Introduction
Choosing the Right Technique
Welding techniques play a crucial role in achieving quality welds. Among these, two primary methods stand out are string and weave.
String technique involves moving the welding torch or electrode in a straight line along the joint, ideal for narrow welds or welding in tight spaces. On the other hand, weave technique involves moving the torch or electrode in a zigzag motion, widening the weld and ensuring better penetration and strength, suitable for thicker materials or larger joints.
Both techniques offer distinct advantages and are selected based on the specific requirements of the welding project. Understanding and mastering these techniques are essential for welders aiming for precision, efficiency, and superior weld quality.
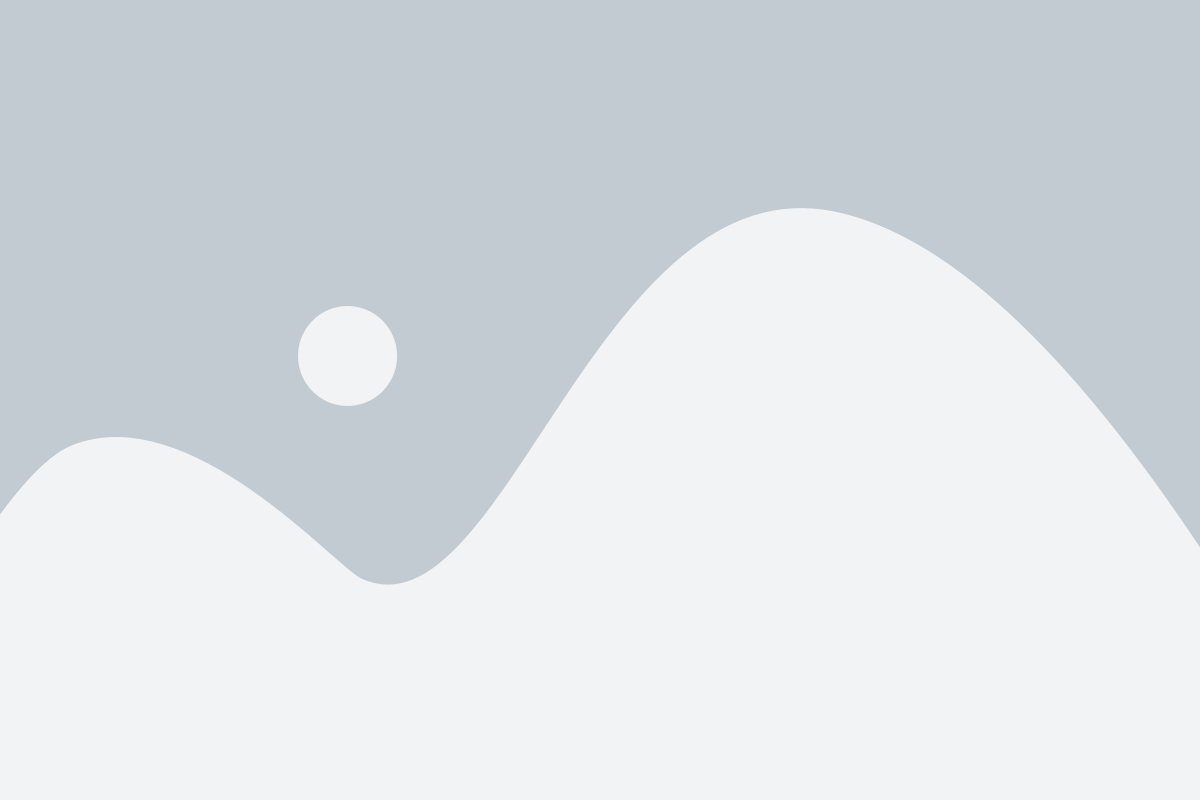
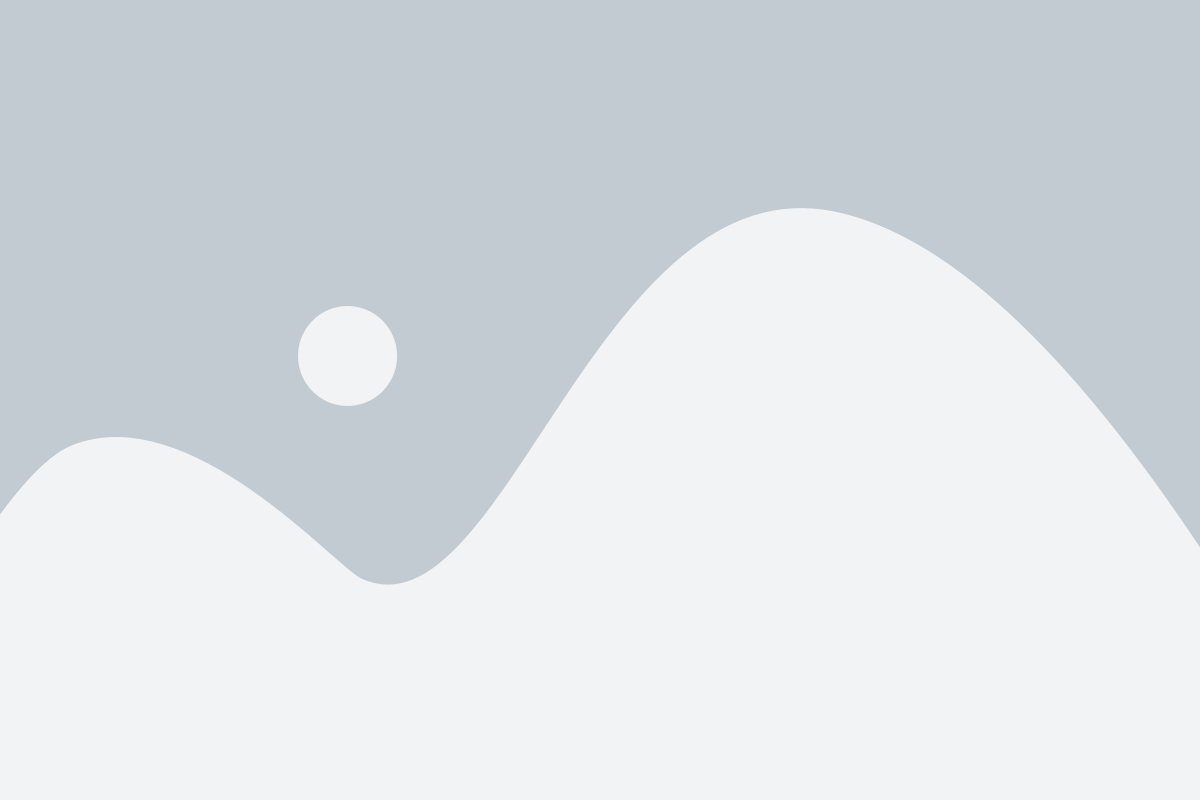
Importance of Welding Techniques
Efficiency Through Technique
Precision: Welding techniques ensure precise control over the deposition of filler material and the formation of weld beads, resulting in accurate weld profiles and dimensions.
Strength: Proper welding techniques optimize the bonding of base metals, enhancing the strength and structural integrity of welded joints.
Quality: By employing appropriate techniques, welders can minimize defects such as porosity, undercutting, and incomplete fusion, leading to high-quality welds.
Efficiency: Utilizing efficient welding techniques reduces the need for rework and enhances productivity, ultimately saving time and resources.
Versatility: Different welding techniques offer versatility in addressing various welding challenges, such as welding thin or thick materials, working in confined spaces, or achieving specific weld geometries.
Adaptability: Welding techniques can be tailored to suit different welding positions, joint configurations, and material types, ensuring adaptability to diverse welding scenarios.
Cost-effectiveness: Optimal welding techniques contribute to cost savings by minimizing material wastage, reducing labor expenses, and extending the service life of welded components.
Safety: Employing appropriate welding techniques enhances workplace safety by reducing the risk of weld defects, structural failures, and occupational hazards.
Compliance: Adhering to established welding techniques helps ensure compliance with industry standards, codes, and regulations, guaranteeing the integrity and reliability of welded structures.
Key factors
String Welding Technique
Material Thickness: Ideal for thinner materials, ensuring precise penetration without distortion.
Joint Configuration: Best suited for fillet and butt joints, maintaining uniformity and strength.
Weld Position: Suitable for flat and horizontal positions, optimizing bead appearance and quality.
Operator Skill Level: Beginner-friendly with straightforward motion, enhancing control and consistency.
Speed Control: Allows for controlled travel speed, preventing overheating and ensuring proper fusion.
Electrode Size: Compatible with smaller electrodes, facilitating intricate welds and detail work.
Heat Input: Low heat input minimizes distortion and warping, preserving the integrity of the workpiece.
Accessibility: Maneuverability in tight spaces, enabling precise welding in challenging environments.
Cost Efficiency: Requires minimal material and energy consumption, maximizing cost-effectiveness.
Versatility: Adaptable to various welding processes, including SMAW, GMAW, and FCAW.
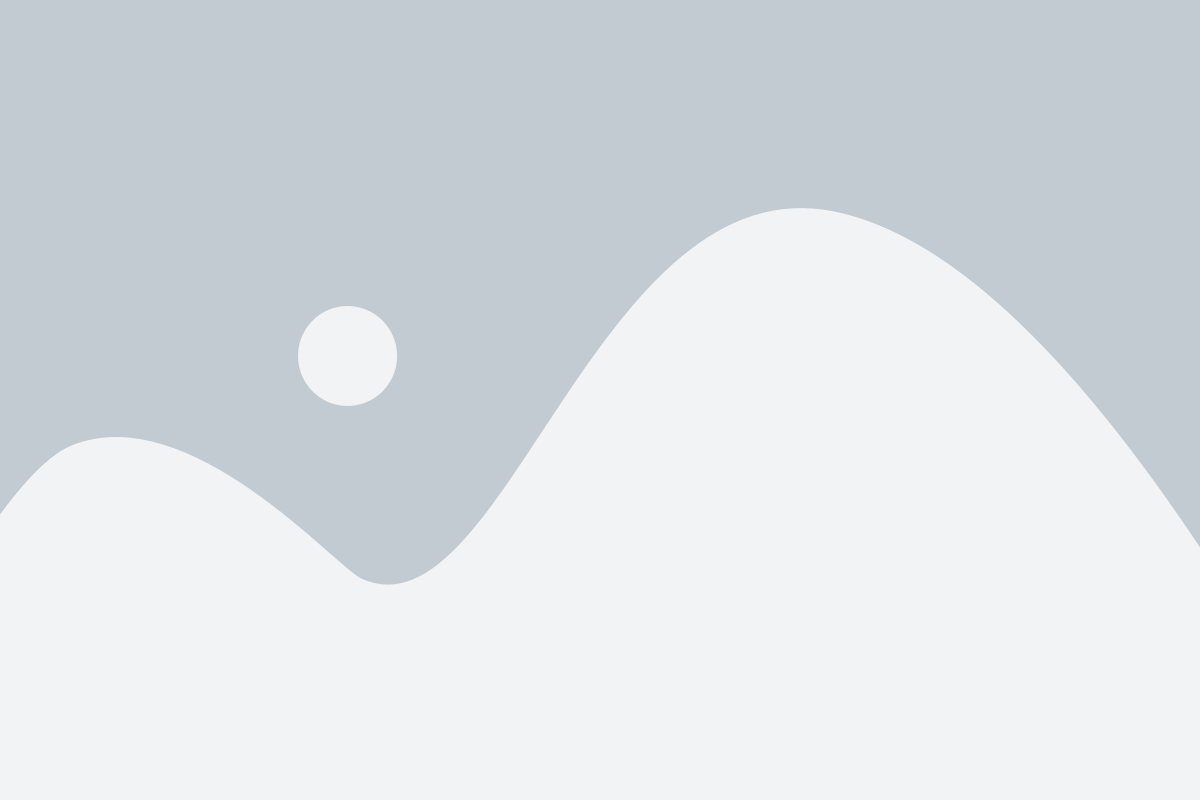
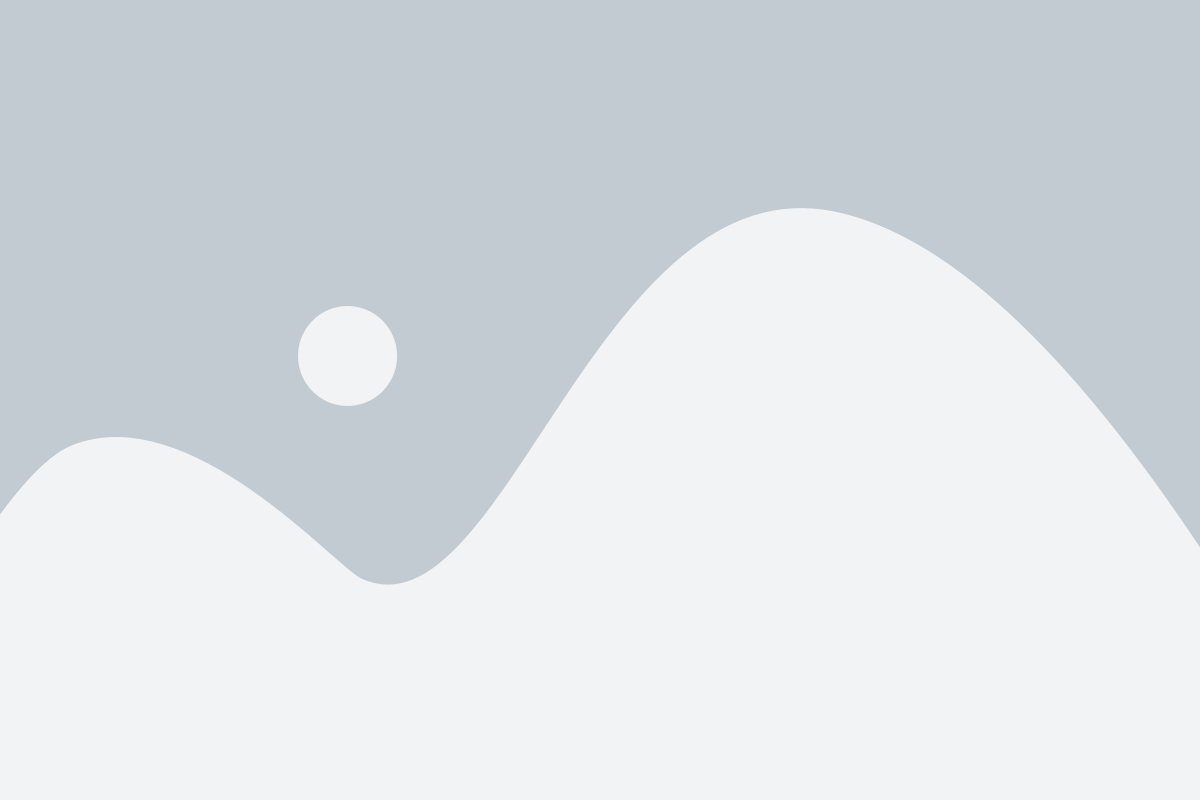
Key factors
Weave Welding Technique
Material Thickness: Ideal for thicker materials, ensuring proper fusion and penetration.
Joint Configuration: Well-suited for wide joints, providing ample coverage and reinforcement.
Weld Position: Versatile across all positions, offering flexibility and accessibility in various welding scenarios.
Operator Skill Level: Requires moderate to advanced skills, mastering the rhythmic side-to-side motion for optimal results.
Speed Control: Allows for controlled weaving motion, regulating heat input and preventing overheating.
Electrode Size: Compatible with larger electrodes, facilitating deeper weld penetration and deposition.
Heat Input: Moderate heat input balances penetration and bead appearance, minimizing distortion.
Accessibility: Maneuverability in open spaces, enabling efficient welding over larger surfaces.
Cost Efficiency: Provides efficient deposition rates, maximizing productivity and minimizing overall costs.
Versatility: Applicable across multiple welding processes, including SMAW, FCAW, and GTAW.
Difference Between
String vs. Weave
ASPECT | STRING TECHNIQUE | WEAVE TECHNIQUE |
---|---|---|
Motion | Straight, back and forth motion | Side-to-side weaving motion |
Application | Suitable for thinner materials and fillet welds | Ideal for wider welds and thicker materials |
Joint Configuration | Well-suited for narrow joints | Best for wide joints and larger surface areas |
Penetration | Provides uniform penetration | Facilitates deeper penetration and better fusion |
Speed Control | Requires consistent travel speed | Allows for controlled weaving speed |
Heat Input | Lower heat input, less risk of distortion | Moderate heat input, balanced penetration and bead appearance |
Operator Skill Level | Beginner-friendly, easier to control | Requires moderate to advanced skills |
Bead Appearance | Straight and uniform bead appearance | Rhythmic weave pattern, provides reinforcement |
Efficiency | Efficient for linear joints and thinner materials | Effective for wider joints and thicker materials |
Versatility | Limited adaptability for various joint configurations | Versatile across different joint types and positions |
Weld Width Control | Limited control over weld width | Provides control over weld width and reinforcement |