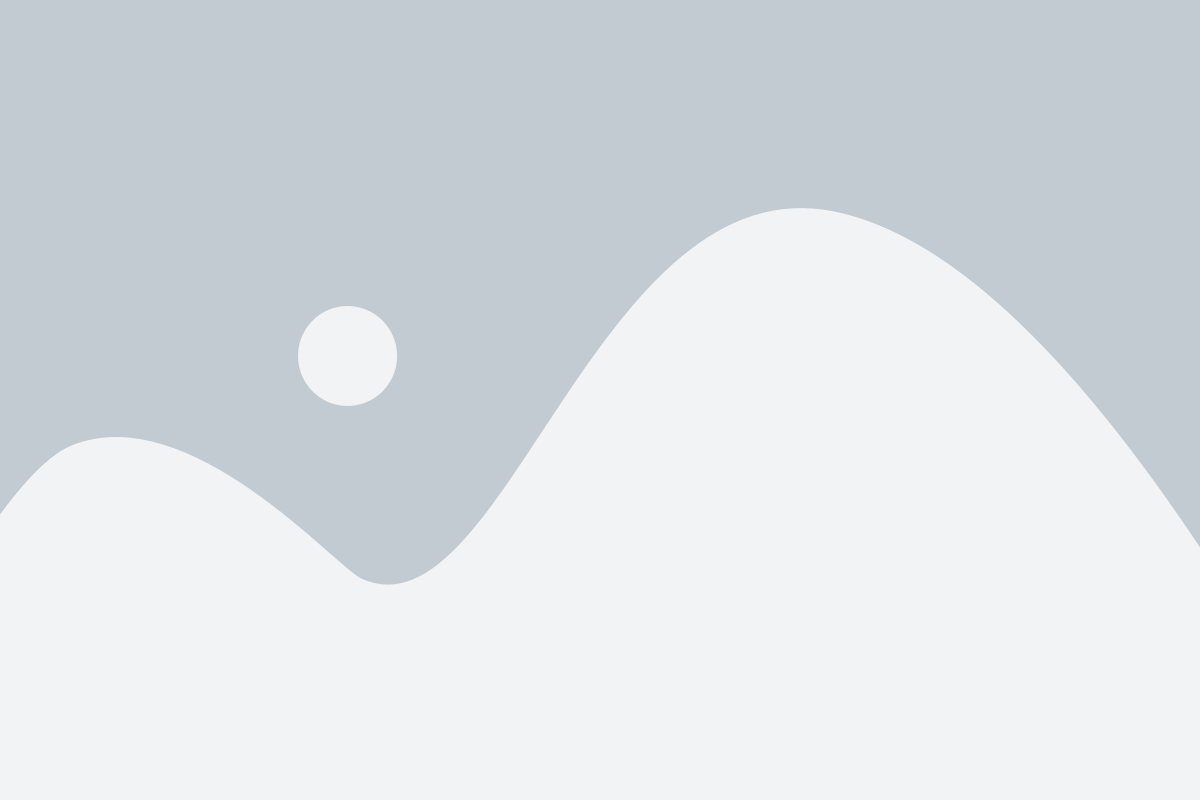
Overhead Groove Welding Position (4G)
This position involves welding on the underside of a horizontal surface, with the groove facing downward. It is challenging due to gravity's effects on the weld pool, requiring skilled technique to prevent defects.
Groove Welding Positions for Pipe
Application in Energy Industry
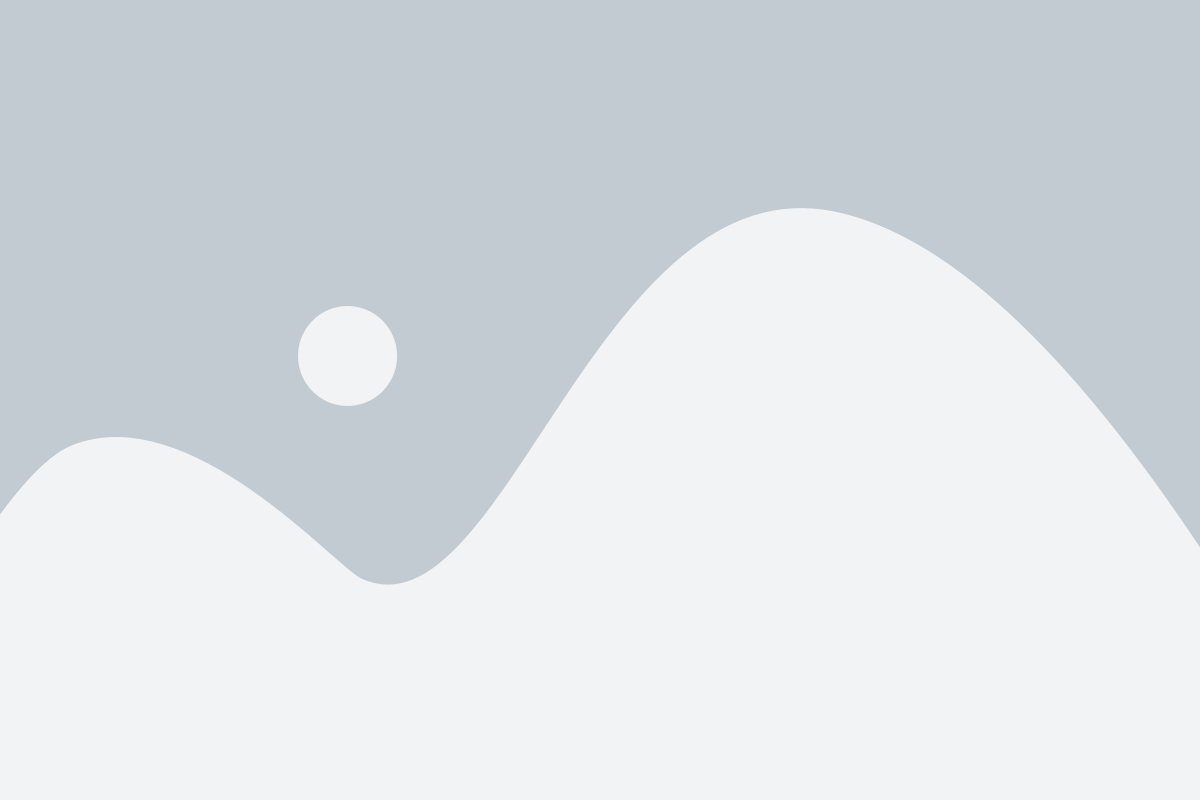
Flat Rotated Groove Welding Position (1G Rotated)
In pipe welding, the 1G Rotated position involves rotating the pipe while welding on a horizontal plane with the groove facing upward. It is commonly used in pipeline construction and fabrication. It is similar to the flat position but applied to cylindrical surfaces.
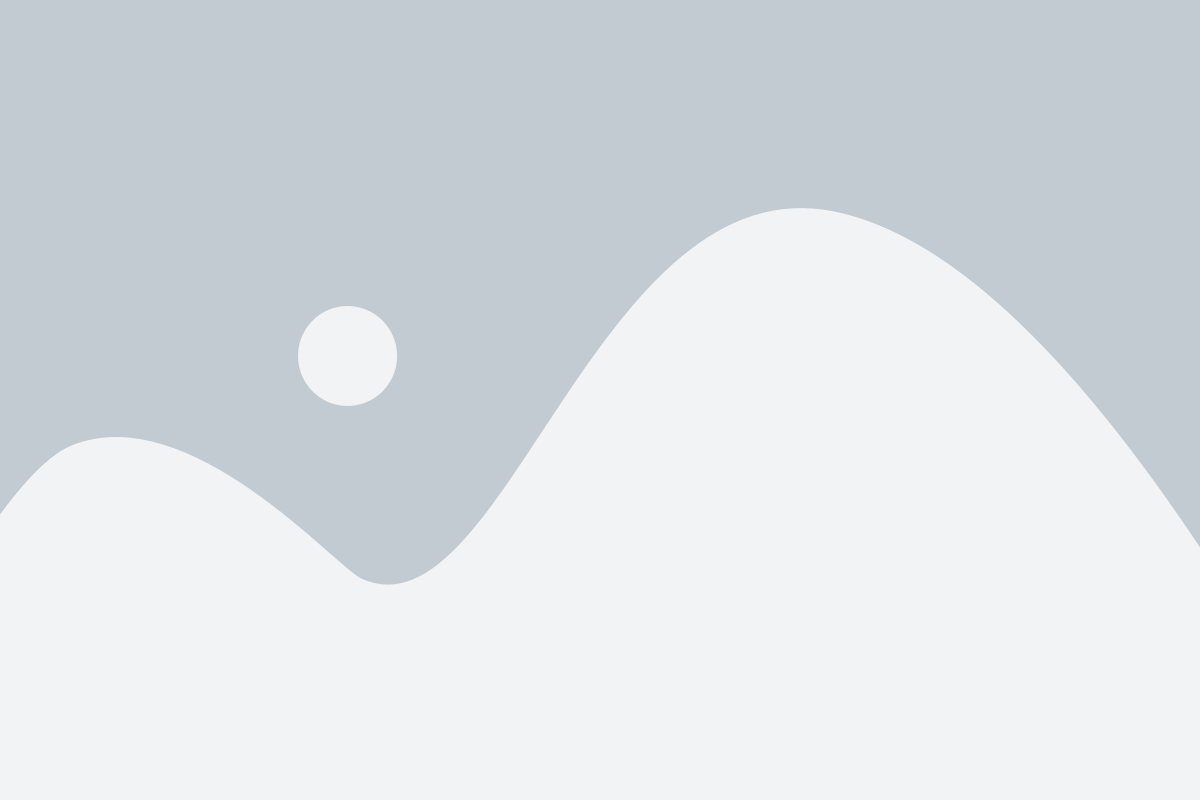
Horizontal Groove Welding Position (2G)
Welding in the 2G position on a pipe requires welding horizontally with the groove positioned horizontally. The pipe may be rotated or fixed, and welders typically work from the side of the joint.
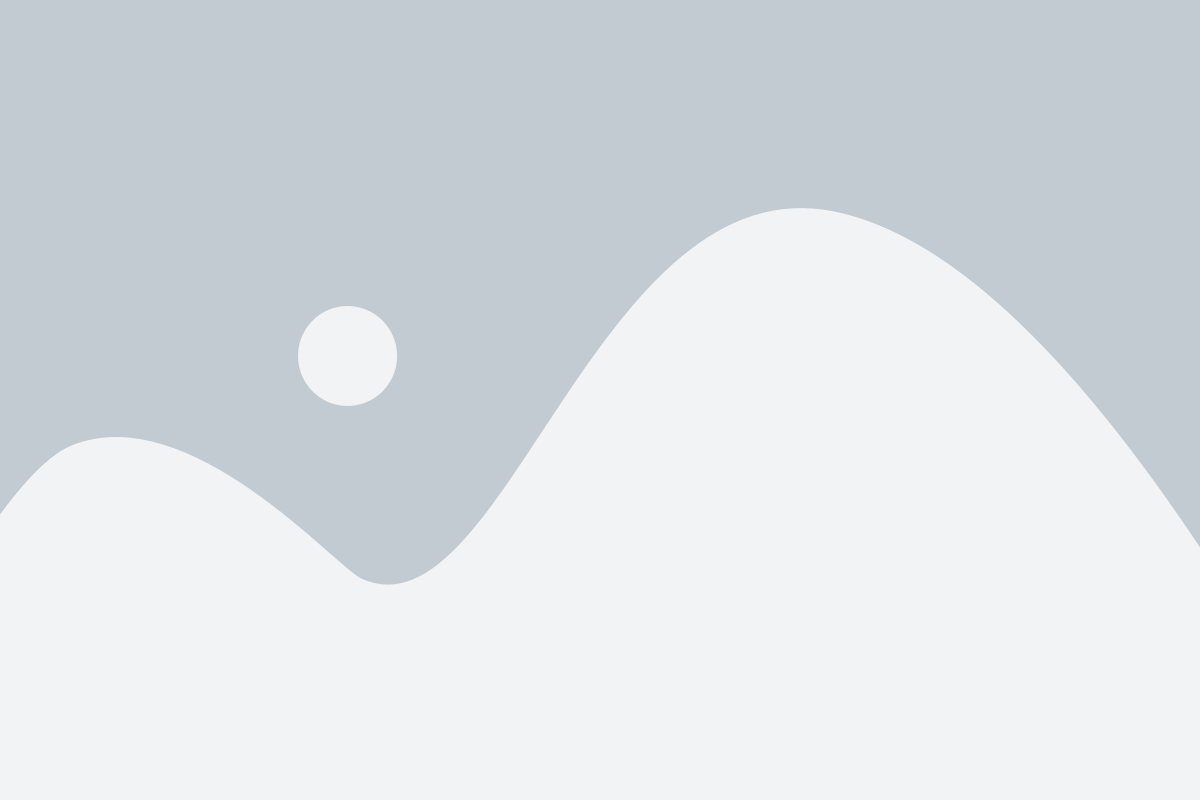
Vertical Groove Welding Position (5G)
The 5G position involves welding on a vertical pipe with the groove placed vertically. It is often used in pipeline construction and requires welders to work from multiple angles to complete the joint.
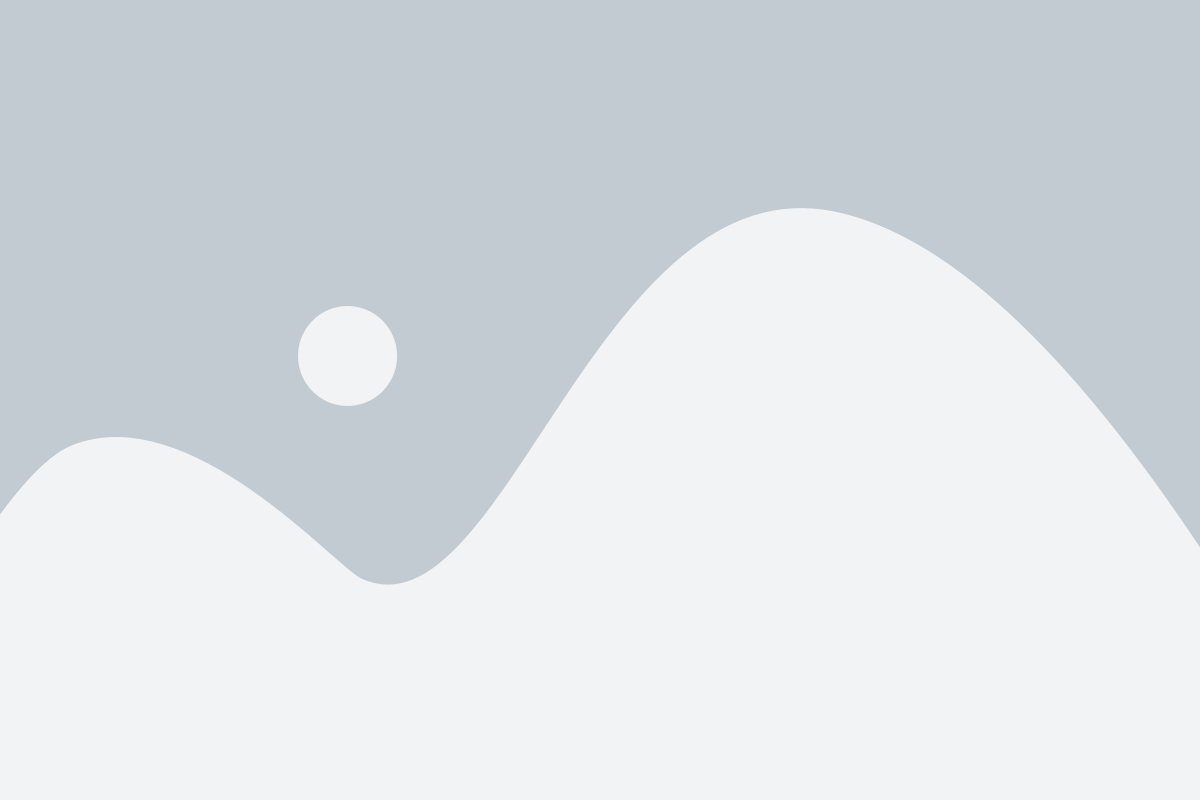
Inclined Groove Welding Position (6G)
In the 6G position, the pipe is fixed at an inclined angle, and the groove can be positioned either horizontally or vertically. This position is commonly required for welding pipes in various industries and demands high skill levels due to the complex angles involved.
Fillet Welding Positions for Plate
Utilization in Plate Welding
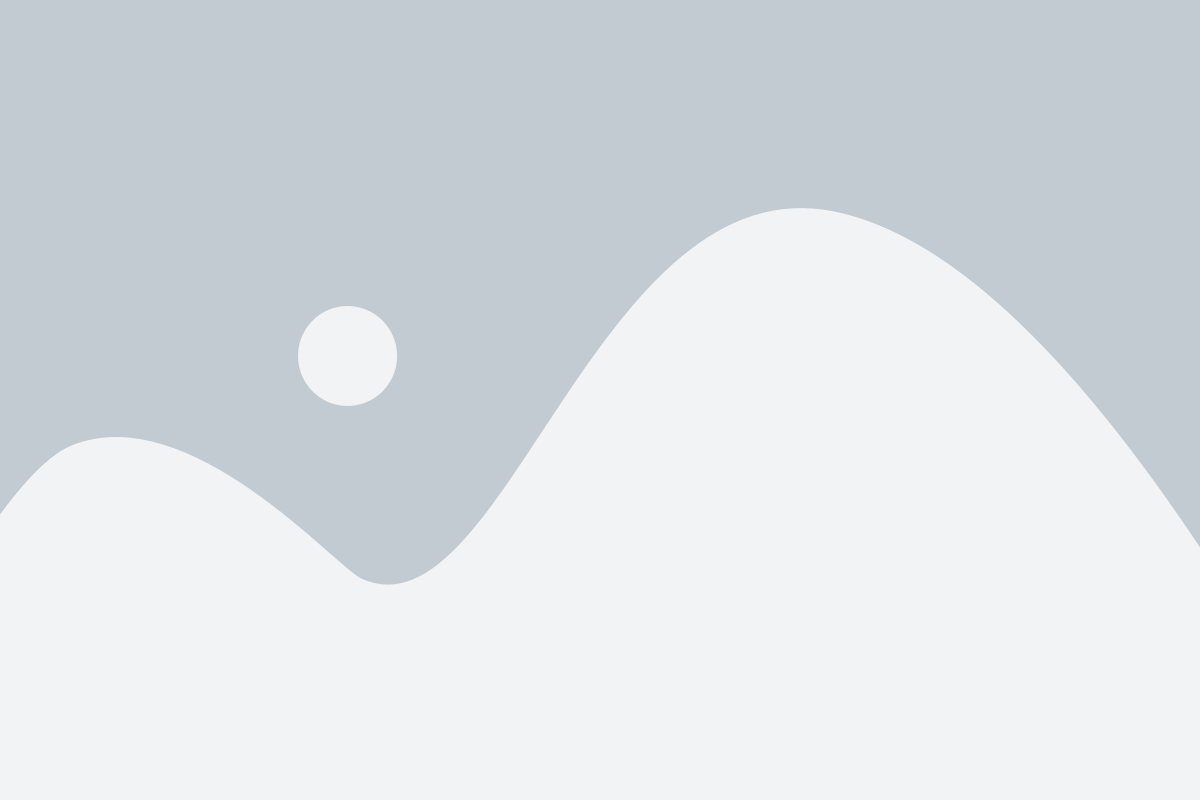
Flat Fillet Welding Position (1F)
In the 1F position, the plate lies flat, and the weld is applied to join two pieces of metal at a right angle. This position is commonly used in fabrication and construction industries for creating strong and durable joints.
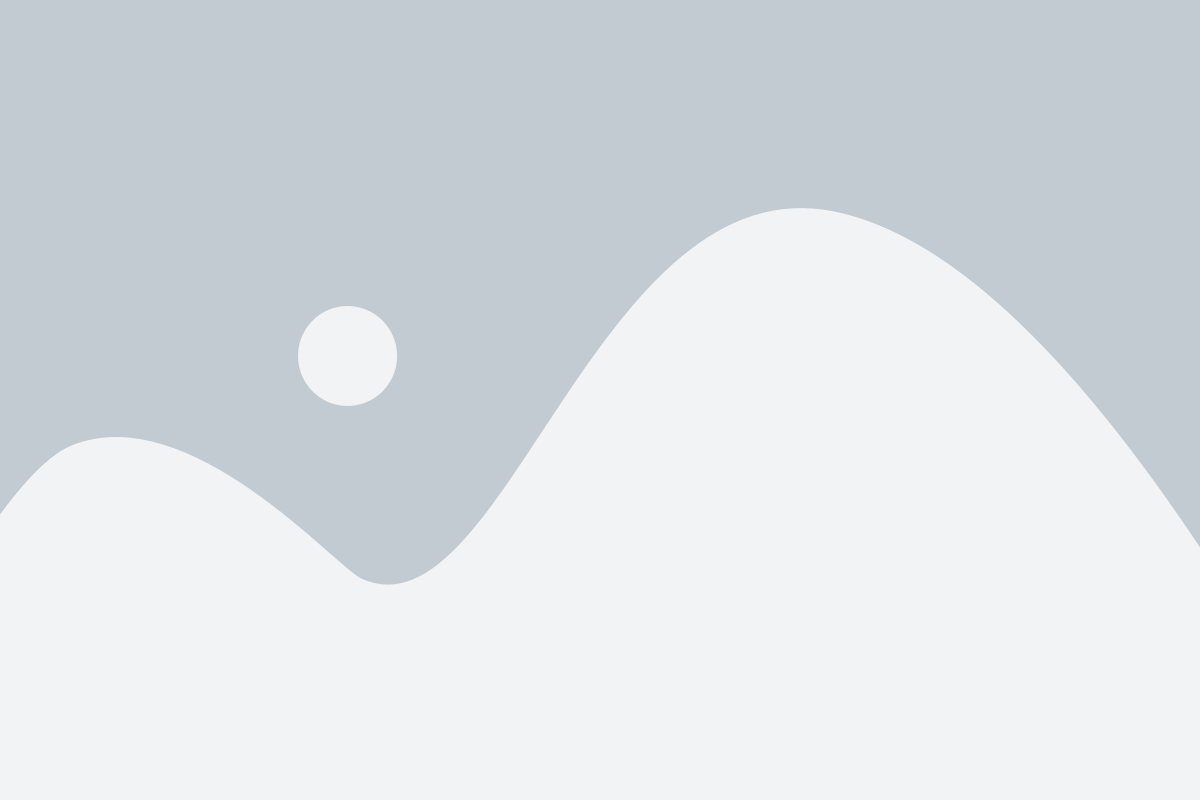
Horizontal Fillet Welding Position (2F)
Welding in the 2F position involves applying fillet welds horizontally on a plate. It is often used in structural steelwork, where the weld is placed on the upper side of the joint while the plate remains horizontal.
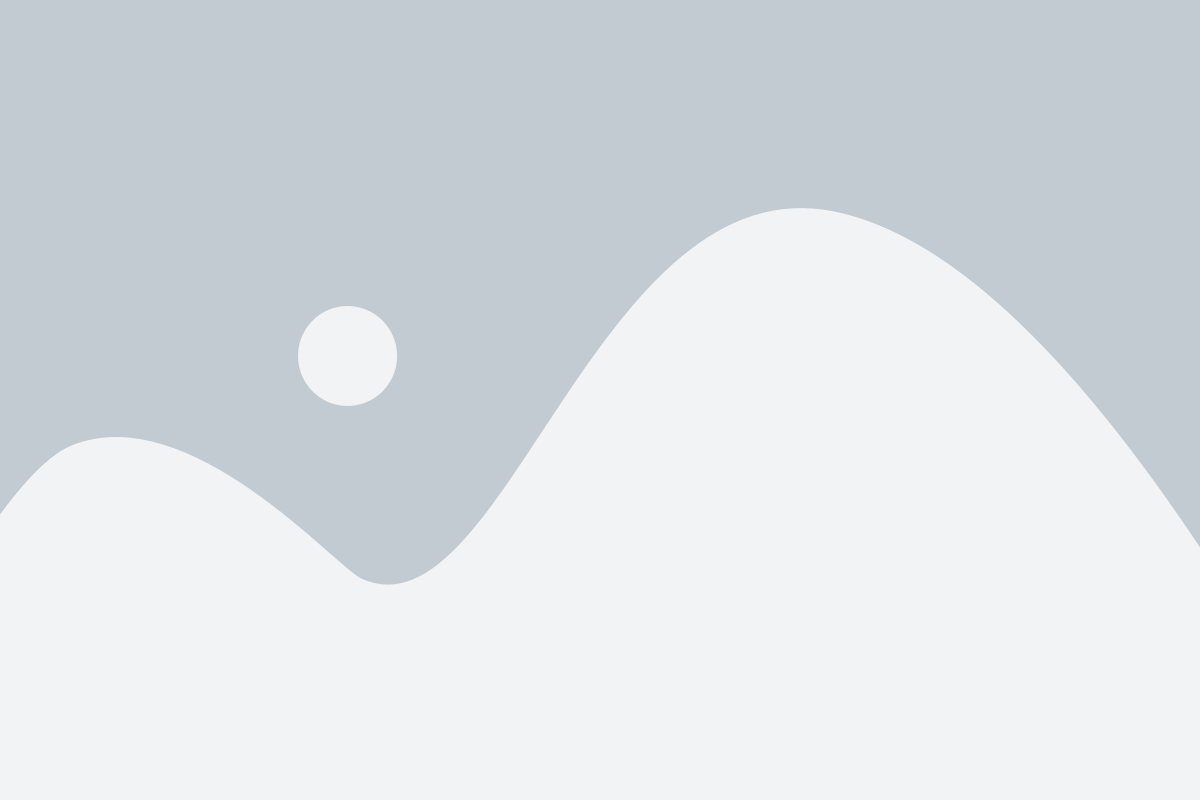
Vertical Fillet Welding Position (3F)
The 3F position requires welding fillet joints on a vertical surface. Welders work from the bottom to the top of the joint, ensuring proper fusion and penetration. This position is common in shipbuilding and bridge construction.
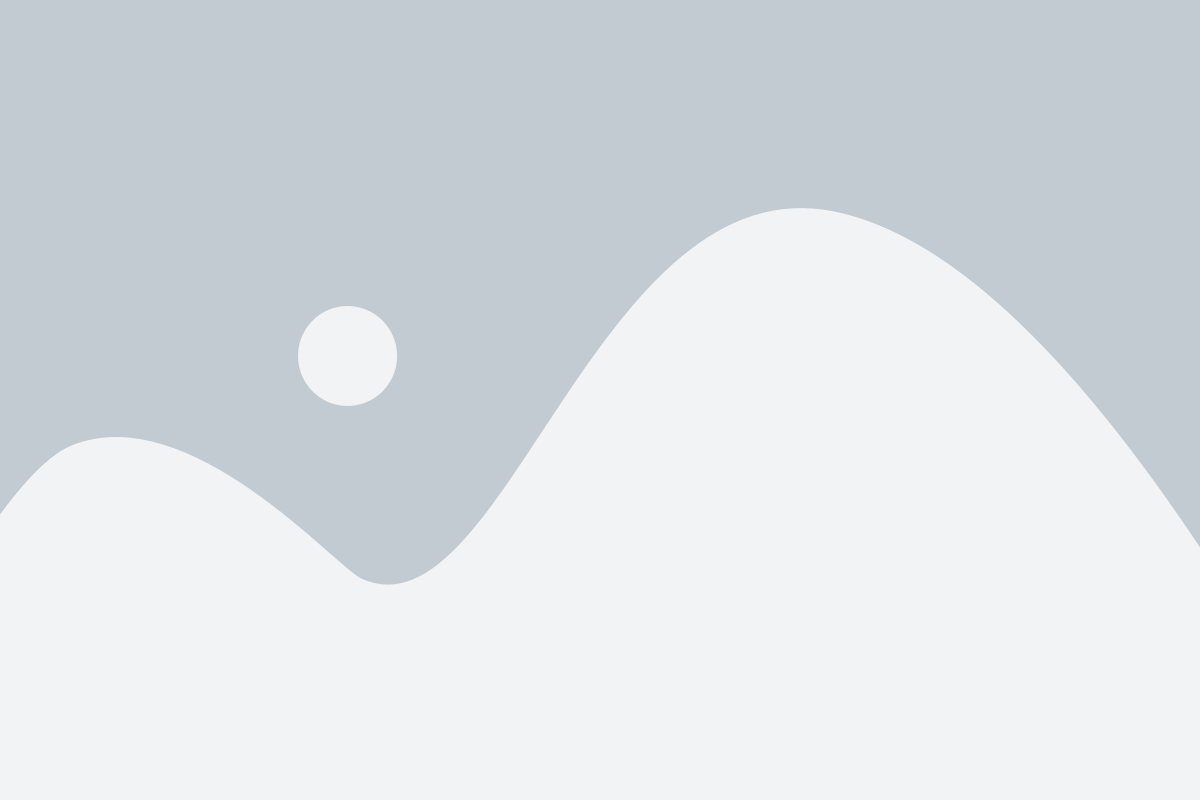
Overhead Fillet Welding Position (4F)
Welding in the 4F position involves applying fillet welds on the underside of a horizontal surface. It demands precise technique and control to prevent weld defects and ensure structural integrity.
Fillet Welding Positions for Pipe
Considerations for Pipe Construction
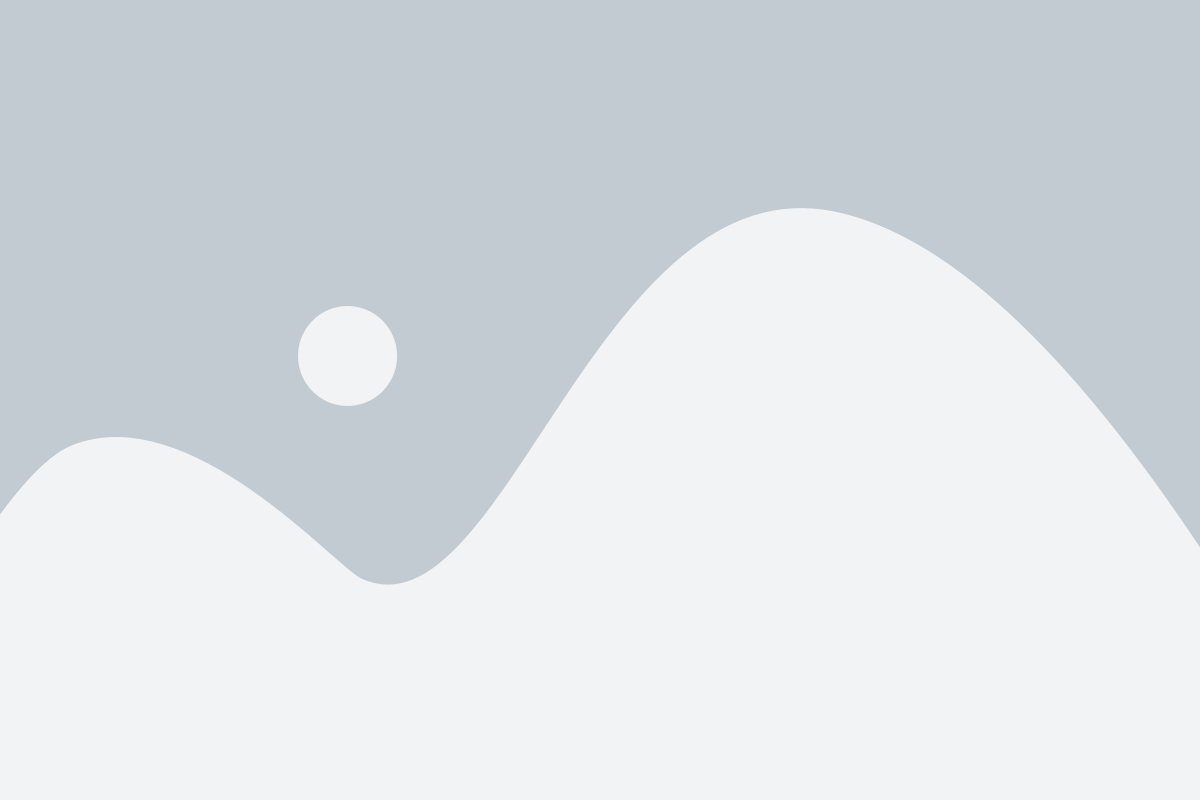
Flat Fillet Position (1F Rotated)
In pipe welding, the 1F Rotated position involves rotating the pipe while welding fillet joints on a flat surface. It is commonly used in pipeline fabrication and repair, requiring steady hand movements to maintain weld consistency.
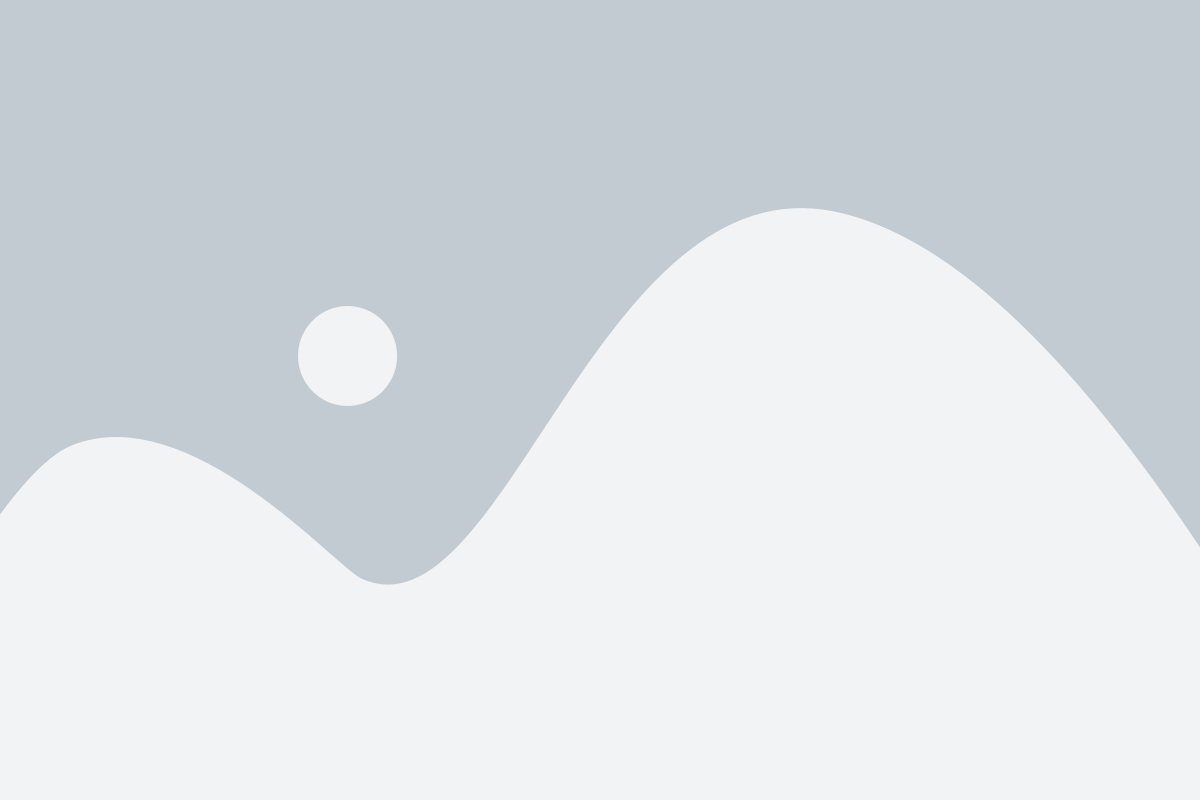
Horizontal Fillet Welding Position (2F)
Welding in the 2F position on a pipe involves applying fillet welds horizontally. The pipe may be rotated or fixed, and welders typically work from the side of the joint to create strong and durable connections.
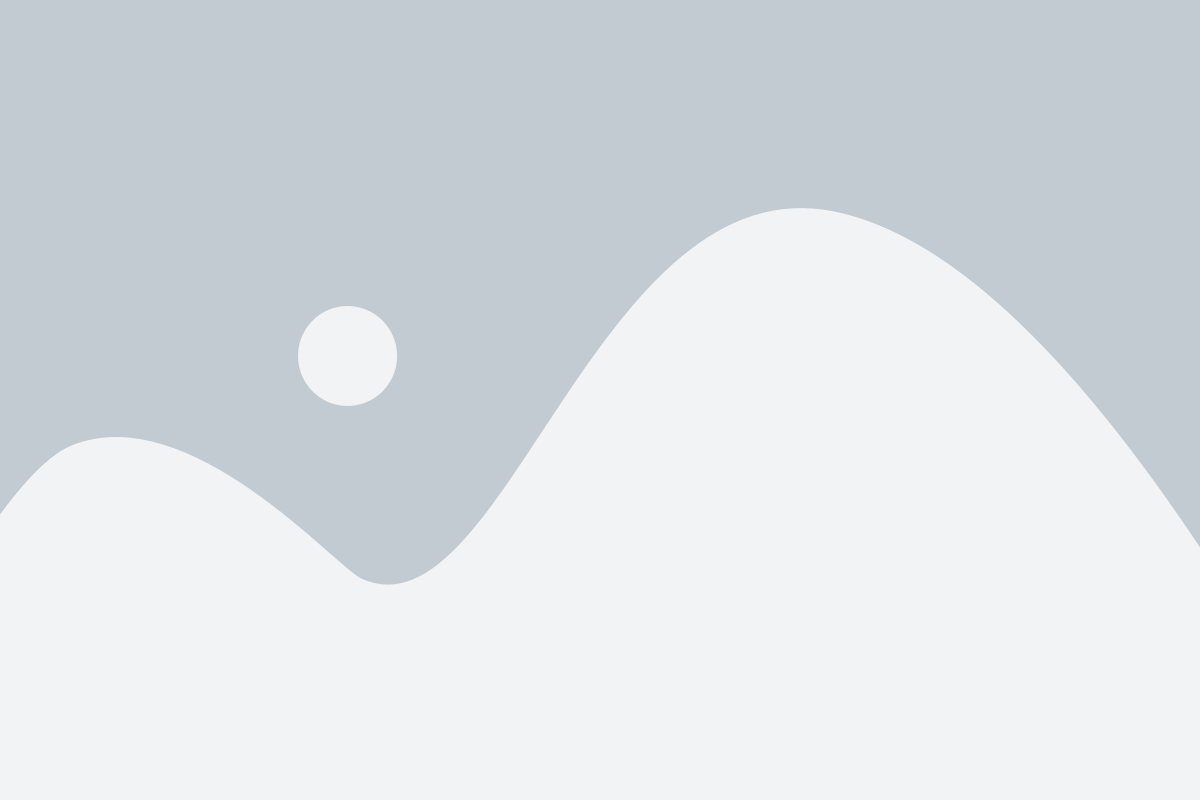
Horizontal Rotated Fillet Welding Position (2FR Rotated)
Similar to the 2F position, the 2FR Rotated position in pipe welding involves rotating the pipe while welding fillet joints horizontally. It is commonly used in pipeline construction and repair applications.
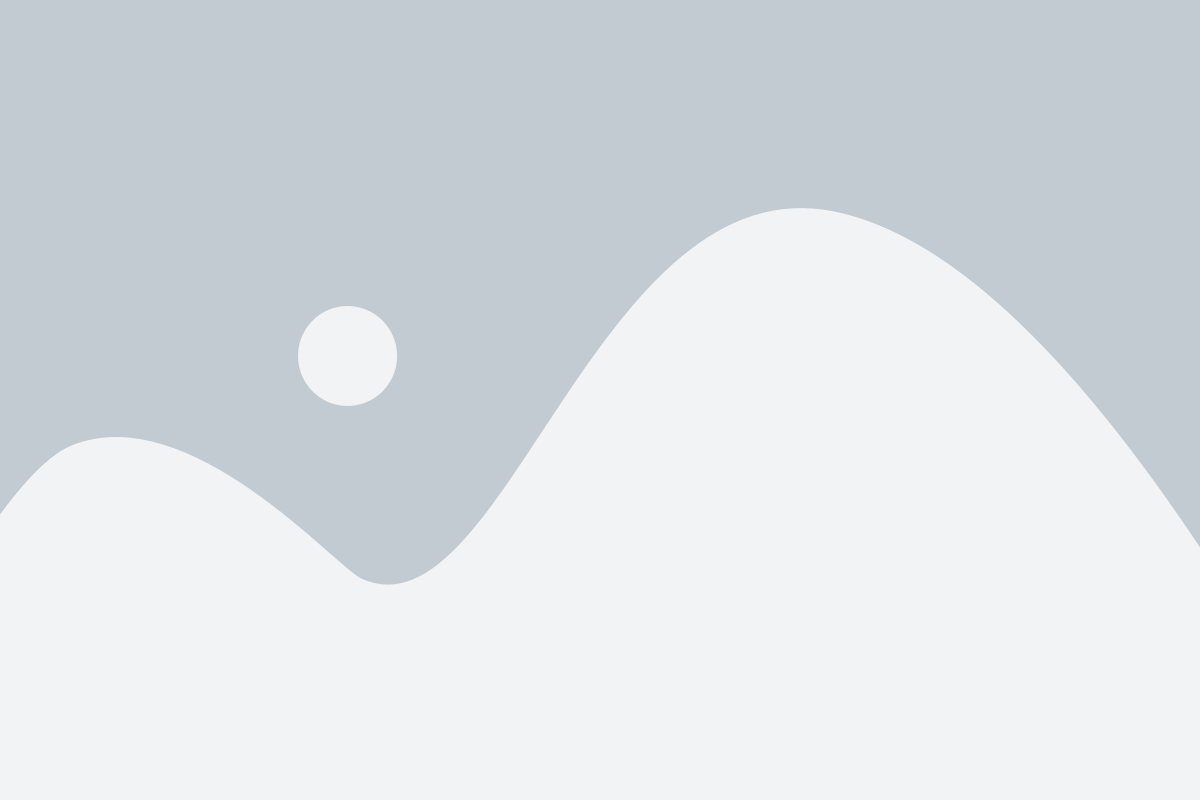
Overhead Fillet Welding Position (4F)
Welding in the 4F position on a pipe requires applying fillet welds on the underside of a horizontal pipe. It demands skill and precision to ensure proper fusion and penetration while working against gravity.
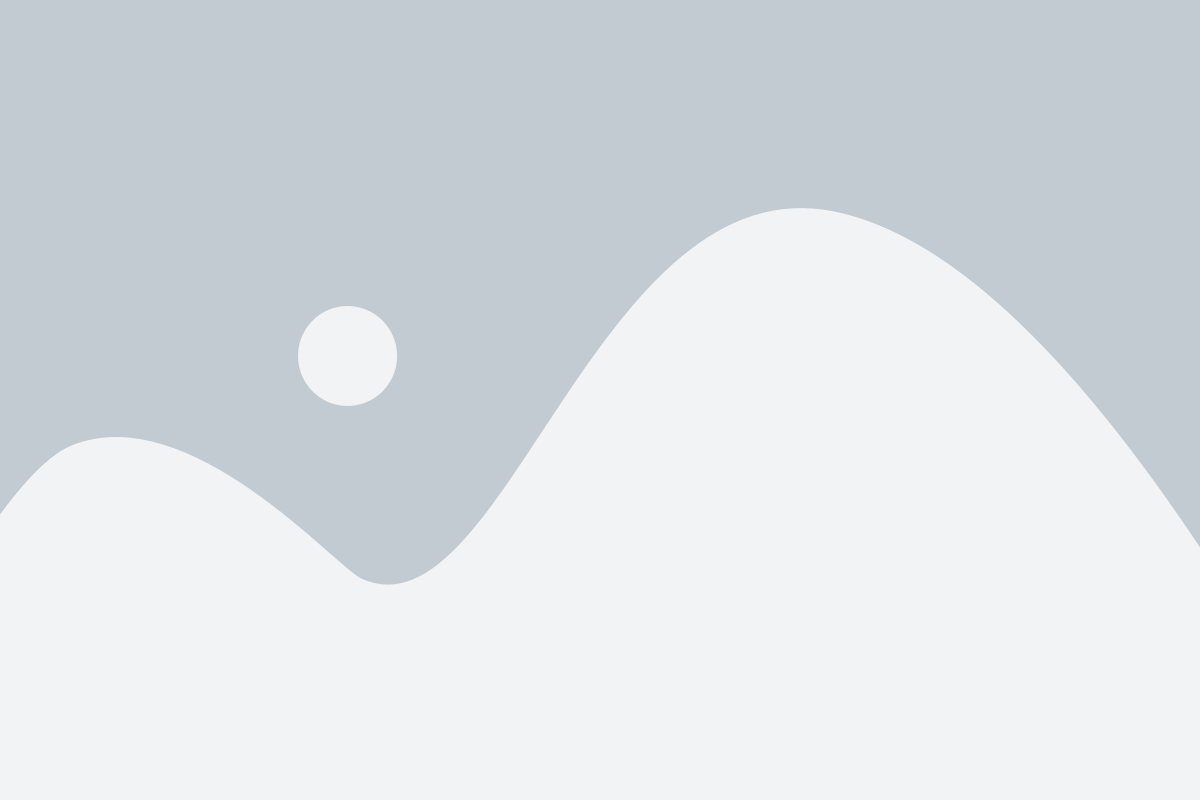
Vertical Fillet Welding Position (5F)
The 5F position involves welding fillet joints on a vertical pipe. Welders must work from the bottom to the top of the joint, ensuring consistent and uniform welds throughout the vertical length of the pipe.
Welding Positions for Stud
Application Specifics
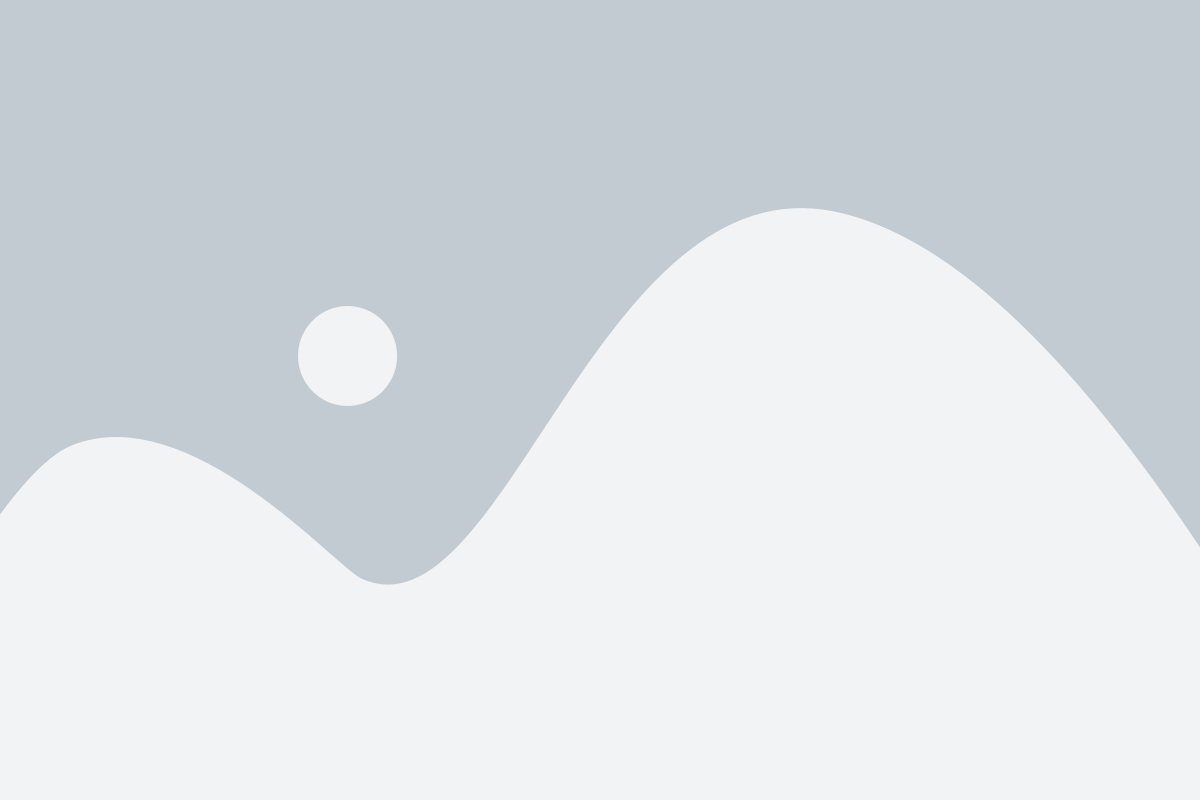
Flat Welding Position (1S)
The 1S position in stud welding refers to welding on a flat surface with the stud perpendicular to the workpiece. It is commonly used in applications where the stud needs to be welded onto a horizontal surface, such as in construction, shipbuilding, and automotive industries. Welders typically work from the top of the joint, ensuring proper alignment and penetration for a strong bond.
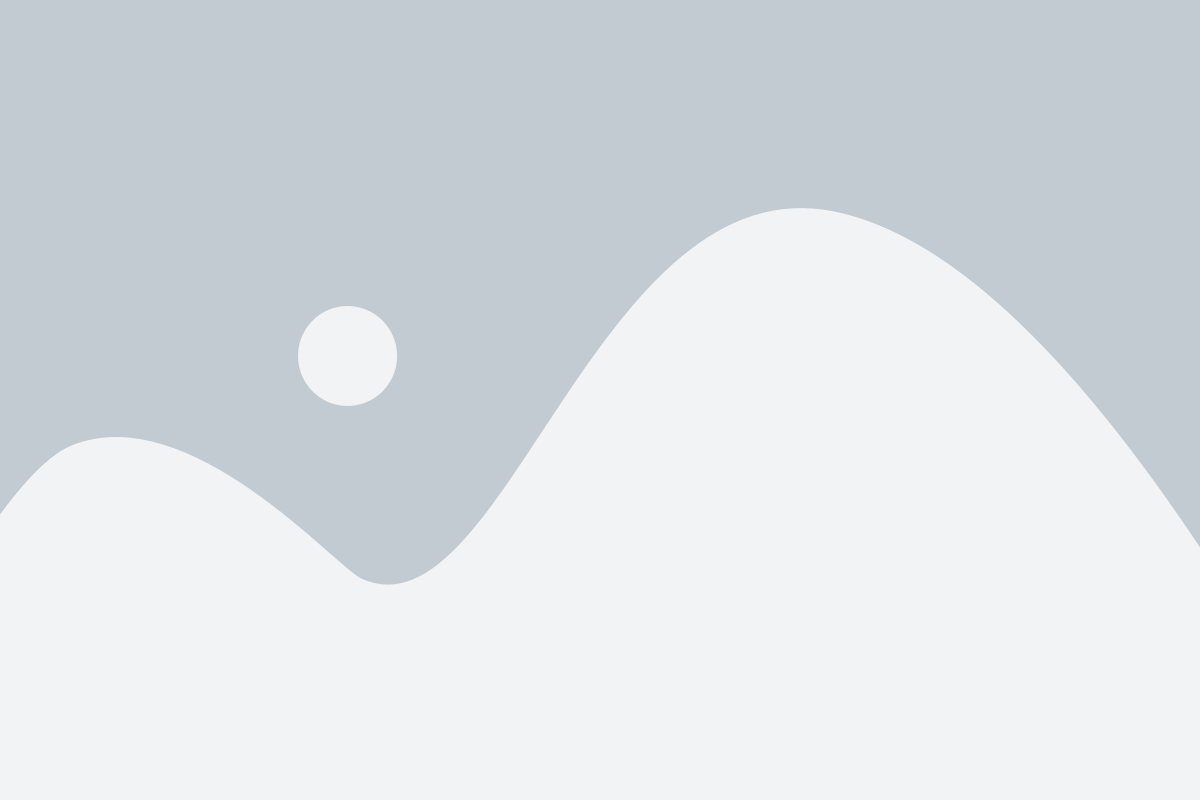
Vertical Welding Position (2S)
Welding in the 2S position involves welding studs vertically onto a workpiece. This position is often used in situations where studs need to be welded onto vertical surfaces, such as columns, beams, or walls. Welders must adjust their technique to ensure proper fusion and penetration, working from the bottom to the top of the joint to achieve a secure weld.
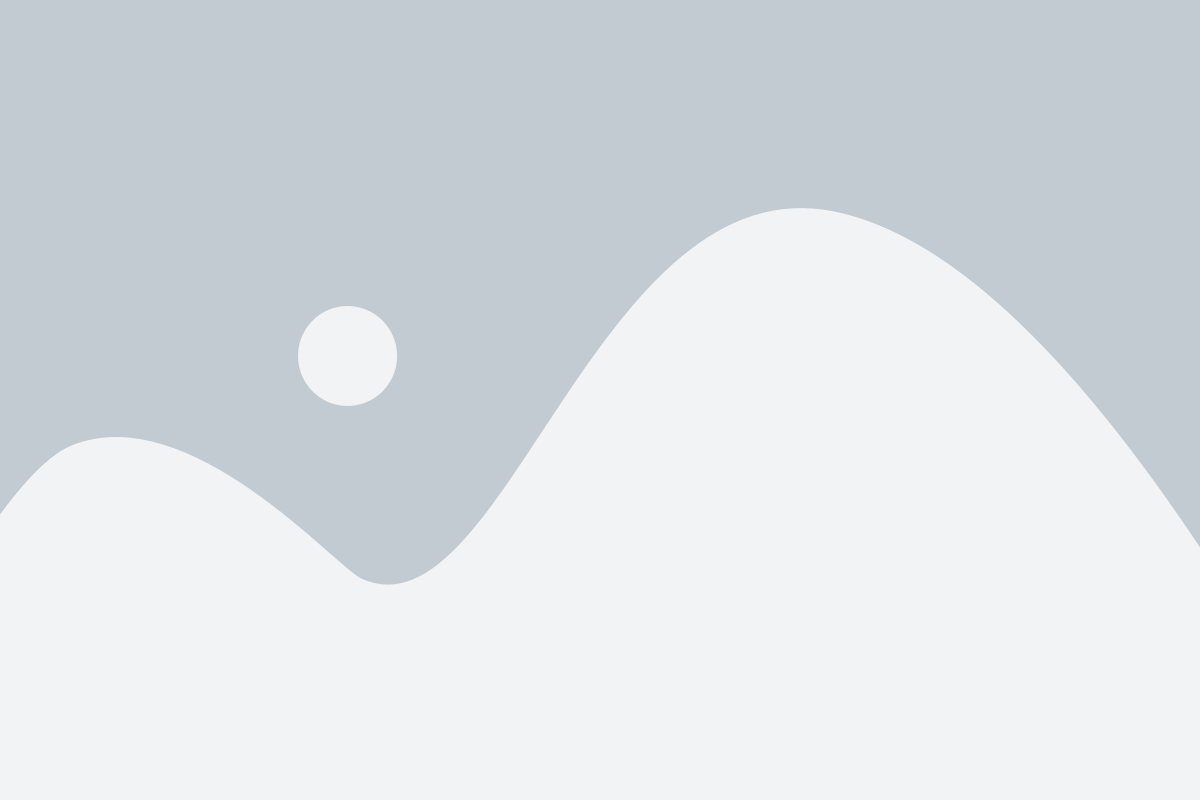
Overhead Welding Position (4S)
The 4S position in stud welding requires welding studs on an overhead surface, where gravity pulls the molten metal downward during the welding process. This position is challenging due to the risk of weld defects and spattering. Welders must employ precise technique and control to ensure proper fusion and penetration while working against gravity.